大力发展催化剂、添加剂生产
在研究如何加快炼油工业发展的问题时,我同炼油科研、设计、技术人员多次进行座谈和个别交谈,请他们介绍炼油技术、工艺流程,讲解有关炼油的一些技术问题。从他们的介绍中,我了解到,生产高级一点的石油产品,都离不开催化剂和添加剂。在原油加工的反应过程中使用效率高的催化剂或在半成品中加入相应的添加剂,就能生产出相应的高质量石油产品。催化剂、添加剂是发展炼油工艺技术的关键因素和重要条件,合理使用“两剂"是增加石油产品品种、提高油品收率、改善油品性能、提高油品质量的重要手段。
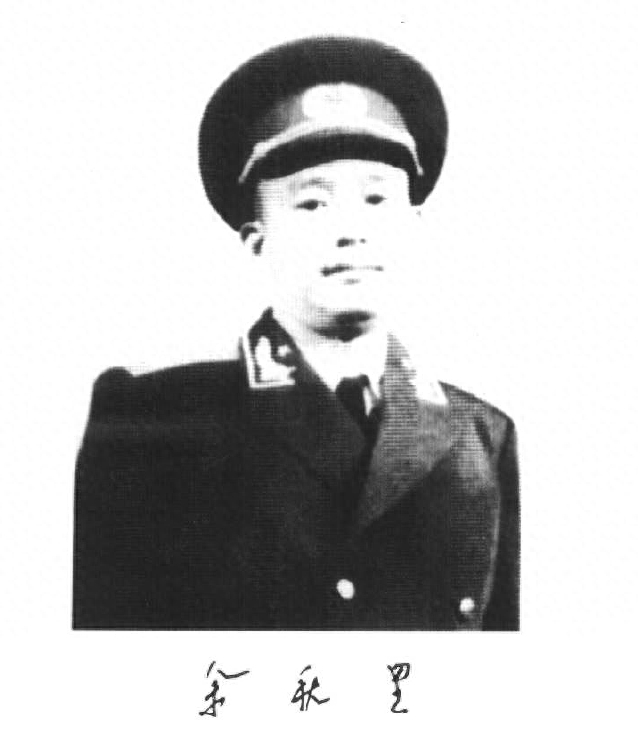
50年代,我国已开始试制、生产提炼人造油以及炼油加工中使用的催化剂.但是品种很少,数量很小;生产高级一点油品使用的“两剂”都靠进口。60年代开始,在加快发展炼油工业、实现石油产品自给的过程中,在研究新品种、发展新工艺、建设新装置的同时,必须解决"两剂”的研制和生产的问题。否则,新装置建设起来了,也不能发挥应有的作用。新工艺研究出来了,也生产不出新油品。因此,我们一直重视“两剂”的研制和生产问题。1960年12月召开的石油炼制科研计划会议上。讲到发展石油新品种时,我提出要抓“两剂一尖”或者“两剂一新”(即催化剂、添加剂和尖端产品、新技术新工艺).“两剂”和油品同等重要,都要抓紧。
1962年1。月20日,在党组会讨论炼油工作时,我提出,为了加强“两剂"研究,要成立研究所.建设“两剂”工厂。以后又多次强调要支持研究部门和炼油厂搞添加剂.尽量多产添加剂,增加石油产品品种。
生产航空汽油。需要使用硅铝小球裂化催化剂,它是开发催化裂化工艺、提高航空汽油收率和质量的关键物质。50年代末60年代初,我国唯一的兰炼移动床催化裂化装置使用的催化剂全部是从苏联进口的。1960年开始,苏联逐步减少以至最后停止了对我国的催化剂供应,直接威胁到我国航空汽油的生产,形势十分严峻。据兰州炼油厂的同志反映,1963年初.他们库存的催化剂最多能维持生产1年。兰炼领导和工人们都忧心忡忡,担心没有供应来源。大家都想方设法节省使用,井回收利用旧催化剂,以保证航空汽油的正常生产。他们急切盼望生产出自己的催化剂来.
为了赢得时间,保证炼油生产,我国硅铝小球催化剂的研究和生产装置的设计,几乎是同时起步的。这是打破常规甚至带有风险的。1962年,我们决定。生产装置建在兰炼,由兰炼总工程师龙显烈同志主持,兰炼和北京、抚顺设计院抽调人员,联合进行设计。
催化剂由石油科学研究院负责研制。当时我们对这种催化剂和工艺了解很少,没有这方面的经验。我把研制催化剂的重担,交给了石油科学研究院从美国回来不久的阂恩泽同志。阂恩泽是化学工程专家,没有直接从事过催化剂研究。他接受了这个艰巨任务后,在研究院组织了一批工程师,在实验室进行研究,并参加工艺流程、设备选型等设计工作。1963年初.研究工作有了结果后,就带着一个小组,一头扎到了兰炼,进行放大试生产。他们吃在车间,睡在办公室,和工人一起爬装置,钻高温干燥箱,一心埋头搞研究、搞攻关。
为了推动催化剂试制工作,李人俊副部长带病去兰炼,听取兰炼领导和阂恩泽同志汇报,研究解决试制中有关问题。由于劳累过度病倒了,住进兰州陆军总医院。住院期间。还放不下心,经常把阂恩泽同志找去了解情况,研究工作。经过3个月的工业试生产,拿出了合格的催化剂。
在兰炼建设的我国第一套催化剂生产装置的设计施工也在同时加紧进行。兰州炼油厂安装公司的领导和职工们同心协力,披星戴月,奋战在施工现场,许多同志带病坚持工作。1964年4月,高质量高速度地建成了我国第一套催化剂生产装置。同年6月,试生产成功。
设计年生产能力为1000吨,后来扩大到1800吨。终干在进口催化剂即将用尽之时,生产出了质量完全合格的催化剂,保证了我国航空汽油的正常生产。
在石油二厂建设的流化催化裂化装置,需要使用一种硅铝微球裂化催化剂。这种催化剂的制造技术为美国所垄断,英、荷等国也是引进或合资生产。技术买不到,买产品要价很高。我们决定,除买一些供我国第一套流化催化裂化装置开工试运的应急之用外,要在兰炼建一套硅铝微球催化剂生产装置。这个装置的设计、建设和微球催化剂的WYE工作,是在小球催化剂研究和生产装置设计完成之后进行的。研制工作仍由石油科学研究院负责。由于二厂建设的流化催化裂化装置计划在1964年底建成,时间很紧迫。对此,我很关切。
1963年春节前,部党组在部机关设宴招待工程技术专家,我与阂恩泽、陆婉珍夫妇同桌,当时流化催化裂化的科研、设计工作已作了安排.关键要看所需的微球催化剂何时能够搞出来。席间,我问闵恩泽:“微球催化剂哪一天能搞出来?”他回答说:“还要详细安排一下。”过了几天,陈毅副总理在人民大会堂举行春节招待会会上,我又见到闵恩泽同志,他才对我说:“马上开始实验室研究,一年后开始设计。现在就与抚顺设计院、兰州炼油厂一起调研,制订方案。”我立即要求设计院、兰州炼油厂等单位,组织有关人员同阂恩泽合作,大力支持他的工作。阂恩泽等同志对比分析国外有关资料。又到上海、天津等地调查,从我国的实际情况出发,选择了研制速度比较快、操作比较简单、设备制造不太复杂、适合我国当时技术水平的工艺,把实验室研究配方和工艺条件,同在中型装置上解决喷雾干燥成型问题结合起来,缩短了研制周期。喷雾用的高压泵是上海大隆机器厂研究制造的。通过部内外科研、设计、施工、生产部门的大协作和交叉作业,解决了一系列技术难题。1965年12月我国第一套工000吨/年微球硅铝裂化催化剂工厂投入了试生产。
1966年1月,我国自己的微球催化剂厂正式生产出合格产品,从此,就不再进口了。
在石油产品特别是润滑油生产中,添加剂起着非常重要的作用。
在润滑油基础油中加入各种相应的添加剂.可以改善润滑油的性能和提高它的质量,如增彩降凝,抑制油品氧化,避免泡沫产生,保护机具减轻磨损、氧化、腐蚀、锈蚀等,生产出适合各种用途和要求的润滑油。从某种意义上讲,添加剂具有“神奇”的力量,可以起到‘点石成金”的作用。我国航空煤油、航空润滑油和其他许多高级油品,都是由于研制、使用了相应的添加剂,才过了技术关,批量生产出合格产品的。
为了适应增产润滑油,增加品种、提高质量的需要,60年代初,石油科学研究部门和炼油厂加快了添加剂的研究试制和工业生产的步伐。1963年以后,在石油科学研究院、中国科学院有关院所和化工部有关部门的配合、支持下,兰州炼油厂、石油六厂、七厂、上海炼油厂以及玉门、独山子等炼厂,先后建立了添加剂车间和添加剂研究组织,使各种添加剂的研究、试制有了突破性进展。在实验室研究、小型中型装置试验取得成功的基础上,建设了一批添加剂T命牛产装置。到1965年,以兰炼、六厂、七厂、上炼为主要基地,全国添加剂生产能力超过1万吨,当年产量达到2500吨,填补了我国添加剂领域的许多空白,为石油产品从品种到质量立足于国内创造了必要的条件。
加强炼油厂的经营管理
炼油厂的管理,是一个重要的问题。我经过调查研究发现,在一些炼厂发生的许多问题,诸如设备跑、冒、滴、漏,生产不正常,油品不合格,以及发生火灾等等,往往不是因为设备不好,不是因为技术水平低,也不是因为缺少必要的条件,而是管理不严、责任心差所致。在60年代初期,为管好企业,搞好生产,我们着重抓了以下几个方面的工作,收到很好的效果。
一是抓质量。石油产品与国防建设和工农业生产、交通运输以及人民生活都有密切关系,涉及千家万户,一旦产品质量出了问题.将影响国民经济的全局,影响人民生命财产的安全。而部队用油则关系到后勤保障是否有效,甚至影响战争胜败。所以.油品质量是万万不可大意的。一定要树立质量第一的思想。我曾提出:工厂产品质量出了问题,总工程师要负责,厂长、党委书记更要负责;要加强质量检验,保证生产的油品合乎质量标准,有一点儿不合格也不许出厂,用户要也不给;用户反映产品不合格,厂长、书记耍亲自去“背”回来。有一次,大连石油七厂发出去的柴油不合格,我们听到用户反映后,硬是要厂长到用户那里,赔礼道歉,把油运了回来。我们把这件事通报各炼油厂,要求大家严把质量关,严格执行质量检查制。各厂普遍建立和执行了“五不许出厂”制度:产品质量不符合标准不许出厂;分析项目不全不许出厂;没有质量合格证不许出厂;包装容器不符合标准不许出厂;军用油品总工程师不签字不许出厂。我们还明确规定,总工程师要把好质量关。这些办法是很灵的。从此,各炼油厂出厂的石油产品,连续多年合格率都保持或接近百分之百。
二是抓设备整顿。初步掌握大庆原油的加工技术之后,我们党组研究,要进一步搞好设备管理,做到安全平稳操作。针对东北许多炼油厂旧设备多,长期失修,跑冒滴漏严喧霎,威胁安全生产的情况,决定选择石油一厂作为整顿设备的试点。1962年4月,我们指派生产技术司司长孙晓风同志为组长,抽调各炼油厂主管设备的副厂长、设备科长、车间主任、工程师等,连同石油部机关有关专业人员,到石油一厂开展设备整顿工作。工作组一到厂,就以大庆油田“三老四严”的精神,认真抓设备整顿。他们深人现场和工厂职工一起,一台一台设备检查,发现泄漏点,一个一个整改。在此基础上,制定了各类设备完好验收标准和定人、定设备、定维修保养内容、定检修时间的“四定”措施。经过整顿,石油一厂的设备状况明显改善,主要设备完好率由年初的73.2%提高到81.2%,安全生产和厂容厂貌发生了很大变化。我看到工作组寄回来的报告时,十分高兴,立即把它转发全国各石油厂矿。1962年下半年,又从各炼厂抽调有经验的设备管理千部、技术人员和老工人,组成设备检查团,用两个多月时间,对全国7个主要炼厂进行了设备大检查。各炼油厂都发动职工群众进行了设备检查、检修和维护工作,使许多年久失修的设备比较彻底地改变了面貌。
在此基础上.各炼厂普遍加强设各管理,建立或健全了有关规章制度。从此,形成了每年进行一次设备大检查的制度。设备是生产的基本手段和物质技术基础的思想,在炼油企业领导人和广大职工中深深扎根.大庆油田的严细作风也在炼油企业国逐步形成。以后,我们又把炼油企业搞好设备整顿的经验,推广到汕田,油田的设备也进行了整顿,使严细作风更加巩固。
三是抓文明生产。我从国外的一些资料和专家的汇报中,了解到国外炼油企业推行“文明生产”的情况,对此很感兴趣。我积极提倡和推行“文明生产”的做法,提出要“刻样板、树标兵”。把企业管理推向一个新水平。在推行“文明生产”中,兰州炼油厂决心改变过去的形象,着手进行工厂园林化、规格化的建设。徐今强同志提出:“要把工厂建得像杭州西湖的苏堤一样,一株杨柳一株桃。”职工利用业余时间刨坑种树,绿化美化工厂环境。几年后,厂内环境大大改善,到处绿树成荫,花果飘香。昔日的黄土沙地,变成了“花园工厂”。兰炼还加强了设备管理。常减压装置二泵房,由几个女青年管理,他们把机泵擦得明光v亮,一尘不染。我去看时,戴着白手套都抹不出灰尘。
四是抓勤俭办企业。我国是一个大国,也是一个经济基础比较薄弱的国家。我多次提出,我们在走自己炼油工业发展的道路中,必须贯彻毛主席历来倡导的‘.勤俭建国、勤俭办企业、勤俭办一切事业”的方针,要坚决反对‘.大少爷、败家子”的作风,不仅要向国家、向社会提供更多的油品,还要不断降低成本,节省一切不必要的开支,为国家多创造财富。从60年代初开始,我们提出,在厂、车间、班组三级开展经济核算和经济活动分析,对形成勤俭办企业的良好风气,起了重要作用。
1962年,兰州炼油厂由原来炼制玉门原油改炼大庆原油,运费比过去高出一半,仅此一项,生产成本就要比上一年增加5000万元一个连续几年盈利的企业将发生计划亏损2600万元。面对这种情况,兰炼职工没有向国家要求降低原油价格,也未要求提高商品油价格。他们反复调查、反复比较,制订了合理利用资源,增加品种,提高质量,降低消耗,紧缩开支的实施方案。经过全厂上下一致努力年底决算时,不但没有亏损,还向国家上缴利润475万元。因此,在1963年7月.兰州炼汕厂被国家经委命名为全国勤俭办企业的“五面红旗”之一,周恩来总理、薄一波副总理还亲切接见了兰州炼汕厂的代表。
1964年上半年,李人俊副部长带领工作组,到兰州炼油厂进行贯彻《工业七十条》的试点工作。他们同该厂领导一起,把建立健全生产工作责任制作为重点。通过座谈调查、跟班写实。对全厂各车间、各岗位以及各职能科室、各级干部的岗位责任制进行全面检查和补充修订,同时修订了炼油工艺卡片;大力提倡文明生产、文明检修、文明维护保养,开展事故预想与排除事故演习,以及平稳操作、技术练兵等项活动,做到在没有照明的情况下坚守岗位,不会发生误操作;在连续生产作业的班组岗位,建立并实行了严格的交接班制度,进一步提高了经营管理水平。兰炼整顿和加强管理的经验,经石油部推广后,带动了全国炼油厂企业管理工作的加强和管理水平的提高。多年来,兰炼一直是全国炼油厂和全国“工业学大庆”的一面旗帜,起了良好的典型示范作用。