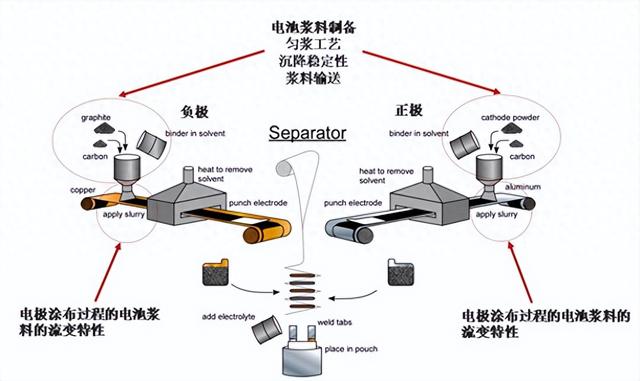
潜在失效模式
潜在失效后果
潜在失效起因/机理
现行预防过程控制
现行探测过程控制
混浆桶内浆料堆积于搅拌轴上
1.影响浆料固液比
因以高速混浆时间延长,以致浆料飞散,附着于轴上。
一个月清洗一次混浆桶
目视
2.黏度变化大
黏度计
搅拌转速不足
浆料不均匀
减速器故障
降低低速转速为50rpm以下
参数设定
混浆桶漏真空
浆料有气泡
真空管腐蚀
更换破损管件
真空计警报提醒
◇黏度过高
极板易拖尾, 正极拖尾导致安全性疑虑, 负极拖尾则无法焊接
粉体比表面积较大
添加NMP调整黏度
每批浆料检测黏度
◇黏度过低
成膜不易, 无法达到要求的重量
粉体比表面积较小
与下一批浆料混合
每批浆料检测黏度
◇分散不均匀
电池效能降低
搅拌时间不够
延长搅拌时间
每批检验粒径
浆料放置过久
规范浆料使用时间
若过期浆料必须重新检验其质量
涂布潜在失效模式
潜在失效后果
潜在失效起因/机理
现行预防过程控制
现行探测过程控制
浆料不足
影响产能
Sample run次数过多
订定每次Sample run的次数
浆料液位警报
混浆量预估错误
收集浆料使用历史, 回补正确的浆料
◎涂面有颗粒
颗粒出现, 局部材料堆积, 影响安全性
浆料颗粒聚集
于浆料过滤前加150μm的滤心过滤
目视
◎浆料中含有磁性材料微粒
于充放电时易出现锂金属沉机, 影响安全性
进料中的杂质料桶、管路的磨损
加入磁力吸附器、每隔400~600L清洗一次
清洗后吸附磁性物质称重计算含量
极板皱折
无法卷绕
张力左右不均
首件检查
目视
◎基重不稳定
有安全隐患
供料槽的浆料液面波动过大
加装液位感应器
首件/尾件秤重检查
◎正极偏重
有安全隐患
浆料沉降
加装回流管线
首件/尾件秤重检查
基重未确认
教育训练
首件/尾件秤重检查
◇正极偏轻
容量偏低
基重未确认
教育训练
首件/尾件秤重检查
伺服电机压力不够而引起刀表不稳定
教育训练,操作员工不可随意调节,由专门的设备人员调节
首件/尾件秤重检查
负极偏重
厚度偏大
浆料沉淀
搅拌棒重新设计后导入
首件/末件秤重检查
基重未确认
教育训练
首件/末件秤重检查
◎负极偏轻
有安全隐患
基重未确认
教育训练
首件/末件秤重检查
涂面两侧突起
极板易在收卷时累积厚度造成隆起断料
下刮板距离过大
涂布前, 量测下刮板与上档板的距离(上档板距离>下刮板)
目视
浆料与铜箔接触接口出现浆料内聚现象
于刮刀轮上加一PET film, 将浆料削薄
目视
浆料溢出挡板
1. 使涂轮寿命降低2. 浪费材料
泡棉失去弹性
每班更换泡棉
目视
极板出烘箱卷曲
无法生产
极板经烘烤后收缩
加装压轮
目视
极卷收料成喇叭状
影响生产速度
收料张力左右不均
极板重收
目视
辗压潜在失效模式
潜在失效后果
潜在失效起因/机理
现行预防过程控制
现行探测过程控制
◇极板不入规格
电池尺寸不符规格
压力与间隙调整不对
生产时给予8片极板试辗压
首件/末件及制程中检查
极板断裂
无法生产
极板出压轮时震荡太大
加装减震轮
目视
分条潜在失效模式
潜在失效后果
潜在失效起因/机理
现行预防过程控制
现行探测过程控制
◎毛边过大
低电压比例偏高电池受压易产生短路, 有安全性疑虑
刀片钝化
依分条长度收集毛边数据
首件/末件毛刺量测
荷叶边
造成极板不平整, 无法上自动卷绕
刀片钝化、刀片咬合深度不佳
裁刀已裁切米数记录管理
目视检查
断料
无法分条
1.接料没接好
教育训练
目视检查
2.极板破损未以胶带贴附
教育训练
目视检查
3.未被刀具裁断
发现后立即通知工程师
目视检查
收料不齐
1.自动卷绕良率低2.极板易受损, 间接影响电池寿命
1.收料铝圈没对位
教育训练
目视检查
2.断料后再接料
接料后用慢速运转, 直到收料整齐
目视检查
3.收料夹具打滑
铝圈固定后, 每个铝圈用手测试咬合状况
目视检查
正/负极板烘干潜在失效模式
潜在失效后果
潜在失效起因/机理
现行预防过程控制
现行探测过程控制
◇极板水分超标
寿命不佳
烘箱异常
每3小时检查烘箱的操作条件
首件测水份
烘干时间不够/温度偏低/真空度不够
教育训练
首件测水份
极板置于一般环境过久吸水
规范极板置于一般环境的时间
首件测水份
极板变脆
卷绕时极板断裂
实际烘烤时间过长、温度过高
每小时检查记录
自主检察
◇极板碰撞、散乱
极板破损,掉粉,
运输、拿取不当
放置于专用支架,整卷极板间加间隔环
目视
极耳焊接/裁切潜在失效模式
潜在失效后果
潜在失效起因/机理
现行预防过程控制
现行探测过程控制
金属柄裁短
插入长度短,与极板焊接面积小
sensor感应偏差,不灵敏。感应纸有污染
感应纸定期更换
每200个检查一次
来料有胶带接头、脏污
胶带上贴颜色标签,及时挑出
◎毛刺超过规格
短路、自放电大
切刀磨损
定期保养、寿命统计、毛刺检测SPC
首件检查毛刺、显微镜观察量测
◇焊接拉力小
内阻大,内阻不稳定、极耳脱落
焊靶磨损
寿命寿命监控焊接拉力spc趋势监控
每300个抽测焊接剥离力
焊接功率设定偏差
教育训练
PP film与极板距离偏大
露胶过长,影响pack长度
sensor感应偏差,不灵敏。感应纸有污染
感应纸定期更换
电芯全检
PP film与极板距离偏小
前侧封后没有露胶太短
sensor感应偏差,不灵敏。感应纸有污染
感应纸定期更换
电芯全检
◇焊接处与涂布距离偏差
影响电芯极耳间距
极板涂布长度、空白段的偏差
首件/每300个抽检
贴保护胶带潜在失效模式
潜在失效后果
潜在失效起因/机理
现行预防过程控制
现行探测过程控制
◇漏贴
焊接面刺穿隔膜,电池短路
送料干涉、切刀磨损
切刀寿命统计、更换
设备自动感应报警
◇长度不足
未盖住焊接面,隔膜被焊接处刺穿,短路
送料干涉(送料夹松动)、切刀磨损
切刀寿命统计、更换
◇贴偏、歪斜
未盖住焊接面,隔膜被焊接处刺穿,短路
送料干涉(送料夹松动)、切刀磨损
切刀寿命统计、更换
极板送料、裁切潜在失效模式
潜在失效后果
潜在失效起因/机理
现行预防过程控制
现行探测过程控制
裁斜
留箔偏短,不能焊接
极耳碰歪造成感应误差
教育训练
首件/每300pcs量测极板长度
◎极板裁切有毛刺
电池易短路,自放电高
裁切刀钝、上下切刀咬合不佳
切刀寿命统计、更换
每300pcs观察,SPC
◇切断位置落在涂布区
容量不足
涂布太长、太短
每300pcs观察
◇极板掉粉
电池易短路,自放电大
边缘碰撞
焊接前有刷极板机构
目视
极板粘结力差(如削头位置)
前段改善
目视
隔离膜切断潜在失效模式
潜在失效后果
潜在失效起因/机理
现行预防过程控制
现行探测过程控制
裁不断
机器操作中断
刀具钝化
统计寿命定期更换治具
首件检查
熔断温度低
首件点检、隔膜试切OK后才开始生产
首件检查
切边毛糙
外观不良
刀具钝化
定期更换治具,统计寿命
目视
熔断温度低
首件点检、隔膜试切OK后才开始生产
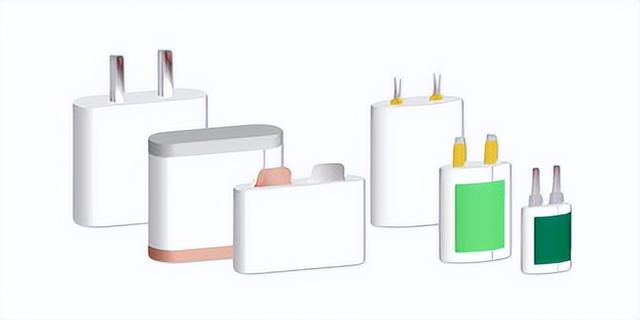
潜在失效模式
潜在失效后果
潜在失效起因/机理
现行预防过程控制
现行探测过程控制
卷止胶带贴歪
外观不良
胶带粘性强
全检
送料夹爪松动
定期检查保养
漏贴
电芯松脱
胶带粘性强
全检
送料夹爪松动
定期检查保养
◎卷绕不齐
容量低或者寿命差,易短路
纠偏不稳定
定期检查保养
每200颗检查一次对位
张力太小,极板送料偏移
送料夹爪松动
定期检查保养
极耳间距不合格
前封不良, 电池有胀气问题
焊接时ppfilm与极板距离有偏差
目视,全检
极耳PP胶高低不齐
影响前封露胶长度
卷绕对位偏差
目视,全检
◎隔膜抽芯
影响卷绕对位包覆外观不良
卷针调节不当
目视,全检
张力过大
目视,全检
尺寸不良
张力设定未最佳化
电芯烘干潜在失效模式
潜在失效后果
潜在失效起因/机理
现行预防过程控制
现行探测过程控制
◇电芯水分过高
寿命不佳
温度,时间及真空度不够
培训合格后上岗
自主检查
烘箱密封性不好
定期保养
电芯被吹散
隔膜碰皱
放气时气流过大造成
控制破真空时间
◇烘烤时间过久、温度过高
隔膜收缩,内阻大
温度设定太高
培训合格后上岗
自主检查
烘箱异常导致温度过高
定期保养
自主检查
电芯压平潜在失效模式
潜在失效后果
潜在失效起因/机理
现行预防过程控制
现行探测过程控制
电芯过压
极板内层断裂,容量低,内阻大
条件设错块规规格不对
培训合格后上岗
首件确认
电芯过厚
电池厚度超规格
条件设错
培训合格后上岗
◇极耳偏斜不居中
前封不良, 电池有胀气问题
电芯捏偏斜
培训合格后上岗
自主检查
电芯摆放倾斜
培训合格后上岗
自主检查
卷绕后极耳不居中
培训合格后上岗
自主检查
短路测试潜在失效模式
潜在失效后果
潜在失效起因/机理
现行预防过程控制
现行探测过程控制
电压设定过大
电池失效,隔膜击穿
操作失误
在设置面板的规定电压处用颜色箭头标示
首件确认参数
电压设定小
有短路疑虑之电池漏检
操作失误
在设置面板的规定电压处用颜色箭头标示
首件确认参数
内阻值设定小
有短路疑虑之电池漏检
操作失误
在设置面板的电阻设定按钮处,指定数值;用标准件再确认
首件确认参数,
表笔没有同时接触到极耳
有短路疑虑之电池漏检
操作失误、员工操作速度过快漏失
接万用表声音提示是否接触好
声音报警
铝袋成型潜在失效模式
潜在失效后果
潜在失效起因/机理
现行预防过程控制
现行探测过程控制
外观皱褶/破损
密封性差
模具表面粗糙、有异物粉尘
目视检查
外观检查
深度尺寸不符
电池外观差
模头调整不正确
首件检查
生产200个检查一次
前封处距离超出规格
电池长度不符规格
裁刀偏斜
首件检查
生产200个检查一次
前侧封口潜在失效模式
潜在失效后果
潜在失效起因/机理
现行预防过程控制
现行探测过程控制
◇封口厚度不良
电池漏液、胀气
封口温度异常
每班作业前实测量测封头温度。
首件真空测漏 测封口区厚度
封口压力及加压时间异常
每批作业前点检压力及时间,导入限位机构,可防止过压偏薄
自主检查
上下封头水平异常
每批首件检查封头水平度,导入限位机构
自主检查
封头磨损
封头连续生产100K必须卸下清洁保养。不连续生产时每次卸下均需清洁,每次装上时需确认封头尺寸
自主检查
◇侧封有皱折
密封性变差
侧封时上下铝袋不平行:-铝袋深度不够-电芯厚度大
铝袋成型后检查深度电芯入袋后不可放置过久才入袋封口
自主检查
封口温度异常
每班作业前用热电偶实测封头温度及做测漏试验
自主检查
封边不齐
外观差
铝袋对折位置不当
教育训练
外观检查
Al/Ni错位
正负极反向
电芯入袋放反
教育训练
外观检查
前封溢胶过长
打PACK后长度超规
前封温度过高
每班作业前模治具调整后量测封头温度及做测漏
外观检查
前封露胶过短
封口短路、极耳回折短路
电芯的pp胶与极板间距小
外观检查
极耳不居中,不入凹槽
密封性差
极耳未整理不平行
封头增加压极耳机构
外观检查
电芯极耳不居中
目视检查
外观检查
短路测试潜在失效模式
潜在失效后果
潜在失效起因/机理
现行预防过程控制
现行探测过程控制
电压设定过大
电池失效,隔膜击穿
操作失误
在设置面板的规定电压处用颜色箭头标示
首件确认参数
电压设定小
有短路疑虑之电池漏检
操作失误
在设置面板的规定电压处用颜色箭头标示
首件确认参数
内阻值设定小
有短路疑虑之电池漏检
操作失误
在设置面板的电阻设定按钮处,指定数值
首件确认参数
表笔没有同时接触到极耳
有短路疑虑之电池漏检
操作失误、员工操作速度过快漏失
接万用表声音提示是否接触好
声音报警
表笔没有同时接触到极耳、铝袋切面
有封口短路疑虑之电池漏检
操作失误、员工操作速度过快漏失
探测指针刺破铝袋确保接触良好
中型电池与指定型号全检,一般性小电池每批首件检验。电阻值规格提高到60GΩ。
注液潜在失效模式
潜在失效后果
潜在失效起因/机理
现行预防过程控制
现行探测过程控制
◇注液量少
电池容量低,内阻大, 寿命差
注液输送管路中有气体
首件检查注液桶抽真空
生产200个抽测4pcs(前后注液针头各2pcs)注液量。视产品需要可以导入100%称重注液机。
注液量调错
首件检查
海霸泵异常
每月定期保养
注液量过多
去气量大造成外观差
海霸泵异常
首件检查
注液量调错
首件检查
注液输送管路中有气体
首件检查注液桶抽真空
◇注液封口不良
漏液、胀气、寿命差
封口温度,压力,时间,平行度异常
每批作业前点检温度、压力、时间及封头平行度
首件真空测漏 测封口区厚度
未注液就封口
电池无电压,内阻
注液管未插入袋中
作业中检查
生产200个检查一次注液量
海霸泵不作动,PLC失效
设备定期保养
生产200个检查一次注液量
外观有伤痕
外观差
电池上夹具时易摩擦到夹具内壁
无
外观检查
胶态电解液配液搅拌不均匀
电池性能不佳
搅拌时间不足
时间记录点检
搅拌完成后进行胶化检验
喷印潜在失效模式
潜在失效后果
潜在失效起因/机理
现行预防过程控制
现行探测过程控制
凹点
外观差
手中拿得太多造成或放电池时用力过猛造成
每次拿不得超过3PCS,轻拿轻放
外观检查
划伤
外观差
电池放置位置错误, 直接在皮带上转动电池
教育训练
外观检查
脏污
外观差
传送带脏污
定期清洁,擦拭作业通道和输送带
外观检查
喷码内容错误
不能正确标示生产信息
信息输入错误
喷印信息与制程卡核对
首件检查
喷码位置偏斜
外观差
电池放置位置歪斜
教育训练
外观检查
化成潜在失效模式
潜在失效后果
潜在失效起因/机理
现行预防过程控制
现行探测过程控制
◇流程参数错误
电池性能不佳
发送前检查不到位
教育训练作点检记录,QA巡检
下架统计每颗电池电压
未预充
重工,浪费工时
极耳与夹子接触不良
夹子每月保养一次
设备和软件有检查功能
漏发流程
发送流程后及时点检及确认
下架统计每颗电池电压
划伤及凹点
外观差
老化板PET膜脏污及夹电池时摩擦老化板
老化板每月清理一次,每次上架时清理一次老化板,PET膜脏污及时更换;中型电池在注液后表面贴膜保护。
外观检查
喷印模糊
不能正确标示生产信息
预充下架时手法过重,导致喷印面与老化板摩擦
教育训练下架时轻取轻放
外观检查
电池短路
电压低
正负极极耳弯曲接触
上、下架时把导柄整理直放摆好
观察极耳有无焦黑
极耳夹伤
极耳易断裂
极耳的夹子夹在隔片上
教育训练
极耳外观检查
电池压平潜在失效模式
潜在失效后果
潜在失效起因/机理
现行预防过程控制
现行探测过程控制
电池过压
电池性能变差或丧失功能
时间,压力,颗数参数错误
点检参数设置
首检测电池厚度
有凹点,凹痕
外观差或报废
电池表面有粉尘沾附(粉尘来源在周转盘)
周转盘每周清理一次;中型电池在注液后表面贴膜保护
每生产100件时检测一次外观
上下模表面有脏污
每压一次以无尘布擦拭上、下模表面
电池漏压
厚度超标
有压与未压电池混料
标识明确,并标示摆放位置
每批纪录电池厚度
胶化潜在失效模式
潜在失效后果
潜在失效起因/机理
现行预防过程控制
现行探测过程控制
胶化温度不正确
电性能不佳
设备功能异常
设置温度报警
每批点检确认
胶化时间不足或过长
电性能不佳
时间设置错误
设备自动到时报警并关机,增加额外时间报警器
每批点检确认
夹板压力偏小
电池厚度偏大
气缸压力设置不正确
点检参数设置
每批点检确认
夹板压力偏大
电池过压
气缸压力设置不正确
点检参数设置
每批点检确认
去气封口潜在失效模式
潜在失效后果
潜在失效起因/机理
现行预防过程控制
现行探测过程控制
◇封口不良
胀气,电池漏液
teflon胶带变形
采用限位封头
1.首件测漏2.测封口厚度3.外观检查
前后封头不平行
感应纸测试平行度
热封温度错误
每班作业前量测封头温度
沾电解液
外观差
电池凹槽垫片使用错误
严格按工艺要求设定参数
外观检查
清洁不及时,导致二次污染
若发现电池沾附电解液, 则立即以酒精擦拭设备;中型电池在注液后表面贴膜保护
外观检查
裁边潜在失效模式
潜在失效后果
潜在失效起因/机理
现行预防过程控制
现行探测过程控制
铝袋断面不平整
影响外观
裁刀钝
每月刀具保养
外观检查
机器调整不当,裁刀与底模间隙过大
调整设备后以铝袋测试确认
外观检查
短路
电压低
电池接触到刀具凹槽金属
作业前检查铁氟龙绝缘胶带是否贴好
极耳焦黑检查
凹点,凹痕
外观差
托料板螺丝松动
用红色胶带标示螺丝位置, 并每日确认是否松动;中型电池在注液后表面贴膜保护
每做200个检查一次外观
裁边模表面有异物,不平整
铁氟龙胶带每周更换一次,每生产100个擦试一次上下模
每做200个检查一次外观
折边潜在失效模式
潜在失效后果
潜在失效起因/机理
现行预防过程控制
现行探测过程控制
电池压伤
电压低,内阻高
电池未放入槽中
教育训练
外观检查
短路
电压低
电池接触到刀具凹槽金属
每周更换铁氟龙
极耳焦黑检查
电池极耳相互接触
两电池的极耳向相反方向放置
有凹痕
外观差
模具表面不平整,有异物
定期检修模具
外观检查
◇折边处挤压破损
电池漏液、胀气
厚薄片边缘不光滑
在厚薄片两面贴teflon胶带
每做200个检查一次外观
电池宽度大,和折边模具不匹配
封口边过封,铝袋内层溢胶多,对折边挤压时导致破损
导入去气限位封头和导R角
首件检验封口厚度
分容潜在失效模式
潜在失效后果
潜在失效起因/机理
现行预防过程控制
现行探测过程控制
短路
电压低
电池夹反造成短路
上架前自检喷印面
每颗电池活化后数据记录与筛选
夹子隔片断,极耳接触
上架前检查夹子隔片,损坏及时更换
上下架极耳同时碰到夹子金属处
夹子处贴美纹胶带
正负极极耳碰到一起
上下架时极耳整直
极耳焦黑检查
划伤
外观差
老化板PET膜脏污及夹电池时摩擦老化板
老化板每月清理一次,每次上架时清洁老化板
外观检查
未活化
重工,浪费工时
极耳与夹子接触不良
发送流程后及时点检及确认,软件界面检查
活化后全检内阻电压和容量
漏发流程
发送流程后及时点检及确认,QA巡检
活化后全检内阻电压和容量
活化参数错误
容量数据不正确
发送前没有仔细检查或未检查
教育训练
每颗电池纪录活化结果
喷印信息模糊
不能正确标示生产信息
下架时手法过重
下架时轻取轻放
外观检查
极耳夹伤
极耳易断裂
极耳的夹子夹在夹子的隔片上
教育训练
极耳外观焦黑检查
极耳清洁损伤
极耳易断裂
用砂纸打磨拉扯导致磨花变脆
改用塑料头打磨轮清洁极耳
限度样本比对做外观检查
Al/Ni裁切潜在失效模式
潜在失效后果
潜在失效起因/机理
现行预防过程控制
现行探测过程控制
短路
电压低
底模未做好绝缘保护
1.交接班前确认贴好绝缘胶带2.切前整平极耳再装盒
极耳外观焦黑检查
长度尺寸不良
不易与PCM焊接
机台调整的尺寸未达到标准
首件检查
每四盒测量一次
刮伤,凹痕
外观差
机台表面上未做好清洁
每做2盒用无尘布擦拭机台与电池表面接触部位
外观检查
Al转Ni焊接潜在失效模式
潜在失效后果
潜在失效起因/机理
现行预防过程控制
现行探测过程控制
短路
电压低
焊头,底模未做好绝缘保护
作业前确认绝缘胶带是否贴好
外观检查
电池正负极极耳接触
焊接后极耳拉直,每盘之间错开放置
外观检查
B段尺寸不良
极耳难焊接PCM
治具位置调节不当
教育训练
每生产100个测量焊接点位置
焊断
极耳断, 电池失效
焊接头下降距离太深
焊头下压限位
每200件测试剥离力
焊接功率不稳定、过大
制作过程需注意极耳焊接情形
每200件测试剥离力
◇焊接不牢,易脱落剥离
无法与PCM焊接
焊接功率不稳定
制作过程需注意极耳和接情形
每200件测试剥离力
折极耳潜在失效模式
潜在失效后果
潜在失效起因/机理
现行预防过程控制
现行探测过程控制
极耳至铝袋gap小
弯折时刺破铝袋
操作手法错误
采用治具操作(gap片0.60mm)
GO/NOGO塞尺全检
极耳歪斜
内外八,极耳间距不良
操作手法错误
教育训练
目视检查
于焊接处弯折
铝转镍处断裂,电池不可使用
铝裁切时偏短
控制铝裁切尺寸
目视检查
点胶潜在失效模式
潜在失效后果
潜在失效起因/机理
现行预防过程控制
现行探测过程控制
极耳上沾胶
外观不良
操作手法错误,点胶拖尾
气压方式控制流量
目视检查
点胶面积不足
固定不牢
操作手法错误
教育训练
目视检查
整形潜在失效模式
潜在失效后果
潜在失效起因/机理
现行预防过程控制
现行探测过程控制
短路
电压低
机台未做好绝缘
交接班前确认贴好绝缘胶带
极耳外观焦黑检查
取放过程正负极极耳接触
整边前先整理极耳再作业
间距设置不当
尺寸不符合标准、外观变形,极板受挤压
调节间距调节不当
首件检查
每批首件和每生产200个测量宽度
高温老化潜在失效模式
潜在失效后果
潜在失效起因/机理
现行预防过程控制
现行探测过程控制
◇温度偏高
电池性能不佳
设备异常
温度超出规格自动报警
厂务每2小时巡检一次
◇温度偏低
不良电池漏检
设备异常
温度超出规格自动报警
厂务每2小时巡检一次
◇老化时间过短
不良电池漏检
检查不到位
同一天出老化之所有批号用美纹胶带捆扎,标示日期
老化时间点检记录,同时制程卡上记录
老化时间过长
电池性能不佳
检查不到位
老化时间点检记录,同时制程卡上记录
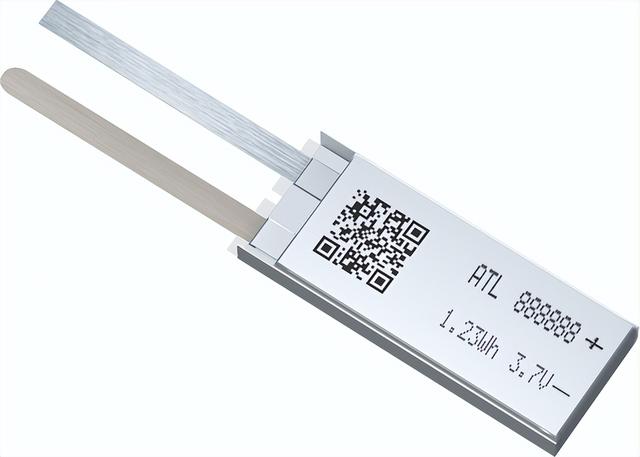
潜在失效模式
潜在失效后果
潜在失效起因/机理
现行预防过程控制
现行探测过程控制
刮伤
外观差
Cell宽厚GO/NOGO治具上有异物所造成
交接班时擦拭治具
外观检查
短路
电压低
测量极耳时手法不正确
操作员培训合格后上岗
极耳外观焦黑检查