简介
在加工行业,设备的可靠性和有效可用性是具有高生产率和向消费者提供忠实服务的首要要求。必须确保设备的可靠性,各环节的重要性大概占比如下:
通过适当的设备选择约占60 %通过正确的安装约占15 %通过适当的运行和维护约占25 %
以下案例研究描述了现场液化石油气(LPG)输送泵的可靠性问题,以及故障排除和修复的方式。
历史
该泵于1999年3月安装并调试。机械密封每隔45~60秒开始间歇性泄漏。即使将RO(限制/调节孔板)尺寸从3 mm增加到5 mm,这个问题仍然存在。
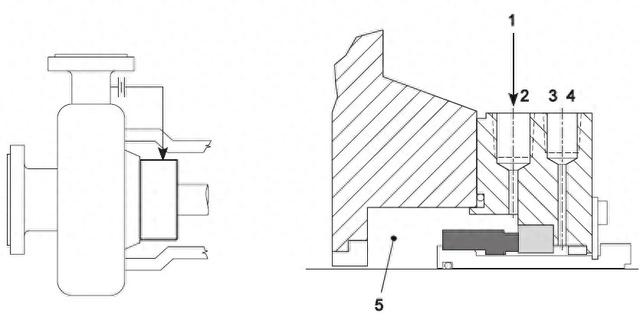
图例说明
1 来自于泵的高压区(泵出口或泵出口管线)2 冲洗口(F)3 急冷口(Q)4 排液口(D)5 密封腔
图1:标准密封冲洗Plan 11详图
Plan 11(包括孔板)提供密封冲洗;Plan 61提供备用急冷,不过最初没有提供冷却水。根据制造商的说明,密封腔内的估计压力约为泵出口压力的90 %,因此约为(0.9×16)14 kg/cm2(g)。
服务:LPG泵制造商:Khimline Pumps, Ltd额定流量:76 m3/h额定扬程:173 m入口压力: 设计=8 kg/cm2(g); 最小=7 kg/cm2(g); 最大=10.5 kg/cm2(g)运行温度:50 ℃汽化压力:6.8 kg/cm2(g) @ 50 ℃比重:0.56NPSHA:2.5 mNPSHR:1.9 m径向轴承:NU310推力轴承:7310(背靠背安装)
机械密封型式:带氟橡胶弹性体、单端面波纹管机械密封。密封平衡比为70 %,低比重液体的压力梯度系数为0.3。根据制造商说明,弹性体压力为0.45 kg/cm2。密封面材料:碳/SiC衬套上的轴向孔一开始没有(见后面的讨论)。冲洗方案:API Plan 11(3 mm孔板),并预留急冷接口(Plan 61)。然而,最初没有提供冷却水,而且接口F/D均用螺塞堵住。
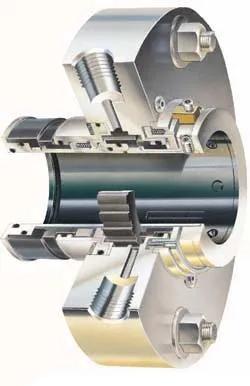
现场运行情况
机械密封出现间歇性泄漏。
入口压力:7.5 kg/cm2(g)出口压力:16 kg/cm2(g)(稳定)电机负载:55 A(稳定)振动:最大6.2 mm/s
间隙性密封泄漏可能的原因
1)动环组件处于悬吊状态2)密封面变形3)转子轴向浮动4)密封腔压力低于汽化压力,液体闪蒸成蒸汽
密封解体后
1)碳面观察到闪光痕迹,旋转面完好2)弹性体状况良好3)两只轴承均完好;未观察到转子轴向浮动迹象4)叶轮完好无损5)旋转单元的轴向运动不受限制,且没有粘性沉积物6)检查密封面的平面度,发现没有问题7)注意到泵叶轮配有后耐磨环,但是没有提供平衡孔
分析
a. 由于发现动环组件在轴套上处于自由状态,因此排除第#1项可能的原因b. 密封面平面度没有问题,因此排除第#2项c. 未观察到转子轴向浮动迹象,排除第#3项d. 在碳面观察到闪光痕迹表明,配合面上有润滑膜损失,这可能是由于密封腔中形成的蒸汽,而由于喉部衬套处的间隙过小,蒸汽无法从密封腔中顺利排出。这种蒸汽的积聚可能是由于配合面和封闭的密封腔产生的热量所致。由于密封面产生的热,密封腔喉部衬套间隙似乎不足以带走汽化热量,尤其是由于Plan 61最初没有提供冷却水。
随着密封面周期性地打开和LPG释放到大气中,密封间歇性失效不可避免。这可能是因为积累的蒸汽(从液态LPG到气体的相变)会逐渐增加填充密封腔的体积,然后,当压力充分积聚时,密封面将被打开,导致蒸汽释放。压力得到释放后,密封面将短期闭合,直至压力升高到某一值时,密封面将会被再次打开,如此循环往复。
解决方案
起初,考虑将密封冲洗方案由Plan 11改为Plan 13。对于LPG/丙烷应用,在工作温度下吸入压力和蒸汽压力之间的差距很小,Plan 13被认为可以将密封腔中过多的积聚蒸汽带回到泵的吸入口。该方案将包括从密封腔通过RO(流量调节孔板)到泵吸入口的冲洗管线。然而,这并不能解决密封腔内的汽化问题,因为密封腔压力会比使用Plan 11时更低,因此腔内压力和蒸汽压力之间的余量会更小。因此,Plan 13被否决。修改/改进的历史记录:
第1步由于LPG服务(密封腔压力和旋转密封面产生的热量非常接近汽化压力),因此必须带走密封面产生的热量,以避免密封区域快速形成蒸汽。最初,人们认为这是由于密封腔内的蒸发造成的,为此,扩大了孔板孔口尺寸以增加密封腔压力。但遗憾的是,这并没有解决问题。第2步API 610标准中的Plan61,为预留的(备用)冲洗方案,设备出厂前其接口采用螺塞堵住。现场可根据实际需要最终决定是否启用Plan61。最初没有启用,因为该位置没有可用的冷却水。与制造商讨论了这一点,指出LPG应用可能对密封腔中的热量比较敏感。然而,制造商认为泵可能不需要额外的冷却,因此没有对冷却水的可用性做出规定。由于问题仍然存在,为了解决此问题,通过将入口和出口管线连接到相邻机组的远程集管来提供通过密封夹套的冷却水循环,而无需拆卸泵。不幸的是,也没有解决问题。第3步在喉部衬套的上部钻了一只5 mm的孔。同时,由于拆卸和检查发现叶轮上缺少了4只平衡孔,因此在叶轮上增加了4只平衡孔。这一改造成功了,泵现在运行良好,没有任何泄漏。根据制造商对轻烃应用的经验,此类泵的密封腔压力(在使用后耐磨环+平衡孔后)≈吸入压力+35 %的出口压力,即:
8.0 kg/cm2 + 0.35 % x 16 kg/cm2 = 13.6 kg/cm2 (g)
有趣的是,这几乎等于改进前的密封腔压力(如上面的“90 %的规则”计算所使用的)。因此,理论上,这种改进不会显著地改变密封腔压力。然而,变化的是从出口连接到密封腔,然后通过开孔的喉部衬套的液体冲洗量。换句话说,限制因素是衬套间隙,而不是Plan11管道中的孔板。
总结
通过在喉部衬套上开孔并在叶轮上增加平衡孔,传递摩擦热的流体冲洗循环通道变得不那么受限,并在没有过多停机时间和成本的情况下解决了问题。经验表明:对于汽化压力和吸入压力之间的裕量较小的轻烃应用的泵,应在喉部衬套顶部开一只3 mm - 5 mm的孔,以便使蒸汽能从密封腔内顺利排出。
免责声明:本平台所发表内容及图片,标原创内容为本人原创。对所有原创、转载文章的陈述与观点均保持中立,原创、转载和分享的内容只以学习为目的,仅供参考,不代表本人的观点和立场。如有侵权和错误,请联系删除或修改,欢迎各位同行,共同交流学习!