高能量密度的锂离子电池在经历了机械滥用、电滥用和热滥用后,电池内部材料发生破坏,释放大量气体,并发生副反应使其发生热失控。而锂离子电池引发热失控是导致锂离子电池燃烧甚至爆炸的主要原因。
然而对于新一代高比能硅碳负极材料在锂离子电池中的热失控特征行为研究比较少。本研究分别以硅碳材料和石墨为负极活性物质,以NCM811为正极活性物质,设计制造成86Ah的软包锂离子电池,通过针刺实验、过充实验和外部加热实验来分析电池热失控过程。对比了硅碳负极和石墨负极热失控特性以及热量产生特点,为今后的热失控预防与后处理提供了理论支撑。
1 实验
1.1 样品
实验样品均为本公司生产的软包动力电池。对于硅碳负极软包电池,正极采用湖北容百锂电材料有限公司的三元NCM811,负极采用来自于贝特瑞新材料集团股份有限公司的硅碳负极材料,比容量为420mAh/g;对于石墨负极软包电池,正极采用湖北容百锂电材料有限公司的三元NCM811,负极采用来自于贝特瑞新材料集团股份有限公司的人造石墨,比容量为350 mAh/g;二者电解液均采用天赐高镍电解液,隔膜均采用PE膜。电芯容量设计为86Ah,由此比较不同体系下硅碳和石墨材料两方案的安全性。
1.2 实验方案
针刺测试:针刺测试按照GB/T 31485-2015《电动汽车用动力蓄电池安全要求及试验方法》和GB/T31467.3-2015《电动汽车用锂离子动力蓄电池包和系统测试要求》标准要求进行测试,设备为大型动力电池挤压针刺综合实验台,可满足单个或多个各种类型电池的针刺实验需求。
实验设备如图1(a)所示,该实验采用电池挤压针刺试验机,实验舱的规格为长×宽×高=1500mm×1000mm×2100mm。该针刺钢针采用碳钢材质钢针,钢针直径为3mm,针尖呈圆锥形。先将电池静置30min,随后以0.33C进行恒流充电,直至电压为4.2V;随后转为4.2V恒电压充电至截止电流为0.05C后停止。随后钢针以10mm/s的速度垂直插入软包电池正中心,刺入深度为1.1mm,刺穿负极片4层,监测整个测试房的温度,并分别在电池正面中心、电池背面中心、电池正极极耳、负极极耳处和电池侧面处安置热电偶,分别记为T1、T2、T3、T4 和T5,如图2(a)。
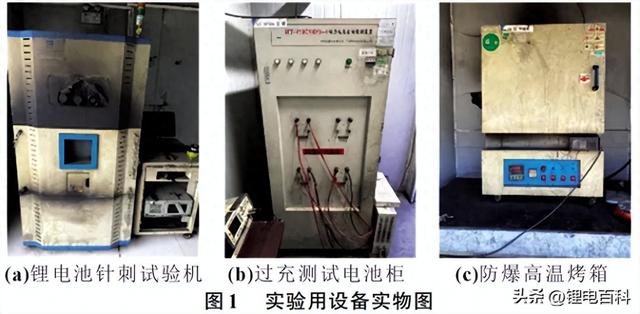
过充测试:实验设备如图1(b)所示,其电压量程为0~50V,电流量程为0~50A。在常温下,将软包电池以0.33C进行恒流充电,直至电压为4.2V,进行恒压充电0.05C截止电流,装入夹具;静置5min;将软包电池以0.33C充电至4.62V。如图2(b),并分别在电池正面中心、电池背面中心、电池正极极耳、负极极耳处和电池侧面处安置热电偶,记为Ta、Tb、Tc和Td表示,环境温度用Te表示。
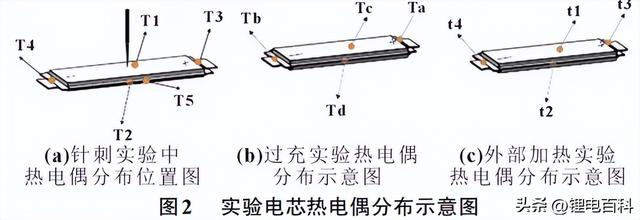
外部加热测试:如图1(c)所示,测试设备为防爆高温烤箱,其升温范围为室温-300℃。首先在25℃下,0.33C恒流充电至4.2V,随后转为4.2V恒电压充电至截止电流为0.05C,装在夹具上;测试从30℃开始,升温速率为5℃/min,在设定温度下30℃静置1h,持续升温,直到电池起火。在实验过程中,设置5处温度监测点,即分别放置在电池正面、后面、正极极耳、负极极耳和电池周围。如图2(c),并分别在电池正面中心、电池背面中心、电池正极极耳、负极极耳处和电池侧面处安置热电偶,记为t1、t2、t3和t4表示,环境温度用t5表示。
2 结果与讨论
2.1 针刺实验对硅碳和石墨负极软包电池引发热失控的影响
图3(a)、(c)和图3(b)、(d)分别为针刺实验前的100% SOC的硅碳负极材料软包电池和石墨负极软包电池,经过针刺实验后,两种软包电池分别受到不同程度的损毁。
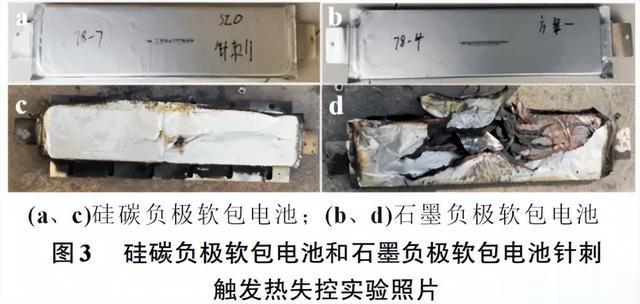
如图4(a)中红色区域标注所示,在硅碳材料针刺实验中,在第3788s钢针刺入电池,电压开始下降,同时从T3处观测到电池内部急剧放热在6s后,即在第3794s时温度达到最大值,此时温度已经超过热电偶的量程,温度在1500℃以上。电池内部隔膜已经融化,电池材料大量反应,释放大量的热。随后其他热电偶上也检测到升温,铝塑膜开始融化,电池内部材料直接和空气接触反应,反应速率减缓,反应温度慢慢下降。
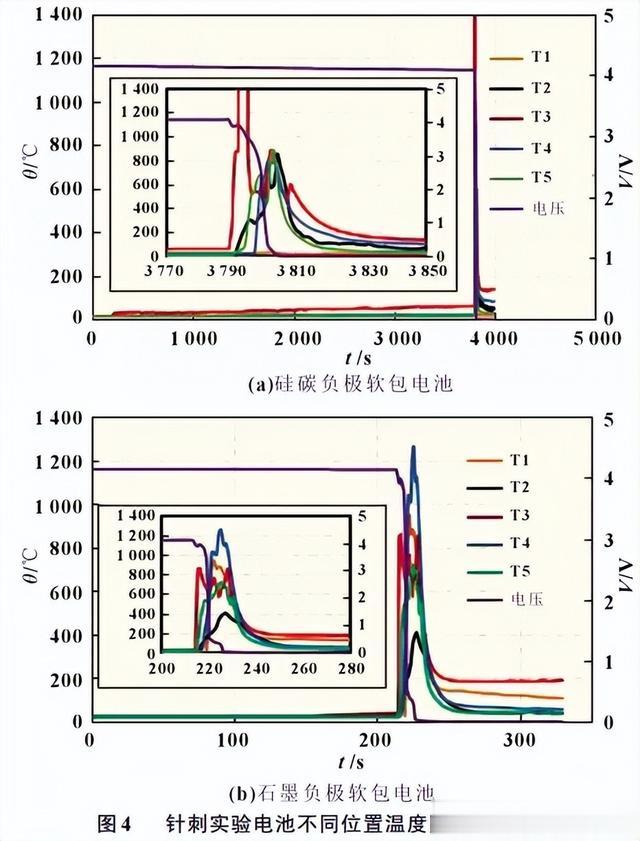
在石墨材料针刺实验中,钢针在第223s刺入电池,随后电压急速下降,说明电池内部已经开始发生短路现象。同时在T3、T5处检测到温度急剧上升的现象。电压在下降一段时间后出现了一个短暂恢复的现象,这可能是由于针刺实验导致电池内部发生短路,改变了电池内部的一些物质组成,导致副反应发生,使得电池内部极化改变。
电池热失控是一个热-温-反应闭环的过程而针刺导致电压的变化实际上是热动力学与电化学相互转化的一个过程,图 4(a)、(b)中的电压上升可以看作是热反应转化为电化学的一个过程。随着针刺实验的进行,在第225s放热加剧,并且在T1、T2和T4处的热电偶上检测到明显的升温现象,这说明了电池短路愈发严重,电化学反应急剧发生并放出大量的热。T4在升温的过程中,在232s处出现了短暂的温度下降过程,随后在238s处温度达到最高点1272℃。这个温度远高于铝塑膜的熔点(660℃),说明此时电池外壳可能已经融化燃烧。热电偶直接暴露在热失控区域,此时大量的电池材料已经反应,热电偶周边已经没有材料进行反应,随后温度开始逐渐降低,转化为缓慢燃烧,此时电压也降为0V。
将硅碳体系电池的针刺失效过程与石墨体系电池针刺失效过程对比,硅碳体系电池热失控最高温度达到1500℃以上,超过我们测试设备的量程,而石墨体系电池热失控最高温度为1272℃。同时到达最高温度的时间上,硅碳负极软包电池比石墨负极软包电池更快达到热失控最高温度。其主要原因是硅碳材料产气量大,体积膨胀大,在热失控的时候,爆发出大量的热量,具有比石墨软包电池更差的安全性能。
2.2 过充对硅碳负极和石墨负极软包电池安全性能的影响
图5(a)为过充前硅碳负极软包电池,图5(b)为过充前石墨负极软包电池,图5(c)为过充后硅碳负极软包电池,图5(d)为过充后的石墨软包电池。从电池表面上看,石墨负极和硅碳负极软包电池并无明显变化,未发生胀气、鼓包等现象。

通过热电偶反应该点各个阶段温度实时变化情况,以最先发生升温的热电偶作为研究对象。整个电池经历了四个阶段:电压正常增长阶段;过充时电压急速增长阶段;过充电压出现下降阶段和电压稳定阶段。将这四个阶段分别按V1、V2、V3和V4表示。
图6(a)中,对应V1阶段,此时硅碳电池电压正常升高,电池表面各温度监测点变化不大,持续时间为229 s。当电压达到约4.2V时开始进入V2阶段,此时正极中几乎90% 的Li进入了负极。随着充电的继续,进入过度充电阶段,电池电压急速上升,此时没有Li+进入负极,而负极是硅碳材料,极片体积膨胀更大,导致负极侧电流密度分布不均匀,产生锂枝晶,发生副反应并产生大量的热,使得温度迅速上升到较高的温度。
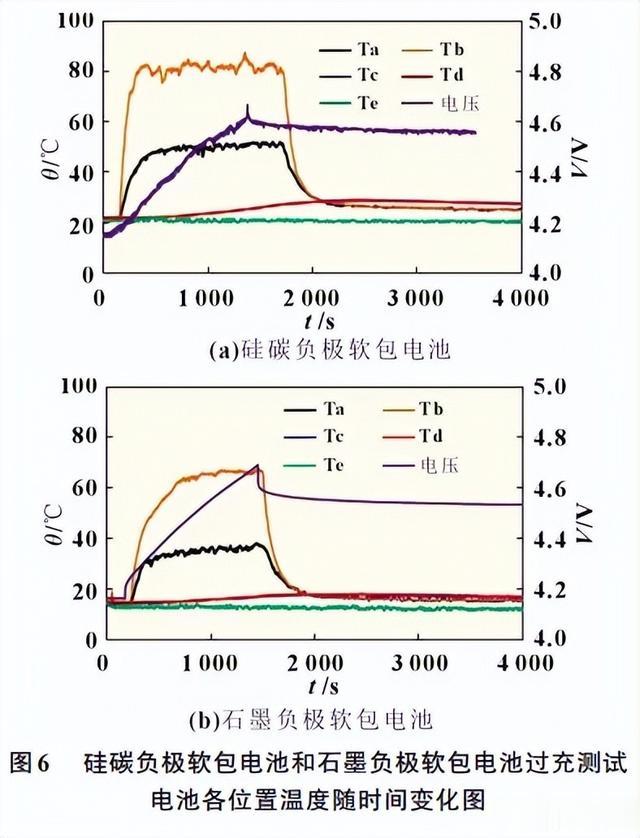
图6(b)中,负极为石墨材料,进入过充阶段,相比于硅碳材料,石墨极片体积膨胀较小,缓慢产生锂枝晶,故图6(b)中温度缓慢上升。由于整个系统为敞开系统存在与外界热交换的现象以及副反应放热不稳定的原因使得温度存在一定的波动,而正极端几乎无锂枝晶产生,使得温度比负极端低,温度波动也小一些。随后电压在第1062s时上升趋势减缓,热电偶监测到的温度始终维持在一个较高水平,这与电池内部的副反应直接相关,过充导致电压过高,电解液部分分解。随后电池电压从1376s时开始下降,此时进入了V3阶段,这是因为电池内部由于锂的持续沉积,导致负极表面形成大量的锂枝晶以及锂沉积层使得电池在短时间内造成微短路;此时电解液持续被分解,发生大量副反应,释放大量的热。在Tb(负极极耳处)的热电偶也检测到温度起伏的变化,第 1354s处检测到的最高温度为87.7℃;在Ta(正极极耳处)的热电偶处检测到最高温度为53.4℃。在正极端由于几乎不会有锂沉积,其主要的热量源来自于电解液与正极材料的副反应。最后到了V4阶段,在电压达到4.62V后停止充电,在经历了微短路导致电池电压下降后电压慢慢稳定在4.58V左右。
对于图6(b)石墨软包电池,电池进入V1阶段,电池先在0.33C下充到4.2V,随后进入V2阶段开始过充,在第1445s结束该阶段。在V2阶段,硅碳负极电池电压上升速率远远大于石墨,可能是因为石墨在过充过程中,锂沉积比硅碳材料更严重,大量锂沉积在负极表面,将 SEI 膜覆盖后导致锂离子嵌入更困难,增大阻力。随后进入了V3阶段,同硅碳负极电池一样,电压开始下降,主要是因为在高电压下,部分电解液出现了分解现象,同时包裹在SEI膜表面的“死锂”与SEI膜和电解液发生副反应。最后进入了V4阶段,电压开始逐渐稳定下来。整个石墨负极电池在过充实验中,电池在第1354s达到温度最高点为67.4℃,正极热电偶检测到的最高温度为37.9℃。
从整个过充实验来看,硅碳负极软包电池无论是从最高温度还是放热持续时间来看均比石墨负极软包电池高。相比于石墨负极软包电池,硅碳负极软包电池的安全性能较差,其主要是因为在过充过程中由于硅碳材料体积膨胀大,同时产气量大,并且 SEI膜反复重构,释放大量的热量。
2.3 外部加热对硅碳和石墨负极软包电池引发热失控的影响
图7展示了硅碳软包电池和石墨基软包电池在100% SOC条件下外部加热引发热失控的过程实物图。图(a)和图(b)分别是硅碳负极和石墨负极外部加热之前的软包电池实物图,随着对电池持续加热,能看到电池发生热失控并起火燃烧[图(c)和图(d)]。
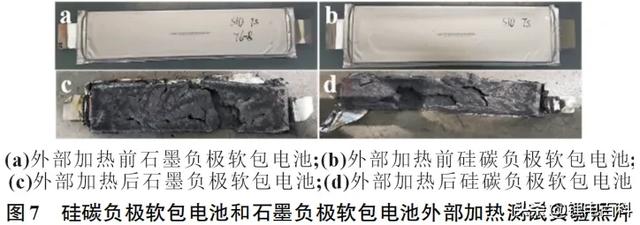
通过各个热电偶显示的数据分别绘制温度、电压随时间变化的曲线如图8所示,其中图(c)和图(d)为图(a)和图(b)的局部放大图。整个电池在恒温箱内以恒定功率加热升温。将这个热失控过程分为三个阶段,用s1,s2和s3表示。在s1阶段,两种电池的各个监测点的温度缓慢上升,大约在80℃左右,SEI膜发生分解再重构现象,放出少量的热。随着温度继续上升,大约在110℃左右,SEI膜开始被分解,脱落,并且放热,此时内部放热和外部加热在同时进行。
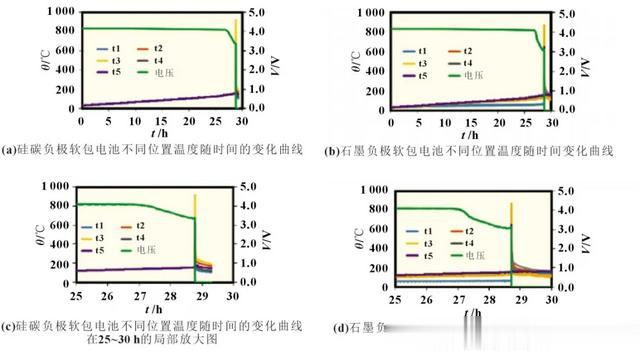
图8 100% SOC硅碳负极体系以及石墨负极体系锂离子电池
加热诱发热失控过程
而此时硅碳负极软包电池在105.4℃左右发生电解液漏液现象;石墨负极软包电池在110.1℃处发生电解液漏液现象。在此时,负极中被嵌的Li+直接与电解液反应,携带着大量的副反应,再次生成新的SEI膜,这个阶段同时产生了H2、CO2、O2等气体,这些气体进一步加速产热。这个阶段环境温度t5处比电池中其他温度高一些,可能是因为有热的气体溢出,t5处的热电偶检测到了热的溢出气体温度。随着内部产热和外部加热的热量叠加,体系温度很快达到隔膜的收缩温度(121℃),隔膜开始收缩融化,加热速率也进一步增加。随后进入到s2阶段,此时温度上升到隔膜的融化温度。隔膜融化,正负极极片接触,电池短路,电压开始下降,释放大量的焦耳热。同时电解液直接与活性锂接触,电压急速下降到0V,发生大量的副反应,释放大量化学反应热,使得温度迅速达到热失控最高温度,电池剧烈燃烧]。
将硅碳体系电池的外部加热引发热失控过程与石墨体系电池外部加热引发热失控过程对比,硅碳体系电池热失控最高温度可达到866.2℃,而石墨体系电池热失控最高温度为801.1℃。同时到达最高温度的时间上,石墨体系电池晚于硅碳材料体系电池,石墨体系电池在第28.71h时达到热失控最高温度,而硅碳负极电池在28.77h时达到热失控最高温度。可能的原因是硅碳负极在电池内部形成的SEI膜反复破碎再生,以及硅的体积膨胀和引发的副反应释放的大量热量远大于石墨基负极。
3 结论
在本研究中,以石墨负极软包电池和硅碳负极软包电池为研究对象,通过针刺实验、过充实验和外部加热引发热失控三种模式对比了石墨负极软包电池和硅碳负极软包电池安全性。在针刺实验中,硅碳负极软包电池热失控达到的最大温度在1500℃以上,远超于石墨负极软包电池(1272℃);在过充实验中,硅碳负极软包电池无论是从最高温度(87.7℃)还是放热持续时间均比石墨负极软包电池(67.4℃)高;在外部加热引发热失控实验,硅碳负极软包电池(866.2℃)比石墨负极软包电池(801.1℃)热失控最高温度高,同时硅碳负极软包电池温度上升速率相对较快。对于硅碳负极软包电池的安全性还面临巨大的挑战,从电池热管理上,还需要对硅碳负极软包电池进行更加行之有效的设计,如在材料上,可对电解液进行改进,减少电解液与硅碳材料副反应的发生,优化硅碳材料结构,降低硅的体积膨胀率,进一步提高硅碳负极材料的安全性。
文献参考:李红生,李慧,萧厚桂,熊得军.石墨负极和硅碳负极软包动力电池热失控特性研究[J].电源技术,2023,47(11):1404-1408
文章来源:电池技术TOP+
注:本站转载的文章大部分收集于互联网,文章版权归原作者及原出处所有。文中观点仅供分享交流,如涉及版权等问题,请您告知,我将及时处理!