原创 johnxing 设备维修号
1
轴旋转油封位置进行硬化处理的原因
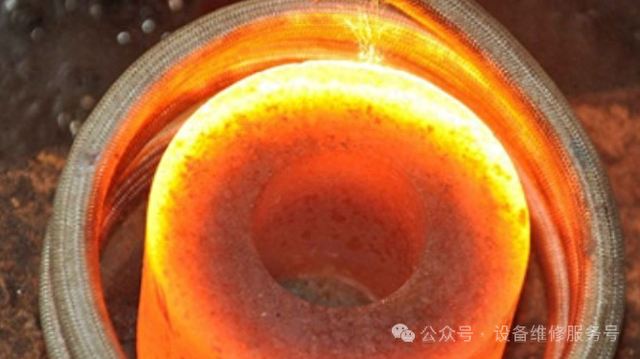
一、提高耐磨性
应对摩擦磨损
在旋转油封工作过程中,油封的唇部与旋转轴表面不断发生相对摩擦。如果油封安装位置的表面硬度不够,容易被磨损,导致油封密封效果下降。例如,在发动机曲轴油封处,曲轴的高速旋转会使油封唇部承受较大的摩擦力,经过硬化处理的油封安装位置(如发动机缸体上的油封座)能够更好地抵抗这种摩擦,减少磨损,从而延长油封的使用寿命。
对于一些在恶劣工作环境下的旋转设备,如矿山机械中的旋转轴油封位置,可能会受到灰尘、砂粒等杂质的侵入,加剧磨损。硬化处理后的表面能够有效抵御这些杂质带来的额外磨损,保持油封的密封性能。
二、增强抗变形能力
抵抗压力变形
旋转油封在工作时,尤其是在承受较高的油压或气压时,会对油封安装位置产生一定的压力。如果该位置的材料硬度不足,可能会发生局部变形,破坏油封的密封结构。例如,在液压系统中的旋转轴密封部位,液压油的压力会作用在油封及其安装位置上。经过硬化处理的安装位置能够更好地抵抗这种压力,保持其形状的稳定性,确保油封能够正常工作,防止液压油泄漏。
在一些高速旋转的设备中,离心力也会对油封安装位置产生影响。硬化处理后的表面能够增强结构强度,避免因离心力作用而产生变形,从而维持油封良好的密封状态。
三、改善表面粗糙度
优化密封配合
硬化处理过程通常可以使油封位置的表面粗糙度得到改善。合适的表面粗糙度对于油封的密封效果至关重要。如果表面过于粗糙,油封唇部难以紧密贴合,容易产生泄漏;而表面过于光滑,又可能影响油封唇部的润滑,导致过度磨损。通过硬化处理,可以将表面粗糙度控制在一个合适的范围内,例如通过研磨、镀铬等硬化处理方法,使表面达到 Ra0.8 - Ra1.6(粗糙度值)的范围,从而提高油封与安装位置之间的密封配合精度。四、提高耐腐蚀性适应恶劣环境在一些特殊环境中,如化工设备中的旋转轴密封,可能会接触到腐蚀性介质。硬化处理可以使油封位置的表面形成一层具有一定耐腐蚀性的保护膜,如镀铬硬化处理后的铬层可以有效抵抗化学介质的侵蚀。这有助于保护油封安装位置的材料结构,防止其被腐蚀而影响油封的密封性能,延长设备的整体使用寿命。未进行硬化处理的轴油封位置常见故障
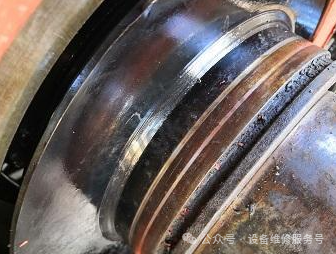
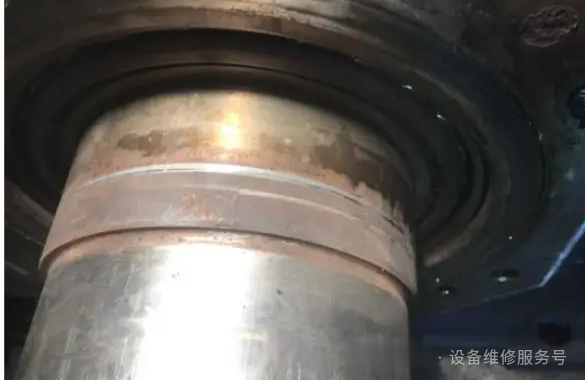
2
常见硬化处理的方法
一、表面淬火
火焰淬火原理:利用高温火焰对工件表面进行快速加热,使表面迅速达到淬火温度,然后通过喷水或其他冷却介质进行快速冷却,从而使表面获得马氏体组织,达到硬化的目的。例如,对于一些较大尺寸的轴类零件,火焰淬火可以在其表面形成一层硬度较高的硬化层。特点:设备简单、成本低、灵活性强,适用于各种形状和尺寸的工件,但淬火质量较难精确控制,容易产生过热、硬度不均匀等问题。感应淬火原理:将工件放入感应器内,当感应器内通入交变电流时,会在工件表面产生感应电流,由于集肤效应,电流集中在工件表面,使表面迅速被加热到淬火温度,随后进行快速冷却。例如,在汽车曲轴的表面硬化处理中,感应淬火可在曲轴表面形成具有高硬度和高耐磨性的硬化层。特点:加热速度快、效率高、淬火层深度易于控制、表面质量好,但设备投资较大,适用于批量生产形状简单的轴类、齿轮类等零件。二、化学热处理
渗碳原理:将低碳钢或低碳合金钢工件置于富碳的介质中,在高温下使活性碳原子渗入工件表面,形成高碳的渗碳层,然后进行淬火和低温回火,使表面获得高硬度、高耐磨性和良好的抗疲劳性能。例如,在制造汽车变速器齿轮时,渗碳处理可提高齿轮表面的硬度和耐磨性,而心部仍保持良好的韧性。特点:能显著提高零件表面的硬度、耐磨性和疲劳强度,但处理时间较长,工艺复杂,渗碳后还需要进行后续的淬火和回火处理。渗氮原理:使氮原子渗入金属表面,形成富氮硬化层。渗氮过程通常在较低温度下进行,如气体渗氮是在氨气的气氛中,氨分解出的活性氮原子渗入工件表面。例如,在模具制造中,渗氮可提高模具表面的硬度、耐磨性、抗腐蚀性和抗咬合性。特点:渗氮层硬度高、耐磨性好、变形小、具有一定的抗腐蚀性,但渗氮层较薄,处理时间长,成本较高。碳氮共渗原理:同时向工件表面渗入碳和氮原子,综合了渗碳和渗氮的优点。可以在比渗碳低的温度下进行,缩短了处理时间。例如,一些机床的齿轮采用碳氮共渗处理,既能提高表面硬度和耐磨性,又能减少处理时间和变形。特点:处理温度较低、速度较快、变形较小,表面硬度、耐磨性和抗疲劳性能较好,但工艺控制相对复杂。三、表面镀覆
镀铬原理:采用电镀的方法在工件表面镀上一层铬。铬层具有高硬度、高耐磨性和良好的耐腐蚀性。例如,在一些活塞环的表面镀铬,可提高活塞环的耐磨性和耐腐蚀性,延长其使用寿命。特点:镀铬层硬度高、美观、具有较好的耐腐蚀性,但镀铬过程中会产生有毒的六价铬废水,对环境有污染,且镀铬层存在微裂纹,容易产生腐蚀源。镀硬镍原理:通过电镀在工件表面沉积一层镍,通过特殊的电镀工艺可以获得硬度较高的镍层。例如,在一些需要耐磨和抗腐蚀的小型精密零件表面镀硬镍,提高零件的表面性能。特点:镀硬镍层具有较好的耐磨性、耐腐蚀性和一定的硬度,电镀过程相对环保,但镍层的硬度与镀铬相比略低。四、喷丸强化
原理利用高速喷射的弹丸(如钢丸、玻璃丸等)撞击工件表面,使表面产生塑性变形,形成一定深度的冷作硬化层。弹丸的撞击使表面层的晶粒发生细化,位错密度增加,从而提高表面的硬度和抗疲劳性能。例如,在航空发动机叶片上进行喷丸强化处理,可以提高叶片的抗疲劳强度,延长其使用寿命。特点设备简单、操作方便、成本较低,能有效提高零件的表面硬度、抗疲劳性能和表面粗糙度,但强化效果受弹丸的种类、大小、喷射速度等因素影响较大。免责声明:尊重版权并感谢每一位作者的辛苦付出与创作;除无法溯源的文章,我们均在文末备注了来源;如文章视频、图片、文字涉及版权问题,请第一时间联系我们,将立即删除。