复合集流体的中间层所采用的乃是高分子薄膜,这一特殊的绝缘层具有独特的性质,使得两侧的金属镀层之间无法实现导通。在焊接过程中,若运用传统的超声波点焊方式,无论是将多层复合集流体的极耳直接进行焊接,还是把多层叠在一起的复合集流体极耳与金属极耳予以焊接,都会遭遇重重困难,最终均无法焊接成功。其原因在于,这种传统焊接方式容易出现虚焊的情况,即焊接点未能完全融合,导致接触不良;或者出现过焊的现象,致使焊接部位过度受热,材料性能受损。并且,焊接强度也远远无法达到预期的目标值。
而激光焊接这一方式,虽然在某些领域具有一定的优势,但其产生的温度过高,会给复合集流体带来严重的问题。过高的温度会致使基材发生显著的热变形,从而影响复合集流体的性能和结构完整性。
就目前行业的实际情况而言,所采用的较为有效的方法是使用两层纯金属箔材夹住一层复合集流体的极耳部分进行焊接。通过这种方式,能够在一定程度上确保焊接的稳定性和可靠性。之后,再将单层或多层纯金属极耳分别与锂电池的正极极耳或负极极耳精准地焊接在一起。这种分步焊接的策略,经过了实践的检验和不断的优化,在提高焊接质量和效果方面发挥了重要作用。
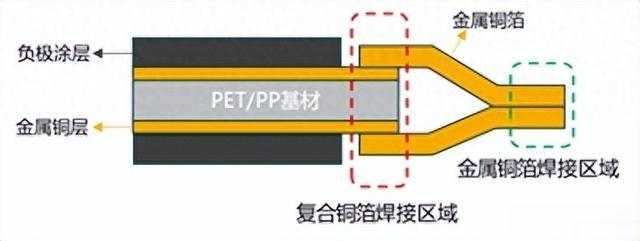
单层复合铜箔极耳焊接方式示意图
超声波滚焊超声波焊接原理,超声波发生器将工频电流改变为超声波频率的振荡电流,换能器依靠“压电效应”,把大功率振荡电信号能转化成相应频率的机械能,由变幅器放大振幅,利用高频振动波将能量传递到焊接物体表面,在高频振动和静压力的共同作用下,破坏工件界面的氧化层、表面油污,焊接工件间的外层电子结构的金属原子相互接触,发生原子再结晶、再扩散、再相变结合。
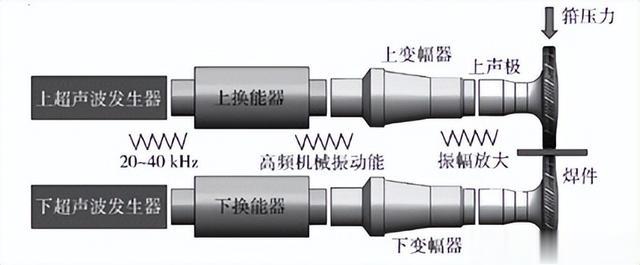
超声波滚焊工作原理
焊接功率和焊接能量直接决定焊接效果,焊接材料所需的焊接功率取决于焊材的厚度和硬度,材料越厚、硬度越大,所需的焊接功率就越高。超声波焊接的主要参数有:振幅、频率、静压力、时间、焊头设计参数等。
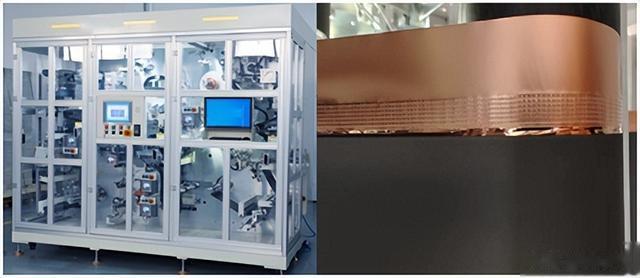
超声波滚焊机和焊接实物
在超声波滚焊方面,公司首创超声波滚焊方案,技术领先独供宁德时代。公司为国内外第一 个将超声波滚焊设备应用于动力电池焊接并成功产业化的企业,目前产品已应用于宁德时代新型 电池生产线。基于自主研发的高精度声学主轴系统设计技术、可旋转换能器设计技术及高速数据 采集技术,20kHz滚焊主轴系统能够稳定承受3500N 压力,40kHz滚焊主轴系统能够稳定承受 2500N的压力(国外同行最高500N),焊接速度可达80m/min(国外同行最高达到60m/min)。
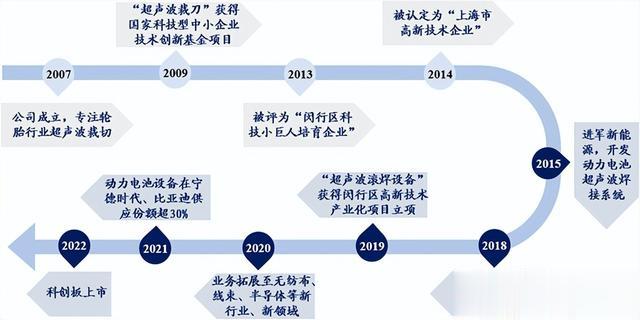
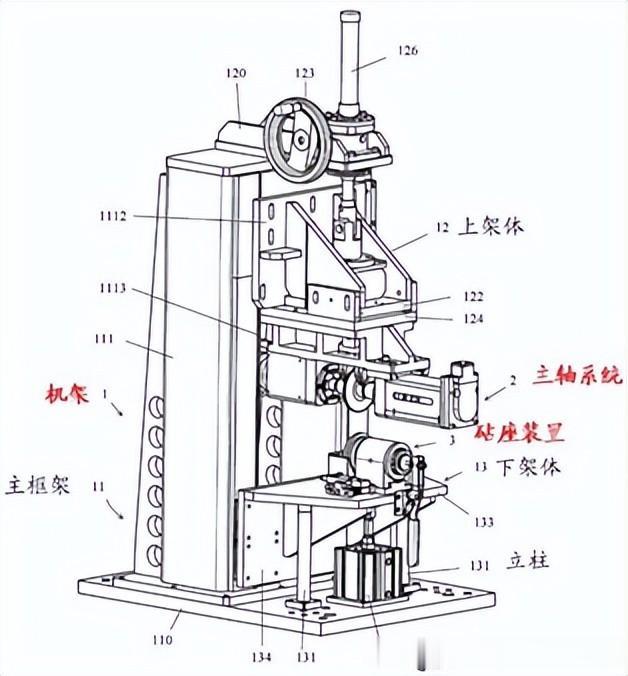
超声波滚焊机立体图
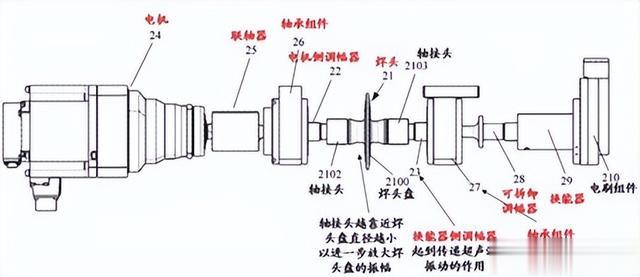
超声波滚焊机核心—主轴系统示意图
广州新栋力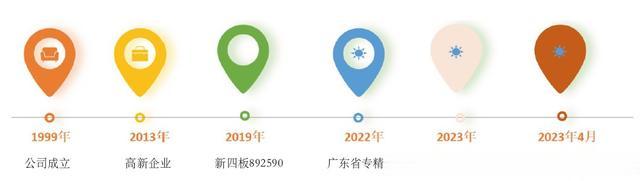
非标定制生产线
频率(KHz):2 0 - 4 0
输入电功率(W):1 0 0 0 - 5 0 0 0
重量(kg):3 0 0 - 5 0 0
适用工艺:多工位自动焊接线、线束焊接线、直线式焊接线、转盘式焊接线、非标定制。
非标定制生产线
频率(KHz):15 - 2 0
输入电功率(W):6 0 0 0 - 10 0 0 0
重量(kg):3 0 0 - 5 0 0
适用工艺:多工位自动焊接线、线束焊接线、直线式焊接线、转盘式焊接线、非标定制。
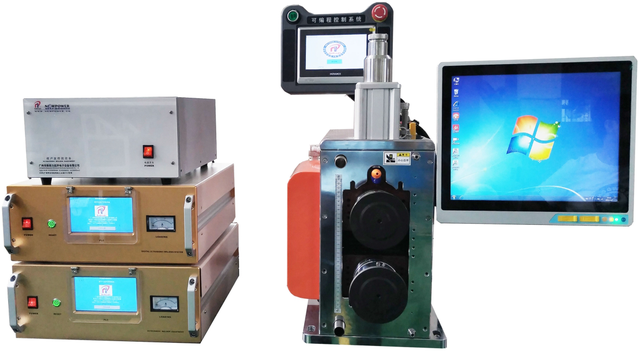
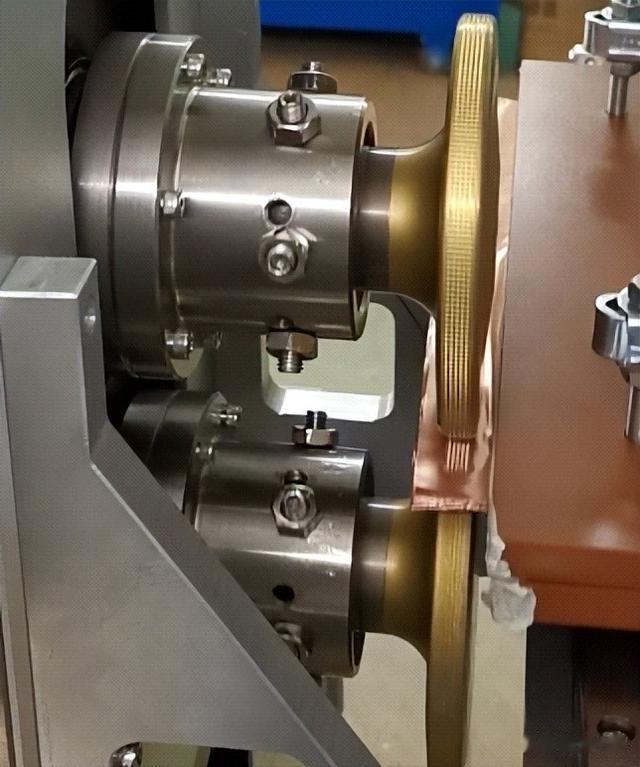
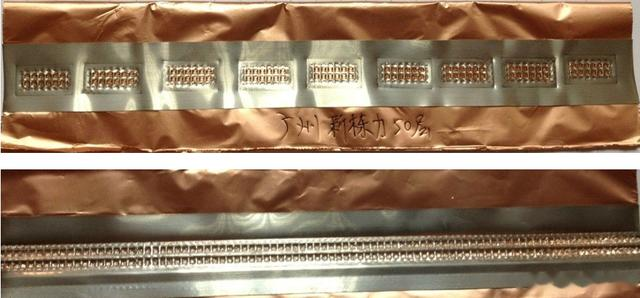
长极耳电池主焊传统点焊(A)与滚焊(B)对比图
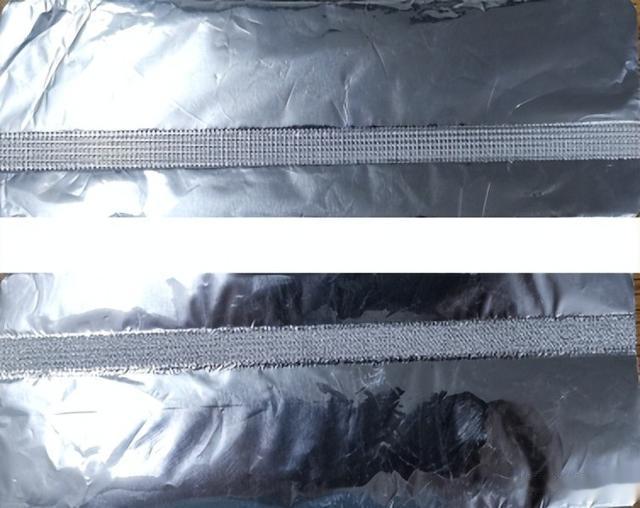
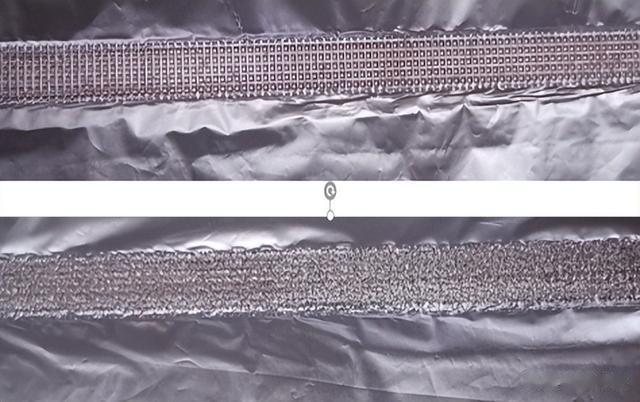
2 0 - 2 0 0层铝箔、铜箔平齿滚焊应用图片
苏州达牛达牛科技全自动智能滚焊装备 CWR2 CWR2 2-7,材料的涂布边和两种箔外缘位置进行检测,并通过纠偏机构对三种材料进行纠偏,可实现三种材料的对齐度为 ±0. 3mm 。在此基础上进行全自动焊接,方式为滚焊满足焊印距涂布边尺寸及公差为 1.3 ±0. 3mm 的工艺要求。在此基础上,通过整形装置对焊印平度进行修整,实现焊印平度保持在 0. 1mm 以内。
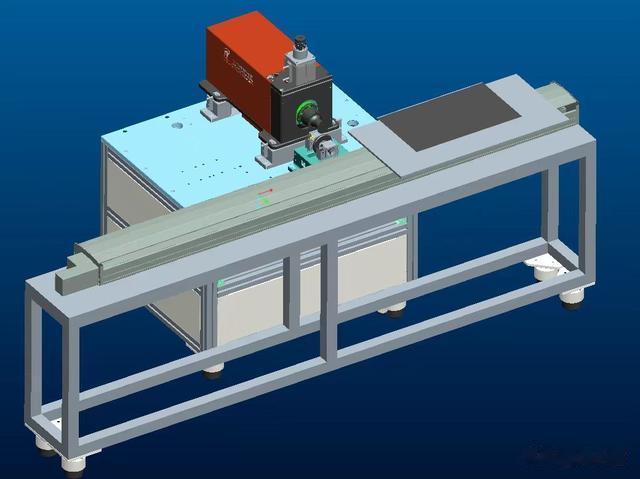
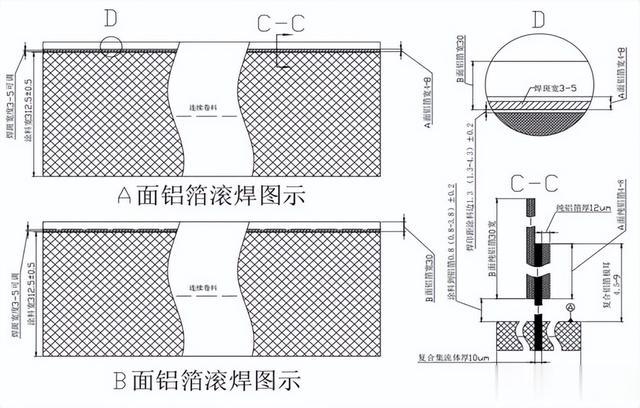
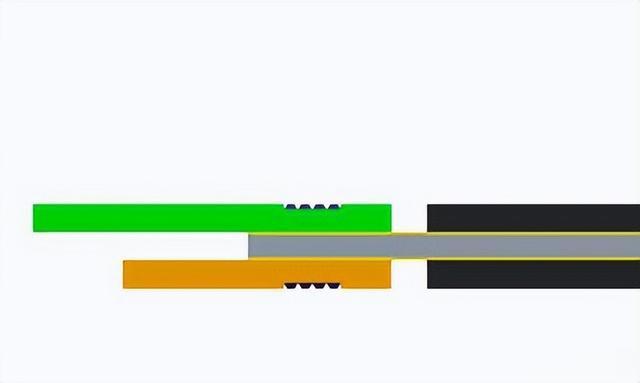
卷材和箔焊接 方式
美国必能信、Sonics基本能达到60m/min。现阶段通过调控焊接工艺参数,复合铜箔在滚焊后均能达到表1中指标,基本满足电芯端需求。
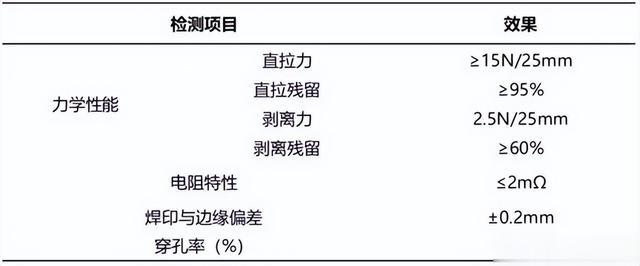
复合铜箔在超声波滚焊后的焊接性能指标
目前超声波滚焊存在一些问题,结合材料,实际焊接出现的情况做几点分析。
a.首先是复合铜箔与复合铝箔焊接差异性:现阶段复合铝箔滚焊效果较复合铜箔好,表现在焊接强度大,且透光率低;滚焊焊接强度如果较小,可能会影响后序的超声波点焊,因此复合铜箔在电池制程后段搭配激光焊接也许更加适合;
b.针对复合铜箔的超声波滚焊,比较了不同基材的差异,PET基膜的复合铜箔焊接效果最好,PP和PI相对不好焊接,强度低。由于基材结构性能差异,需要根据基材设计不同的焊头,并调整工艺参数。图所示,(a)是从PET复合集流体滚焊后剥离的纯铜箔,可以发现焊印处的铜箔几乎留在原处,并没有剥下来,而(b)PP基材复合集流体在滚焊后纯铜箔基本剥离下来,留在焊印处较少;
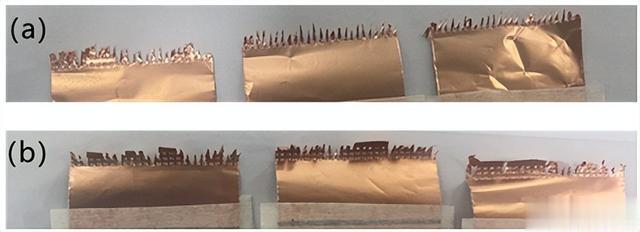
从滚焊处剥离下来的纯铜箔:(a)PET复合集流体;(b)PP复合集流体
c.复合铜箔焊接选用的纯铜箔厚度也会影响到焊接质量。目前超薄铜箔4.5um可能不太适用于复合集流体超声波滚焊,效果较差,主流还是使用6um的纯铜箔,焊接质量能够保证,当然如果使用更厚的箔材焊接效果可能会有所提升,但也会带来明显成本增加和极耳厚度增加,这需根据实际情况进行选择;
d.以电芯厂角度看,不希望PET基材复合铜箔存在较多穿孔现象。这样会使得基材暴露于电解液中发生一系列反应,加速电池性能衰减,但从滚焊焊接原理看,只有将基材穿破,实现上下层金属箔连接才能保证足够的焊接强度,因此需要进行工艺优化,以及在焊接强度与穿孔率之间找到平衡点。评价穿孔率可以通过透光实验或者采用白板笔在焊印处划的方式比较,从图5中还是可以明显看到滚焊后的PET基材复合铜箔存在部分穿孔。
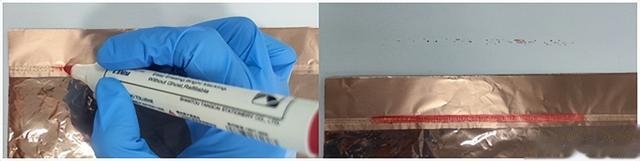
穿孔测试(白板笔在焊印处划)
压熔焊为解决多层极耳焊接痛点,卡洛维德(常州)智能焊接装备有限公司,研发出可替代超声波焊接+激光焊接的“第三种焊接工艺”——压熔焊,该技术是传统电阻点焊的改进升级。在具体应用中,上、下电极在焊接压力作用下,连同多层极耳和极柱盖板一起压紧,并利用电流通过焊件接头的接触面及邻近区域产生的电阻热,将被焊金属加热到局部熔化或达到高温塑性状态,形成牢固的焊接头,实现“一步式”焊接,如图原理示意。
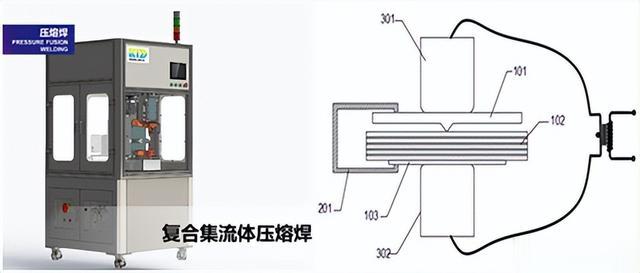
压熔焊设备模型以及焊接原理示意图
压熔焊工艺优势
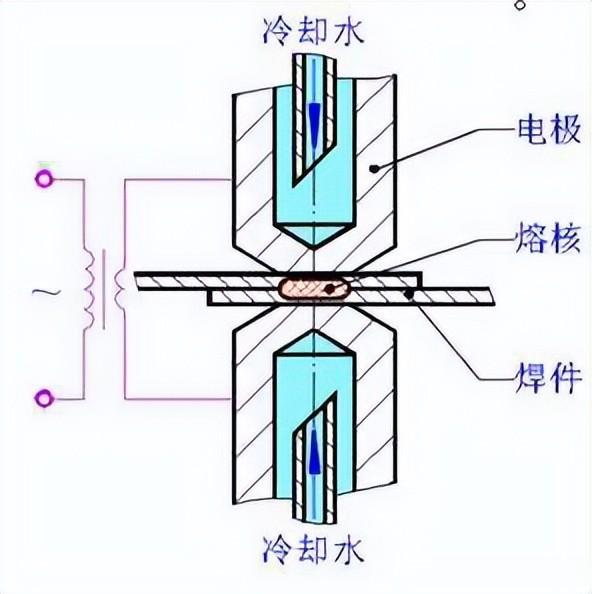
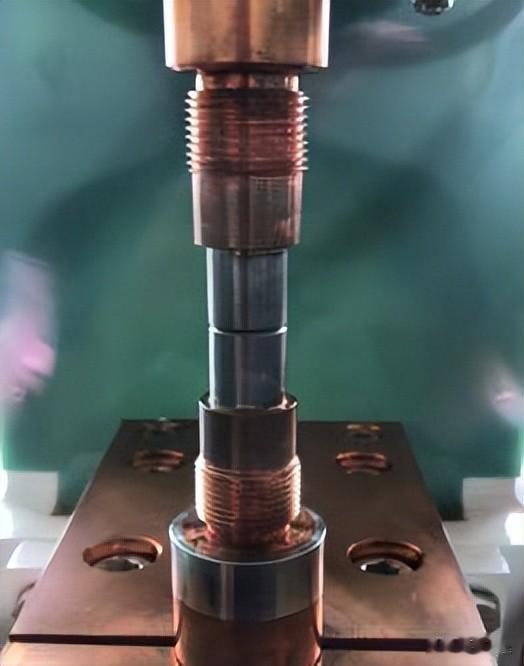
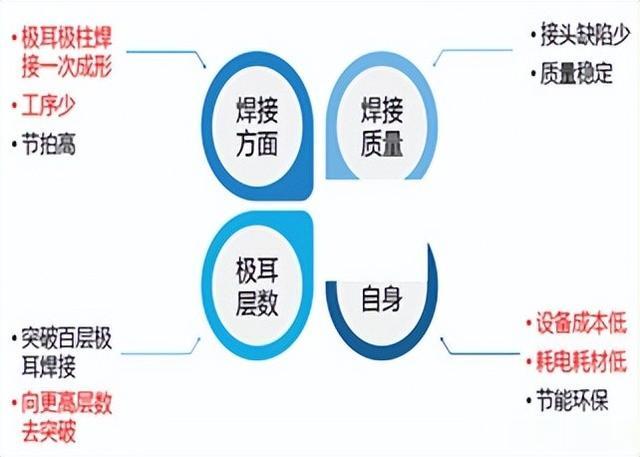
复合箔材焊接方式
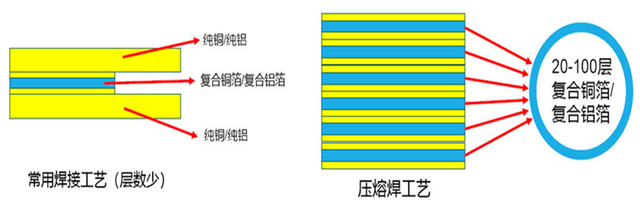
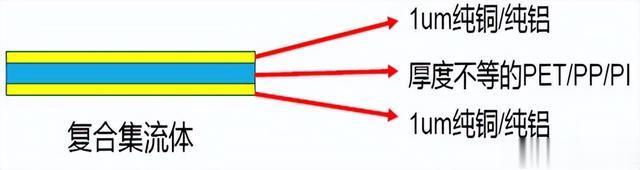
复合集流体焊接:
可实现间断涂布工艺焊接极耳+压熔焊
现阶段压熔焊设备的焊接效率有了显著提升,整机设备已能满足主流30ppm产线节拍,据悉卡洛维德压熔焊工艺有望逐步导入头部电池企业产线,首先用于铜铝箔的焊接,下半年还将推出全新一代复合集流体焊接工作站。焊接效果方面,压熔焊的多层极耳焊接达到铜箔、铝箔200层内水平,同时,压熔焊工艺可满足复合集流体焊接要求,目前可实现60层复合铜箔焊接,电阻0.006mΩ。
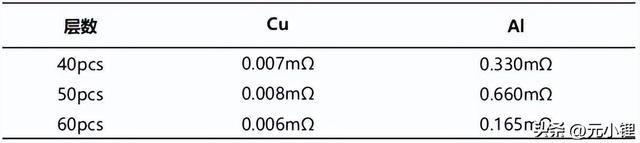
复合集流体焊后内阻测试(复合箔材+板材)
压熔焊技术突破
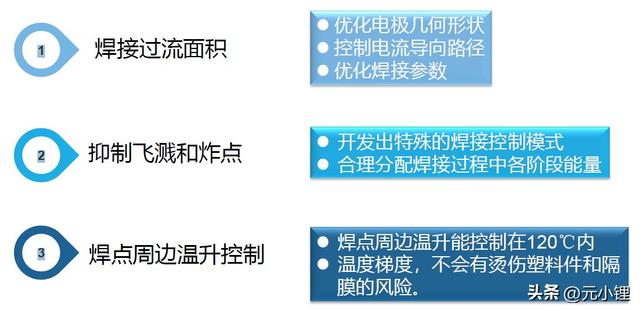
焊后正极金相
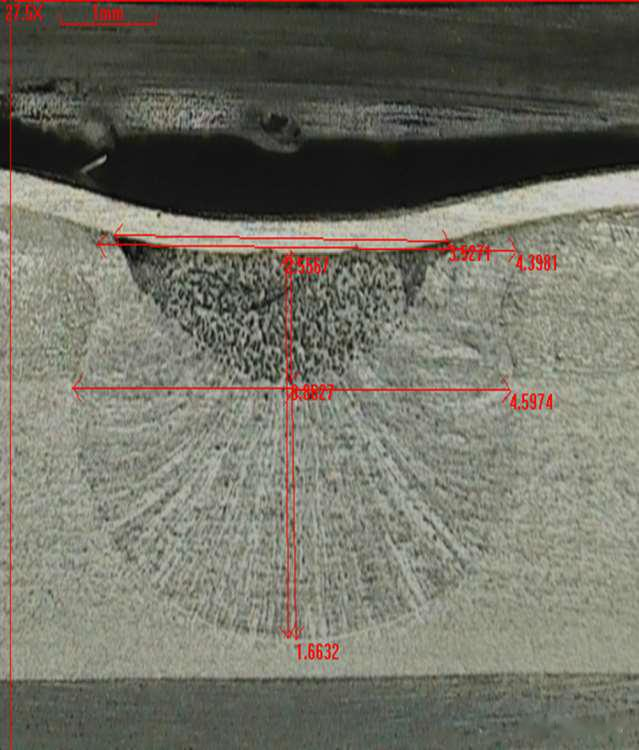
正极铝80层
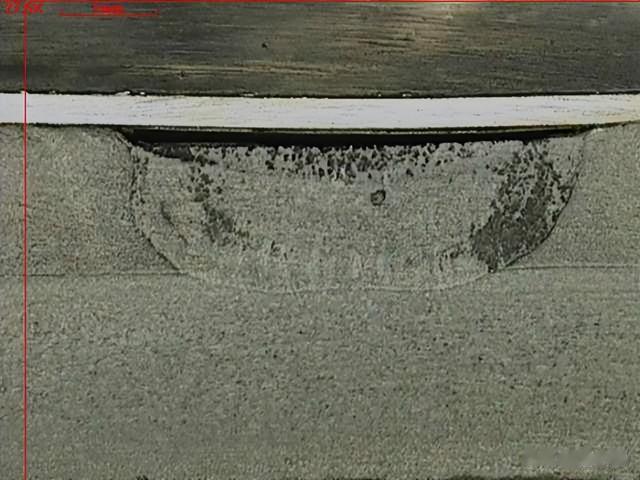
正极铝100层
焊后负极金相
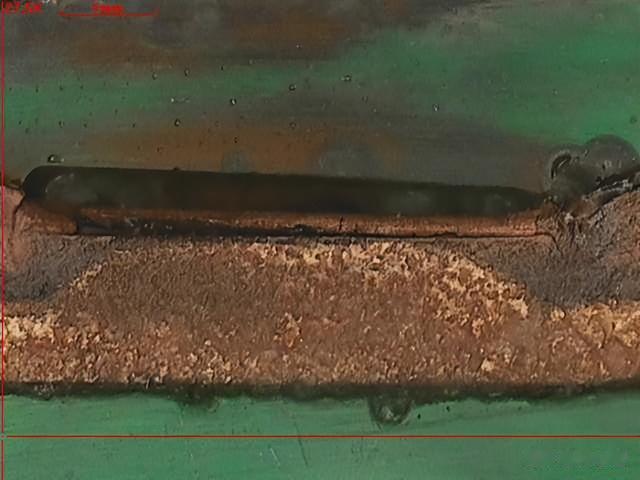
负极铜40层
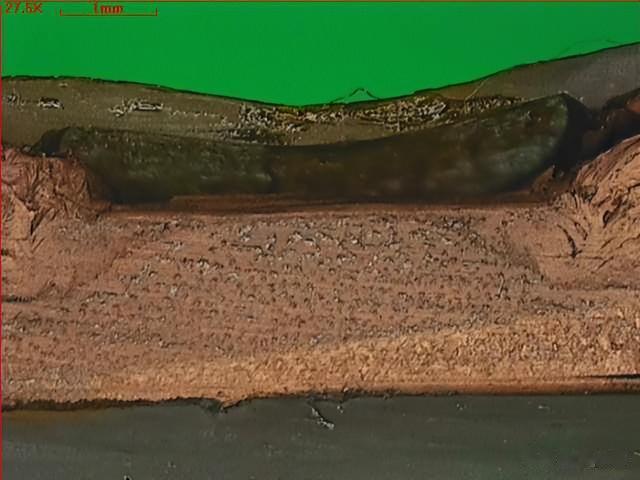
负极铜60层
焊后拉力测试
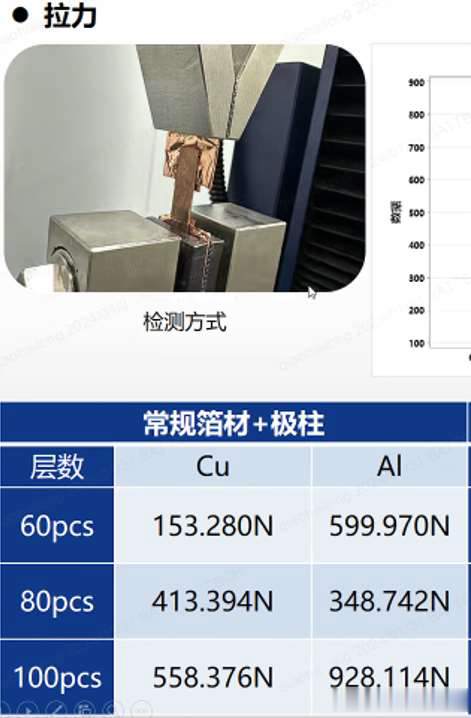
焊接后多项数据测试
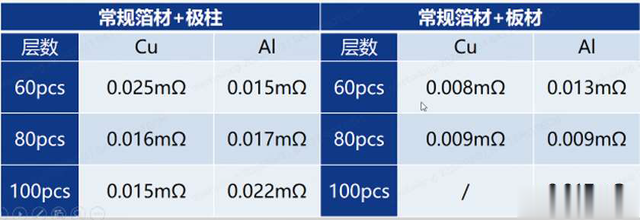
焊后内阻测试
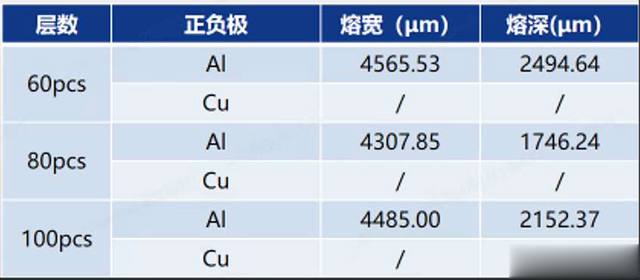
焊后金相测试
焊接后温度、过流温升测试
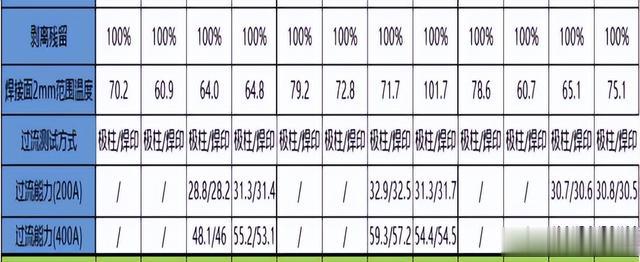
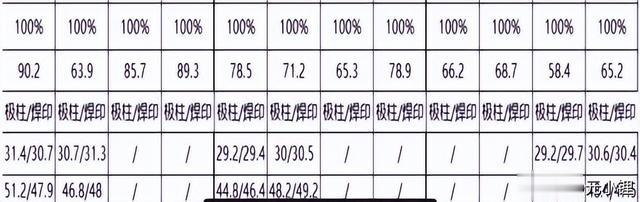
多层复合铜箔焊接
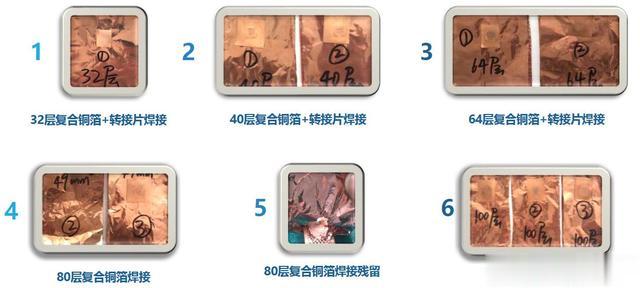
多层复合铝箔焊接
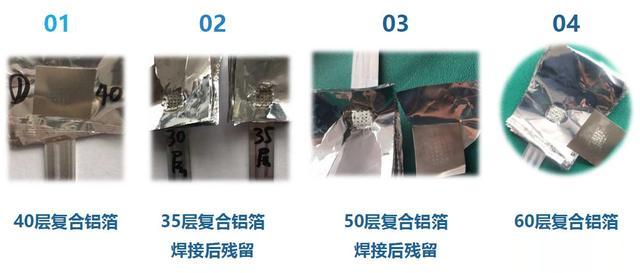
复合集流体焊后数据测试
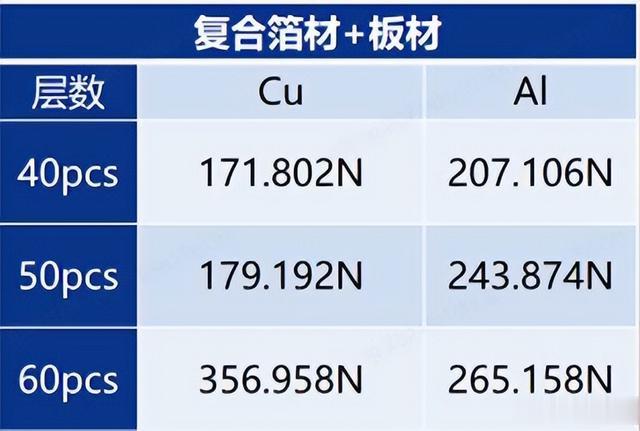
拉力测试

内阻测试
总结超声波滚焊工艺目前已经发展得相对成熟。当下,主要的工作重点在于对滚焊速度以及对齐精度进行更进一步的升级优化。头部电芯厂已经积极采取行动,采购了滚焊设备用于对复合集流体进行验证。具体而言,是在极片辊压工序完成之后,实施超声波滚焊操作,从而成功地实现了复合集流体极耳转接焊这一关键步骤。
压熔焊工艺则展现出了化繁为简的独特魅力。通过将多层极耳与极耳极柱进行焊接,可满足100层以内的复合集流体与极柱的焊接;实现复合集流体到极柱焊接的“一步法”。焊接过程中无飞溅、无炸点现象发生;焊接工序操作简单;设备自身便于集成到产线。这样不仅显著提高了生产效率,还成功降低了成本。其具备的显著优势吸引了市场的关注与验证,市场普遍预期其有望在今年下半年逐步导入头部电池企业的产线。
随着时间的推移,复合集流体的耐焊性呈现出持续增强的良好态势。与此同时,焊接设备与产线之间的适配性也在稳步提升,二者相辅相成,共同发挥着积极的作用。
正因如此,复合集流体在电芯制程端长期以来一直存在的那些主要问题,正逐步、有序且有效地得到了解决。曾经困扰行业发展的难题,如今正一个接一个地被攻克,为产业的进步铺平了道路。
这一令人欣喜的积极变化,毫无疑问将会为复合集流体的产业化进程注入汹涌澎湃且强大无比的动力。就如同为一艘正在航行的巨轮增添了更为强劲的引擎,使其能够在发展的海洋中破浪前行。
这种强大的动力,必然会进一步加快复合集流体产业化的步伐,使其不再受到以往种种限制的束缚,能够以更快的速度向前迈进。
而且,这一变化还将产生广泛而深远的影响,有力地推动整个行业朝着崭新的发展阶段奋勇前进。促使行业不断创新、升级,开拓出更为广阔的发展空间,迎来前所未有的繁荣景象。