干法电极技术早期主要被用于超级电容器制备,与湿法电极技术相比,干法工艺主要是将活性颗粒、导电剂和进行干混均匀后加入粘接剂,在粘接剂原纤化作用下形成自支撑膜,最后辊压覆盖在集流体表面。干法制膜的工艺主要包括粘接剂原纤化法和静电喷涂法两大类,其中静电喷涂法在后续的可加工性、粘连稳固性、电极柔韧和耐久上表现不如粘接剂原纤化法。其中2019年被特斯拉收购的Maxwell主要采用是粘结剂原纤化,日本Toyota主要采用静电喷涂法,美国和日本在干法工艺上处于领先地位,工艺简图分别如下。左图为粘结剂原纤化示意图,右图为静电喷涂工艺示意图。
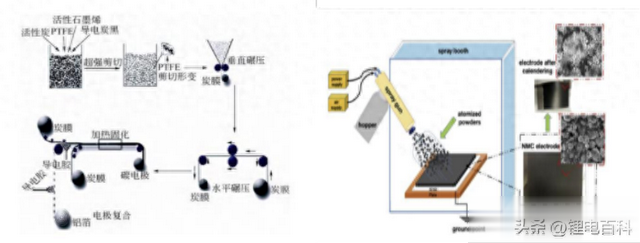
干法电极相比湿法电极技术应用的难点主要包括:粘接要求更高,锂电池比表面积小,锂离子脱嵌带来的膨胀系数高,多次循环后干法容易脱粉,需要开发相应的粘结剂;保持活性物质不被破坏,干混制膜过程可能破坏活性物质,需要对原纤化制膜机的性能进行提升;电池内部阻抗大,集流体与活性物质界面阻抗大,大电流下可能存在极化问题,固-固界面阻抗大;PTEE 易与负极发生反应,PTFE 的LUMO 轨道能量更低,容易接 受电子,导致电池容量下降;正极辊压要求更高,正极活性材料电化学活性高,辊压过程中容易发生化学变化;辊压后自支撑膜仍容易掉粉;粘接剂分布均匀要求更高,PTFE 粘接剂粒径大,削弱粘连效果,尤其是正极配方中正极活性物质与其它材料密度差距较大,导致分散较难。干法电极工艺在正极中应用的挑战更大。
最近三星SDI公开了一项专利US 2024322168 A1,采用添加导电添加剂和其它化学物质用以解决干法电极工业化面临的问题,根据实施案例描述的信息,主要如下:第一,导电添加剂制备,利用CVD化学气相沉积在1000°C下7.5h下制备石墨烯@ Al2O3 颗粒(平均直径:20nm),其中导电添加剂中Al2Oz(0 < z < 3) 质量分数为 60%。第二,混料,将LiNi0.91Co0.05Al0.04O2、上述导电添加剂、碳纳米管按照质量比为 99.75 : 0.2 : 0.05)进行研磨,研磨工艺为,5-30分钟,1,000-2,000 转/分钟,混合均匀得到分散好的干混料。第三,干法电极模的制备,将所得干混材料、LiNO3、琥珀腈、CNT、科琴黑和 PTFE(聚四氟乙烯)按照质量比为95 : 0.5 : 0.5 : 1.4 : 0.6 : 2再一次混合并纤维化,所得混合物被挤压成自立式正电极薄膜,然后进行辊压(3.5 吨/平方厘米,厚度:150微米);第四,干法电极制备,将上述薄膜层压到预先涂碳铝箔上。利用半电池对上述干法电极制备的正极电极进行电化学性能测试,经过 350 次循环(0.1 C 充电/放电)后测得的容量保持率为 94.6%,采用本工艺提升了干法电极正极的循环性能。

文章来源:储能及新材料技术洞察
注:本站转载的文章大部分收集于互联网,文章版权归原作者及原出处所有。文中观点仅供分享交流,如涉及版权等问题,请您告知,我将及时处理!