【化工科技装备大发展】系列-801
这是一个记录石油化工装备发展历史和取得成就的有趣系列合集
欢迎大家分享点评讨论交流,为化工装备现代化鼓劲加油
回顾历史 分享成就 展望未来
------------------------------------------------------------------------------
2023年12月15日,采用中国石化国际首创的环己烯酯化加氢制环己酮新技术的20万吨/年生产装置,在巴陵石化己内酰胺产业链搬迁与升级转型发展项目一次开车成功,标志着全球首套环己烯酯化加氢制环己酮工业生产装置建成投产,为中国石化打造全球单套产能最大、技术领先的己内酰胺生产基地提供新动能,为我国己内酰胺产业链高质量发展提供坚实支撑。
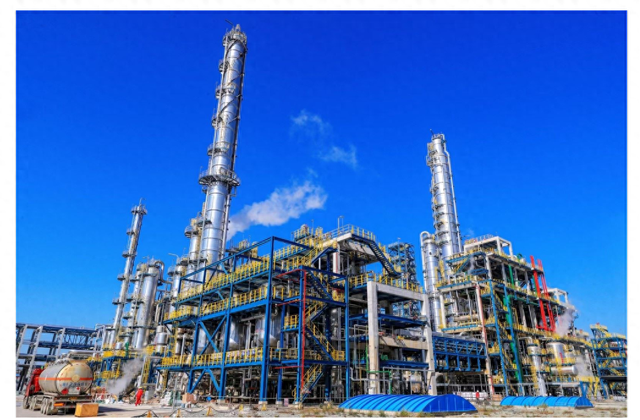
环己酮是重要基础有机化学品,主要用于合成尼龙-6、尼龙-66 及其它树脂,并作为性能优异的高档溶剂,在涂料、油墨、制药、农药、胶黏剂、感光材料等行业广泛应用。
早期,国内环己酮只是己内酰胺的中间产品,厂家的环己酮生产能力与己内酰胺装置相匹配,只有很少量的商品环己酮供应市场。环己酮作为一个独立的行业成长和发展起来,主要有两个原因:一是由于环己酮的溶剂用途不断扩大,特别是作为一种高档的有机溶剂,在涂料、油墨、胶粘剂等行业被广泛应用,形成了较大的商品市场;二是随着国内生产水平的提高,环己酮在化工合成领域发挥着重要的作用,除在化纤领域用于合成己内酰胺、己二酸外,还可以制备树脂、聚己内酯、医药中间体等多种化工产品。
目前,全球99%的己内酰胺由环己酮经肟化、重排生产,并广泛应用于纺织、电子、汽车、轨道交通、航天航空等新材料领域。己内酰胺产能的快速扩大,推动了环己酮需求的日益增长。2023年,我国环己酮消费量超过600万吨,超过全球消费量60%。
据了解,现有环己烷氧化制环己酮工业生产技术仍存在较大不足,环己烷氧化工艺的碳原子利用率不足80%、“三废“排放量大、本质安全性低。环己烯水合工艺虽然碳原子利用率可高达95%,但沸点相近的环己烷、环己烯、苯分离能耗高,且水合反应单程转化率仅约10%,开发原子经济性高、安全性好、能耗低的绿色生产新技术迫在眉睫。
工艺国产化历时13年形成具有自主知识产权的环己烯酯化加氢制环己酮新技术中石化石油化工科学研究院有限公司(以下简称石科院)是中国石化直属的综合性科学技术研究开发机构,创建于1956年,在国际上拥有较高的知名度和影响力。院本部位于北京市海淀区学院路,在昌平高新科技园区和天津南港工业园区设有研究机构和科学试验基地。科研领域包括:炼油、石油产品、化工、材料、新能源、环保、智能化、资源循环利用。
面对日益增长的产业需求和绿色低碳要求,中石化石科院在全球首次提出环己烯酯化加氢制环己酮原创新技术,开展技术攻关,将新反应途径、新催化材料、新反应工程进行集成创新,先后进行小试、中试和工业化装置建设,历时13年最终形成具有自主知识产权的环己烯酯化加氢制环己酮新技术,相关成果获中国发明专利授权40件、欧美等国家和地区发明专利授权3件,成为中国石化己内酰胺新一代绿色生产成套新技术中的核心技术。
石科院研究人员提出了一种环己酮制备新技术路线:苯选择性加氢生成环己烯,环己烯与乙酸酯化生成乙酸环己酯,乙酸环己酯再加氢生成环己醇,并联产乙醇,最后环己醇脱氢制备环己酮,反应方程式如下:
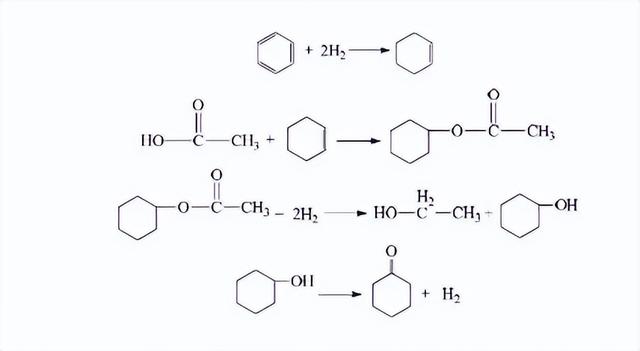
该技术路线的优势在于:
①新工艺不仅少消耗1/3 的氢气,副产物环己烷可再利用,且避开了环己烷氧化的过程,苯的利用率达到99%以上,是一条绿色高效的生产路线;
②酯化和加氢反应均具有很高的选择性,原子经济性高;
③联产乙醇,增加了过程的经济性。
2003年,石科院携手巴陵石化等单位开发的单釜於浆床环己酮氨肟化制环己酮肟技术实现首次工业应用。与传统的羟胺肟化工艺相比,该技术氮原子利用率从不足60%提升至90%以上,废气排放量下降99%,能耗降低40%,装置投资减少70%,经济和社会效益显著,达国际领先水平,推动了我国从完全依赖引进技术一跃成为拥有自主知识产权技术的世界己内酰胺第一生产大国,自给率从不足15%提升至98%,全球市场份额超过60%。
近年来,石科院锚定“双碳”目标,在多年氨肟化技术开发和应用的基础上进行二次创新:一方面,开发了高效减排的环己酮氨肟化升级技术,装置蒸汽消耗下降42%,废水排放量降低15%,环己酮、过氧化氢利用率进一步提高,装置技术经济水平再次大幅提升;另一方面,攻克了装置大型化的难题,将单套装置规模由10万吨/年提高到30万吨/年,单套装置产能达到世界领先。
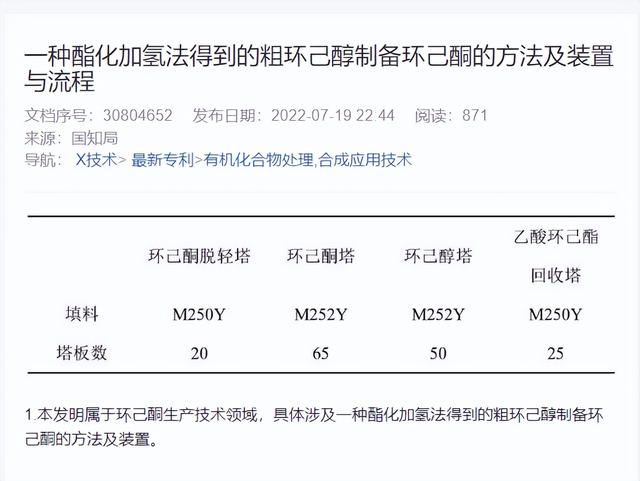
湖南石化年产60万吨己内酰胺产业链搬迁与升级转型项目新建酯化法环己酮装置,是该项目的核心装置之一,共有两条生产线,年产能均为20万吨,包含6个生产单元。
20万吨/年环己烯酯化加氢制环己酮成套技术是中国石化十条龙科技攻关项目,采用中国石化首创研发环己酮绿色生产新技术建设,碳收率高,三废排放少,清洁高效,是巴陵石化年产60万吨己内酰胺产业链搬迁与升级转型发展项目的重要技术支撑。该项新工艺是由中石化牵头,石科院与巴陵石化公司合作开发,首次工程化项目落地。
2023年7月5日,巴陵石化年产60万吨己内酰胺产业链搬迁与升级转型发展项目酯化法环己酮装置顺利中交,进入生产准备阶段。

2023年12月15日,中国石化具有自主知识产权、全球首套采用环己烯酯化加氢制环己酮装置A线一次开车成功。两个月来,湖南石化新区己内酰胺部和中石化石科院等单位加强协作,持续优化新装置生产运行,在稳定提高负荷上下功夫。
2024年2月15日,环己烯酯化加氢制环己酮成套新技术的工业化装置,在湖南石化建成投产两个月,运行平稳,产出合格环己醇、环己酮、环己烷、粗乙醇等,累计生产环己酮近2.6万吨,目前日产环己酮400吨左右。
关键设备的国产化助力全球首套环己烯酯化加氢制环己酮装置兰石重装为该项目研制了酯加氢反应器、环己酮脱氢反应器和脱轻塔等16台核心装备。其中,酯加氢反应器采用中国石化首创环己酮新技术,为中国石化重大装备国产化攻关项目。兰石重装研发销售中心扎实做好前期技术准备,加强统筹调度,紧扣时间节点,精心组织生产,圆满完成产品研制并按期交付,为巴陵石化项目酯化法环己酮装置中交提供了有力保障。
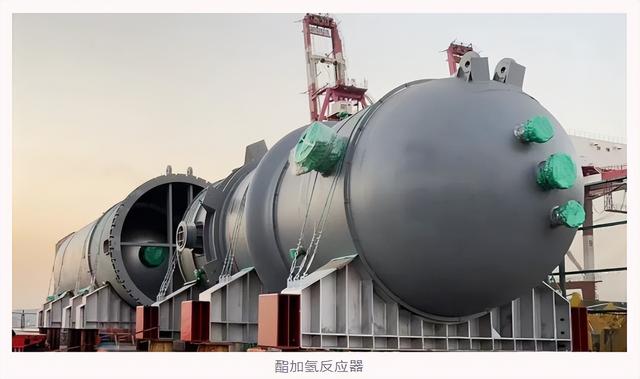
环己酮脱氢反应器由管程和壳程组成,产品规格Φ4500×20×10325(mm),筒体壁薄且直径大,每台产品内含4683根换热管,产品制造难度大。
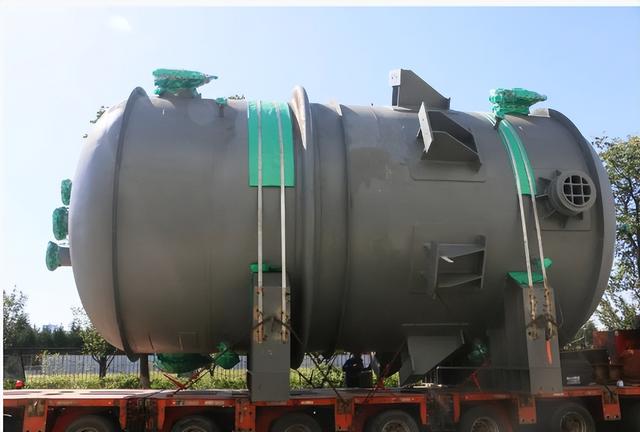
环己酮脱氢反应器
巴陵石化选择中圣科技承接设计及制造酯化法环己酮苯选择加氢反应器等核心设备。此项目承制的加氢反应器,从设计到制造历时15个月,中圣科技将坚持研发创新发展理念,高度配合中石化进行国产化项目的开发,共同推动中国重大技术装备国产化进程。
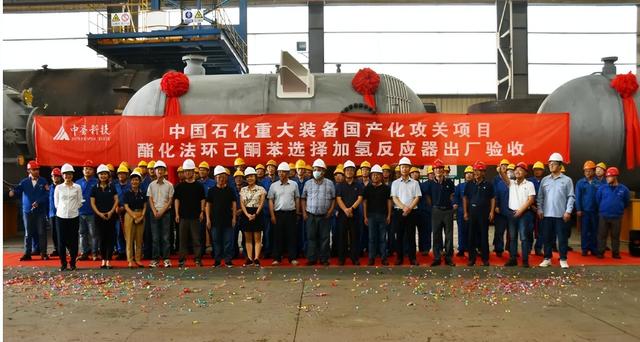
2022年8月26日,中石化重大装备国产化攻关项目——巴陵石化己内酰胺装置加氢反应器通过中石化物装总部、中石化特聘专家组、设计院、业主方的联合验收工作!
酯化法环己酮装置大件设备共计30台,计划分4个批次进行吊装,2023年1月全部吊装完成。
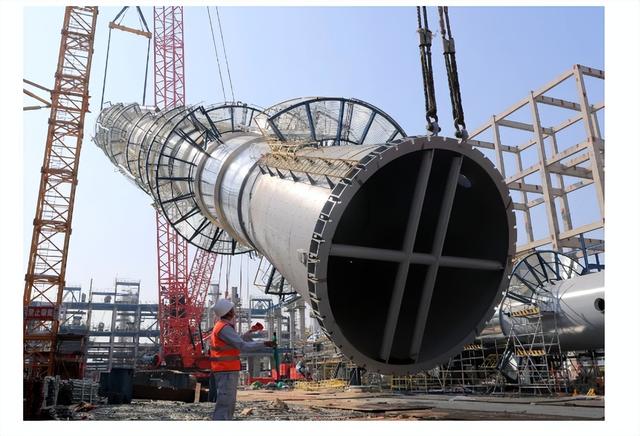
2022年11月6日和7日,巴陵石化己内酰胺产业链搬迁与升级转型发展项目己内酰胺分部酯化法环己酮装置B线现场,抽提精馏塔和溶剂回收塔分别吊装就位。
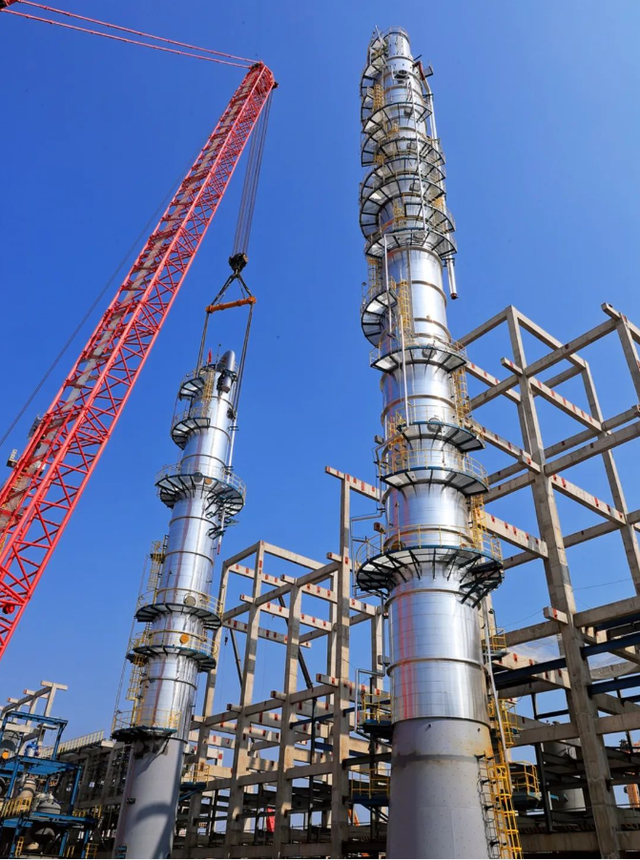
2023年1月2日,巴陵石化己内酰胺搬迁升级项目临时大件码头,随着4台酯化加氢反应器陆续安全起吊卸船。
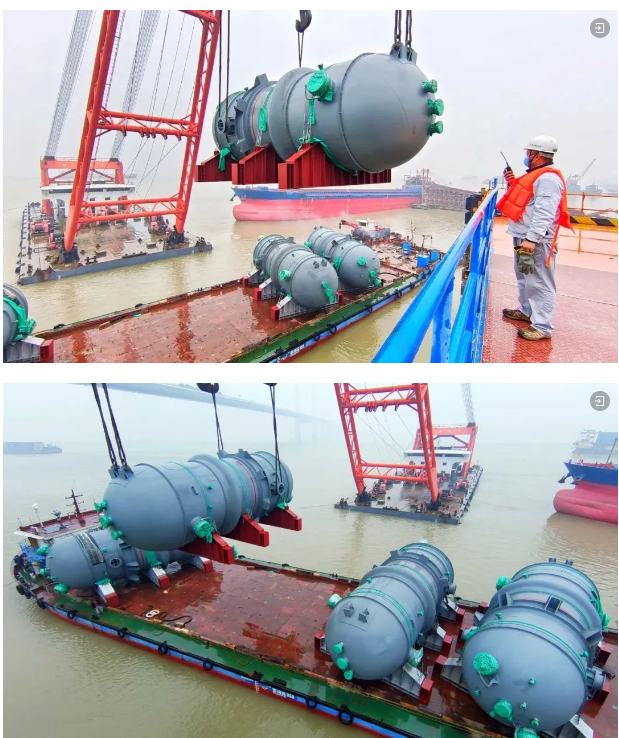
2023年2月25日,巴陵石化己内酰胺搬迁升级项目己内酰胺分部酯化法环己酮装置B线大件设备脱酯塔顺利吊装就位。该设备直径3.8米、长51米、重150吨。

2024年2月23日,中国石化集团公司在2024年科技进步工作会上表彰一批科技创新先进,湖南石化“浆态床双氧水/酯化环己酮成套技术开发创新团队”获评中国石化优秀科技创新团队。
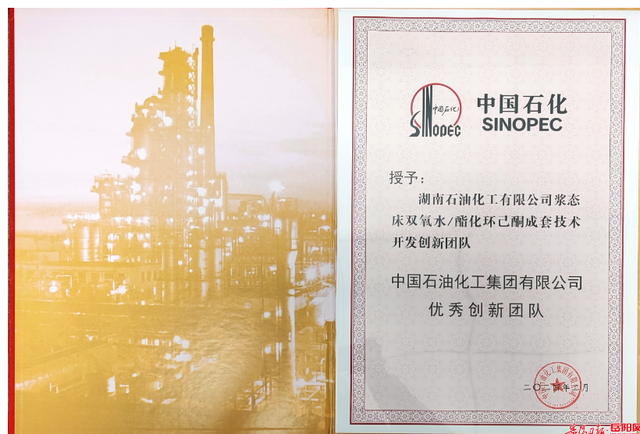
**********************
赞盛世中华繁荣富强
向装备制造工作者致敬,
为化工行业建设者加油
**********************
本系列和大家分享最近十年来化工装备行业取得的成就
图文来源网络资讯收集整理,对资讯发布者表示感谢,如有侵权秒删
感兴趣的朋友可以看系列合集,欢迎讨论