
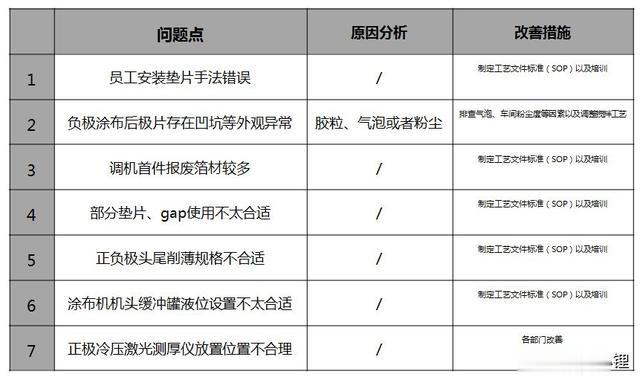
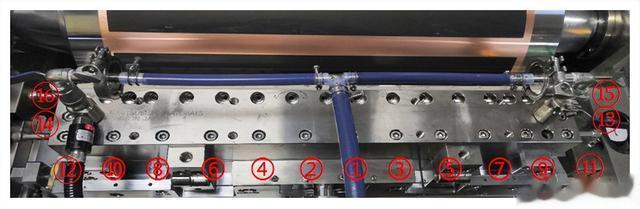
现象描述
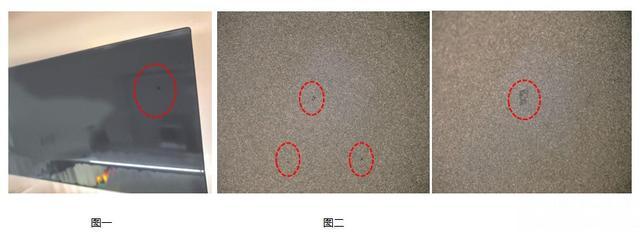
如图一所示,在机头湿膜上存在明显可见的凹坑(5cm*5cm上存在10个左右,直径0.5mm~1mm)
如图二、三所示,冷压后取样,在CCD下观察,可见明显微观状凹坑( 5cm*5cm存在15个左右)
机理分析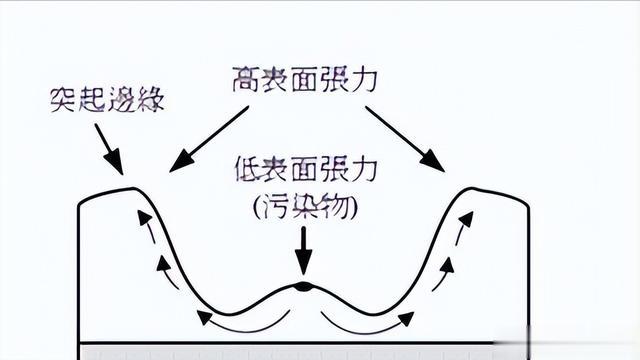
缩孔现象产生根本原因为表面张力的变化造成,极片出现凹坑位置的表面张力发生变化,造成局部力的不平衡,因此产生缺陷。力的变化可以参考上图。
改善措施
优化浆料工艺,适当提高转速和延长搅拌时间等,提高浆料一致性优化制胶工艺,适当提高转速和延长搅拌时间等,减少PVDF的团聚优化粉尘洁净度,减少污染物或者粉尘等落到极片,减少污染源适当延长抽真空时间,减少气泡产生的机率实验方案一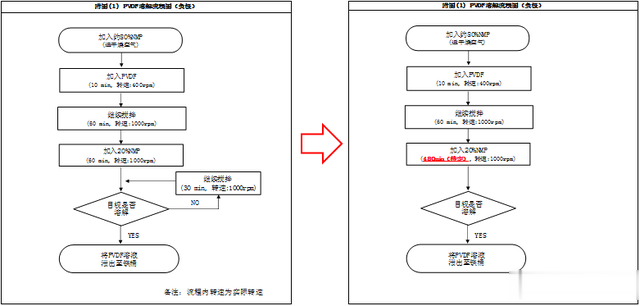
PVDF溶解主要膨胀和溶解两个过程;
在很短的时间内,PVDF只发生软化和膨胀,部分溶解;
适当延长时间和加温,有助于提高PDVF的溶解,减少搅拌过程中PVDF胶粒团聚。
实验方案二(负极)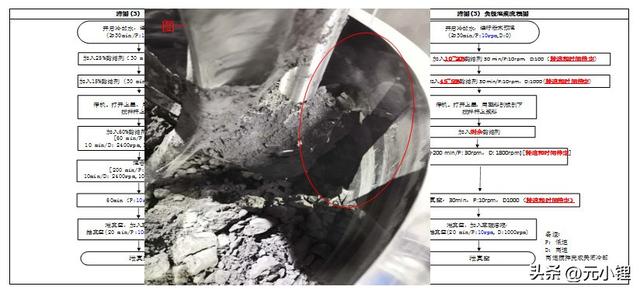
10~20%胶液主要起到一个润湿作用,具体用量实际观察待定;
45%~55%胶液起到捏合作用;
抽真空30min主要是去除浆料中的气泡;
图一为25%搅拌结束后浆料状况,分散轴和罐壁之间存在干粉料未参与搅拌(开分散轴转速)。
实验方案三(正极)
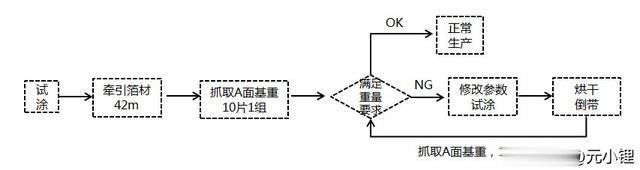
优化前

优化后
头尾部:极片左中右打洞取样示意图
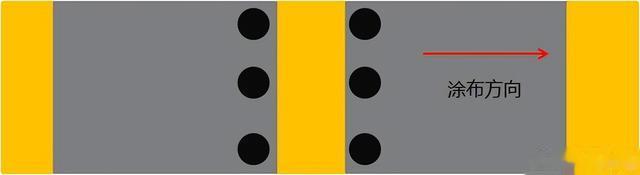
极片左中右打洞取样如上图所示;
修改前后首件流程的不同点:主要区别在于框一;
修改后每次首件可以节约牵引箔材42m;
修改后可以节约调机时间。
部分垫片、GAP不合适正极生产极板单面时,涂布速度8m/min,用1.2mm垫片,GAP150um 150um,腔体压力55。
措施:
使用1.0mm垫片,GAP控制在110~130um之间,腔体压力控制在80Kpa左右。
正负极头尾削薄规格不合适油性极板头部、尾部和中间厚度相差控制在10um之内;水性极板A面头部与中间厚度相差控制在10um之内;B面头部和中间相差控制在30um之内;A\B面尾部和中间控制在30um之内;头部和尾部削薄长度在6mm之内。措施:
头部削薄 0~5mm为参考区(0~2mm不测量);5~15mm为削薄区;尾部削薄 0~5mm为削薄区;涂布头部削薄 :正极(-10,5) 负极(-5,10);涂布尾部削薄:正极(-10,5) 负极(-5,10)。涂布机机头缓冲罐液位设置不合适目前二厂正负极涂布机机头缓冲罐液设置上限为80%,下限为30%;涂布前先打满机头缓冲罐(基本上液位在80%~90%),涂布过程中不再补充新的浆料,直至液位下降到30%报警;上述操作会导致在补充完新的浆料后,涂布重量产生突变。措施:
设置缓冲罐液位上限为80%,下限为60%;在涂布过程中,当液位低于60%,自动补充新料,当液位高于80%,停止补料,始终保持液位在60%~80%之间。正极冷压激光测厚仪放置不合理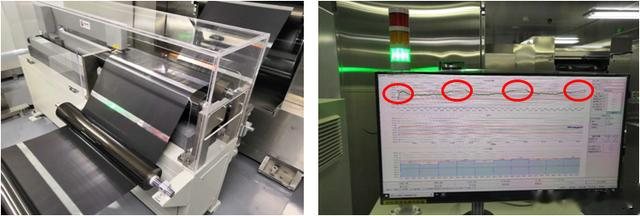
措施:
增加过辊,减缓极片抖动;在空间允许的情况下,设备适当后移。中长期计划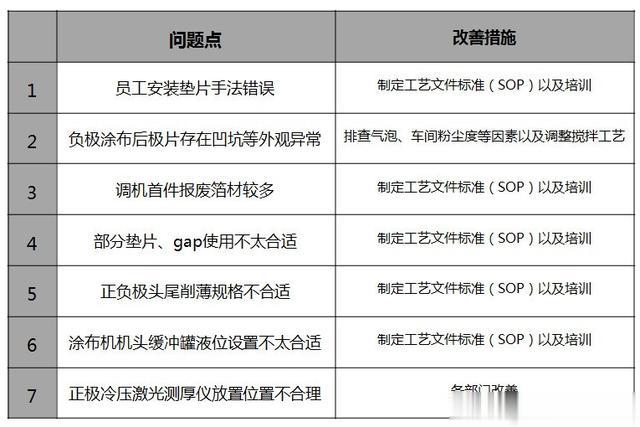