在新能源汽车产业发展方兴未艾之时,动力电池装机量逐年上升,动力电池退役量也随之同步增长。
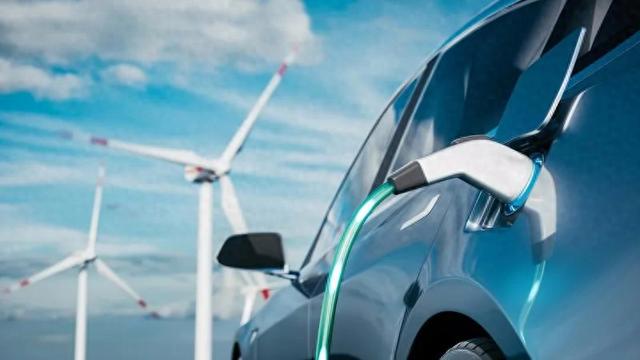
我国电池回收产业,最早要从2001年说起,彼时格林美便已踏上探索以电池材料回收为核心的绿色循环技术产业化之路。格林美历经了2001—2002年的产品开发阶段、2003—2019年的产业化阶段,于2010年在荆门开启构建核心循环产业群的全国布局阶段,2011年至今,国外项目重产线开通,迈入全球发展阶段。
同一时期的电池回收龙头企业,还有邦普循环。或许这个名字大家并不耳熟能详,它是宁德时代的控股子公司。创始人李长东于2003年创立该企业,专业从事各类废旧镍氢、镍镉、锂离子二次电池中的废镍、废钴回收与处理,迅速发展成为中国最大的库存二次电池再利用、废旧二次电池拆解及其再资源化供应商。
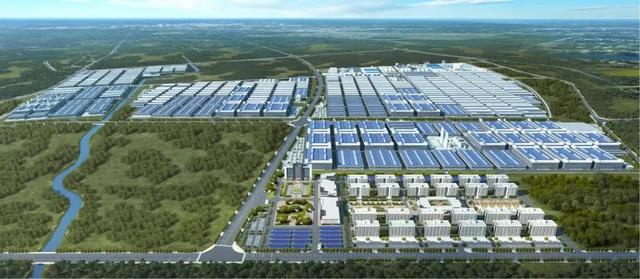
宁德时代-邦普一体化电池材料产业园
邦普循环在全球废旧电池回收领域率先攻克了“废料还原”这一行业性难题,并且构建起上下游优势互补的电池全产业链循环体系。
一个聚焦电池全产业链循环体系,一个专注于废旧动力电池回收、镍钴锂钨战略资源再造等领域。都为我国电池回收产业的发展奠定了基石。
这两家电池回收的龙头企业,一个聚焦电池全产业链循环体系,一个专注于废旧动力电池回收以及镍钴锂钨战略资源再造等领域。两者均为我国电池回收产业的蓬勃发展奠定了坚实基石。
当前,锂电回收技术主要有湿法和火法两大工艺路线,相比海外常见的火法回收工艺,湿法冶金路线基于溶液化学反应,在较低温度下将金属元素转化为金属离子,再通过后续提纯和沉淀过程得到目标材料,不仅可方便地适配磷酸铁锂回收需求,在能耗与碳足迹上较火法也有明显优势,瞄准短流程低成本的应用需求,邦普、格林美等本土龙头企业已经对湿法工艺进行了大量改进。
如邦普循环首创的定向循环技术DRT,通过短程资源再生工艺把废旧电池中的核心金属循环再造成为新材料,在全球废旧电池回收领域率先破解了“废料还原”的行业性难题,电池产品核心金属材料总回收率达到99.3%以上。
尽管技术有所突破,但在产业化进程中依旧面临诸多障碍。
截至2023年,我国废旧动力电池退役量超过58万吨。根据中国汽车工程学会的预测,到2030年,我国退役动力电池的规模将达到350万吨,市场规模预计增长到1406亿元,远高于2023年的58万吨。这一庞大的市场需求亟需更高效、更低碳的技术手段与回收产业的完善配套。
就回收路径而言,不同型号的电池在材料成分、结构设计上各异,导致回收过程复杂。尤其是高能密度电池,回收过程中风险系数较高,存在爆炸、泄漏等隐患。
根据国务院发展研究中心2023年发布的调查研究报告,截至2023年底,中国新能源汽车动力电池的规范化回收率不足25%。市场准入门槛低、闭环回收利用链条不清晰、标准体系不完善、技术水平偏低、政策体系不健全以及商业模式创新不足等均是动力电池回收行业的弊端所在。
约75%的废旧电池被“小作坊”(指不具备回收拆解资质的小工厂)及尚未进入电池回收企业白名单(工信部发布的符合《新能源汽车废旧动力蓄电池综合利用行业规范条件》的企业名单,共计156家企业)的企业消化,而“小作坊”的回收率远超正规企业,其通常隐蔽性强,监管难度大,安全隐患突出。导致无序回收,加剧环境污染问题。
市场生态的改变,需要时间,更需要相关部门自上而下地对退役动力电池回收渠道做出非常明确且强制的规定,且出台关于动力电池回收利用的法律文件。
当前处于回收技术与产业化进程的发展初期,一边要扩大动力电池回收规模,一边要管理其市场秩序,还要面对《欧盟电池和废电池法规》中的强制性要求,多重挑战如何迎刃而解?
我国作为全球最大的电池生产国,要在短时间内实现碳足迹标识认证,对企业数据追踪和管理能力有了高标准、高要求。近日,市场监督管理总局等部门已开展产品碳足迹标识认证试点工作,包括锂电池在内的多个领域正在进行试点,以推动相关政策的引导和激励机制的完善。除政策法规先行外,相关行业企业在加速技术创新的同时,需在电池设计阶段就考虑其全生命周期的可回收性,提高电池的回收效率。
电池回收技术的进步、回收路径的选择和政策引导均是推动行业发展的多重动力,对于提升相关企业在国际市场的竞争力、实现产业的绿色发展、构建电池材料回收的绿色循环技术产业化之路具有重要作用。