【化工科技装备大发展】系列-802
这是一个记录石油化工装备发展历史和取得成就的有趣系列合集
欢迎大家分享点评讨论交流,为化工装备现代化鼓劲加油
回顾历史 分享成就 展望未来
------------------------------------------------------------------------------
杭氧--国家大型化工装备的排头兵杭氧集团是国内第一台空分设备的制造者,大型、特大型空分设备产量和销量全球第一 ,神华宁煤十万等级空分设备被誉为“大国重器”,总体技术达到国际领先水平;乙烯冷箱等低温石化产品国内市场占有率第一,“复杂原料百万吨级乙烯成套技术研发及工业应用”项目获得国家科技进步奖一等奖。近年来,杭氧集团坚持“重两头、拓横向、做精品”发展战略,实现“工程总包-设备制造-气体运营”全产业链经营。目前已在全国范围内投资设立56家专业气体公司,总制氧能力超280万Nm3/h,气体产业已跻身国内第一梯队。
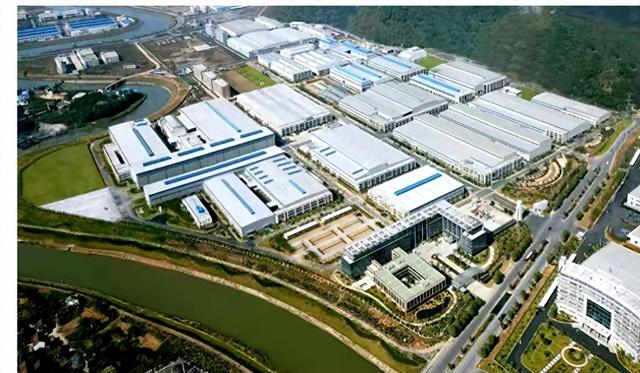
下面,我们就来看看杭氧作为国家大型化工装备的排头兵,在这几年攻克一项项技术壁垒,创造一个首台套,一项项的国产化装备。
打破国外企业对十万等级空分设备垄断创里程碑成就空分装置号称“煤化工之肺”,2000年以后,随着我国冶金、石化、煤化工等产业对大型、特大型空分设备需求的迅速增长,促进了我国空分设备行业的快速发展,设备最大规格迅速地从1万等级提高到了3万、4万、5万、6万等级,又从6万等级上升到了8~12万等级。
但是国内空分企业在大型空分设备招投标中和国际巨头同台竞技的机会并不多。
2010年之前国内大型工业气体空分装置基本都被国外巨头占有,国内空分行业其中杭氧为龙头企业,从首套3万级开始攻克,到6万级8万级,再到10万级,杭氧公司的每一次攻克都是国内首台套。
2011年神华包头煤制烯烃项目上,杭氧公司研制的4套6万级装置(近10亿元)开车成功,标志国内空分行业已具备大型装置的研发能力。
再到2017年6套10万级在神华宁煤项目上和林德平分秋色,到出口伊朗卡维12万级,国内空分行业一直在进步。
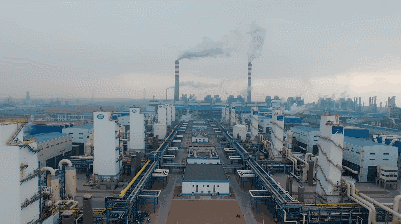
神华宁煤空分装置
在宁夏神华宁煤400万吨/年煤炭间接液化项目基地,十二套十万等级空分设备正开足马力,源源不断产出高浓度氧气,而其中六套空分设备,都是由杭州杭氧股份有限公司自主研发制造的。这一“国之重器”横空出世,以实测能耗指标优于当时世界上任何十万等级空分装置的国际先进水平,打破国外企业对十万等级空分设备垄断,堪称我国重大设备国产化的里程碑成就。
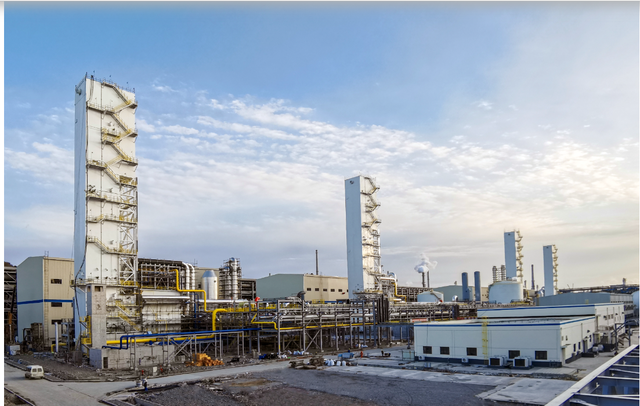
神华宁煤空分装置
据了解,在神华宁煤项目之前,世界上十万等级空分设备都由国外企业制造。2008年,杭氧决定啃下这块“硬骨头”。为了造出高质量设备,杭氧团队不断进行技术论证和沙盘推演,在32种流程方案中选出最优方案,在制造过程中,工作人员克服戈壁恶劣环境,每天面对3.6万多米长度的管道、6万多道焊口,在60多米高的冷箱内爬上爬下仔细检查确认。六年筹备,四年攻坚,杭氧“十年磨一剑”,空分设计研究院60余名科研人员同心协力,终于为十万等级空分设备打上中国制造标签。
2017年3月15日,第一套神华宁煤杭氧十万等级空分装置成功出氧!实时数据显示,氧纯度达到99.87%,超过99.6%的行业标准。这一年的8月25日,6套空分设备全部开车,其中8号空分设备能耗指标为202.8T/h,是世界上同规模在运行能耗最低的空分设备。当时参加评审的权威专家表示,神华宁煤十万等级空分项目已达世界先进水平,足以与世界空分行业鼻祖德国林德制造的另外六套设备分庭抗礼。
从“国际先进”到现在的“国际领先”,意味着十万等级空分设备国产化完成了关键一跃。据了解,目前,杭氧正努力攻关性能更优能耗更低规模更大的空分设备,国内单体规模最大整体冷箱已制造成功,十二万等级空分设备呼之欲出。
2024年国际首台(套)承托式滑动型径向流纯化装置2024年1月11日,浙江省经济和信息化厅、浙江省财政厅公布了2023年度浙江省首台(套)装备名单,杭氧集团《承托式滑动型径向流纯化装置》获得国际首台(套)。
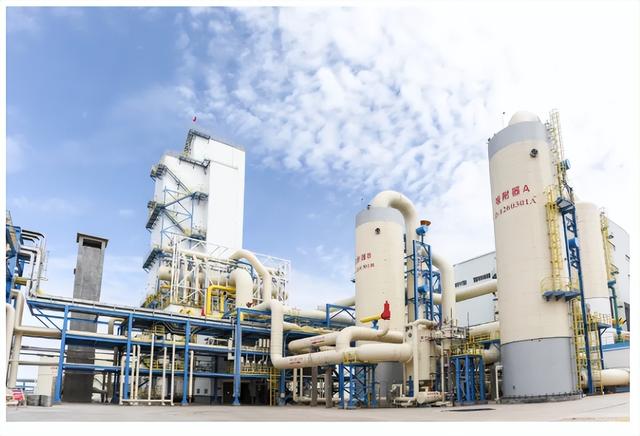
杭氧集团《承托式滑动型径向流纯化装置》
据介绍,该项目针对承托式滑动型径向流纯化装置的关键技术开展了研究,发明了一种可实现大伸缩变形的多层床径向流吸附器,首创内件微应力结构设计技术,实现工作过程中内部格栅自由伸缩,多层栅网接近零应力,提高了设备使用的可靠性。
研发了承托式滑动型径向流吸附器的长周期运行技术,延长了纯化系统的使用周期,提高了空分产品提取率,降低了运行能耗。
承托式滑动型径向流纯化装置攻克了径向流吸附器纯化系统的空气品质自适应的控制难题,实现纯化系统的运行随着大气中CO2含量、温度等参数的变化自动调节运行周期,提高系统可靠性和稳定性。
承托式滑动型径向流纯化装置项目相关技术已获国内发明专利5件,国际发明专利3件,实用新型专利10件。本装置区别于世界上任何一个国家的径向流纯化装置,解决了径向流吸附器领域国际上的共性难题,该装置是我国高端制造装备的代表,能够提升我国空分设备的国际竞争力占领技术制高点,推进国内重大装备的创新发展。
2024年国内首台(套)80万吨/年丙烷脱氢(PDH)装置电机制动氢气膨胀机2024年1月11日,浙江省经信厅公布的2023年度首台(套)产品认定结果,其中杭州杭氧膨胀机公司自主研制的80万吨/年丙烷脱氢(PDH)装置电机制动氢气膨胀机获得了国内首台(套)的认定。
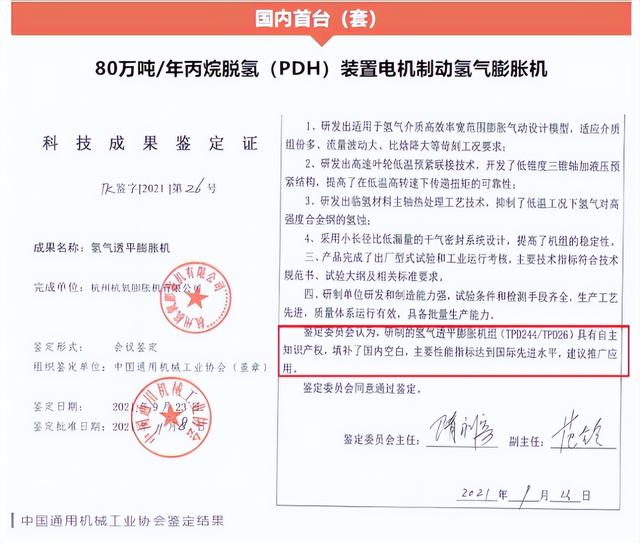
PDH氢气膨胀机组为大型丙烷脱氢装置必不可少的关键装备之一,机组能否成功运行,直接影响上百亿投资丙烷脱氢装置的经济性。在杭州杭氧膨胀机公司成功国产化之前一直被欧美国家技术垄断,直接影响着我国丙烯化工产业的安全发展。
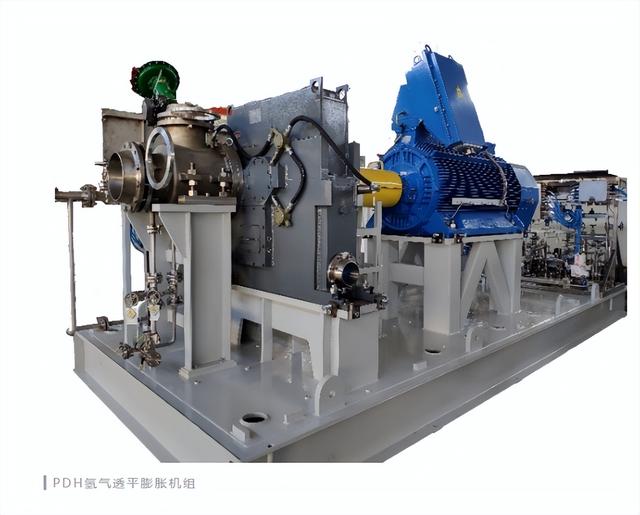
杭氧作为一家有着雄厚技术和制造实力的大型国有企业,有着打破国际高端装备垄断的责任与传统。杭州杭氧膨胀机有限公司作为杭氧集团全资专业膨胀机子公司,公司有着近60年深厚的技术积累,经过3年的调研和研发,于2021年自主研制的80万吨/年丙烷脱氢装置氢气透平膨胀机在东华能源宁波新材料一次开车成功,各项技术指标满足工艺要求。
在研制过程中获得了4项授权发明专利,5项实用新型专利,主持起草了氢气膨胀机行业标准1项,经过中通协专家鉴定各项关键技术指标达到国际先进水平。
2020年国内首台超大型乙烷脱氢制整装乙烯冷箱2020年7月2日,由杭州制氧机集团股份有限公司(以下简称杭氧集团)研制的国内首台超大型乙烷脱氢制整装乙烯冷箱完成研制,起航发往连云港石化有限公司项目基地。
乙烯冷箱是用于将乙烯从原料混合气中分离出来,是乙烯生产中的关键工艺设备之一。此次启运的乙烯冷箱包含31个核心设备,设备长8.7米,宽7米,高近34米,总重达592吨,是目前国内单台重量最大的乙烯整装冷箱。

在研制过程中,杭氧集团克服了系统结构复杂、项目工期紧张等一系列困难,将原本需要5台冷箱集成为1台冷箱,性能提升15%,为用户节约投资20%以上。一方面,整装冷箱由于高度集成,各核心设备之间密度高配管的布置难度大幅增加,技术团队经过对配管应力进行反复计算和布置方案的反复优化调整,保障了高密度配管的可靠性。另一方面,由于新冠肺炎疫情影响,使得项目工期十分紧张,制造团队通过制订周密的生产组织方案,采用模块化、多工位同步组装等创新协同作业方式,仅仅只用了两个月时间就完成了这个庞然大物的制造。
该乙烯冷箱的及时发运,将会为连云港石化联合装置工程及原料加工装置工程建设的顺利推进作出重要贡献,同时也标志着我国在大型乙烯冷箱的设计、制造水平上又迈出了坚实的一步。
2018年国内单体规模最大83000m³/h空分整体冷箱完成制造浙江石油化工有限公司4000万吨/年炼化一体化项目位于舟山市岱山县鱼山岛舟山绿色石化基地,规划面积约41平方公里。舟山绿色石化基地是“十三五”期间,国家发改委重点规划发展七大石化产业基地之一。该项目是基地的龙头项目,项目的建设将有利于提高我国石化产业基地的规模化和集中度,促进相关加工产业的优化升级,对提高我国芳烃、PTA-PET产业的竞争力和保障产业安全,增强石化行业的整体竞争力和可持续发展有重大意义。
浙江石油化工有限公司4000万吨/年炼化一体化项目一期炼化一体化项目规模为2000万吨/年炼油、400万吨/年PX及百万吨乙烯项目;二期为2000万吨/年炼油、480万吨/年PX及120万吨/年乙烯。一期项目计划于2018年8月份投产,配套空分设备计划于2016年7月前完成招标,2018年6月实现汽轮机冲撞。
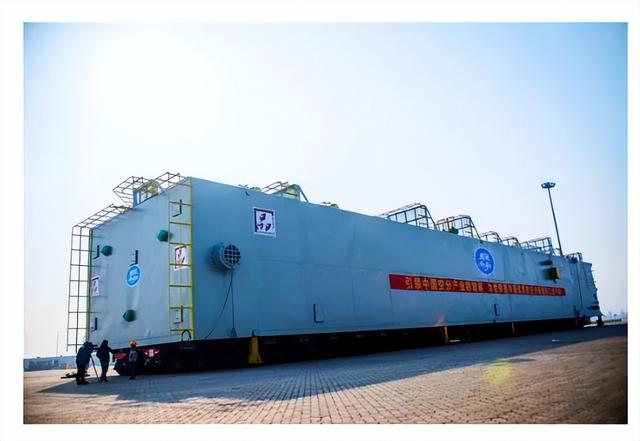
浙江石化四套83000m³/h空分设备是杭氧继神华宁煤六套100000m³/h空分装置合同以来的又一重大合同订单。该项目从2016年初便引来国内外各大厂商的关注,德国、法国和美国的世界空分设备知名企业纷纷派出精兵强将争夺该项目。杭氧在第一时间获取项目信息后,公司上下高度重视,多次组织召开专题会议,讨论投标技术方案。最终杭氧依靠自身先进的技术水平和优质服务,获得了浙石化四套83000m³/h空分装置的设计、供货和服务合同。
2017年2月16日,杭氧与浙江石油化工有限公司4000万吨/年炼化一体化项目一期工程四套83000m³/h空分设备合同正式签约,合同金额近9亿元人民币。
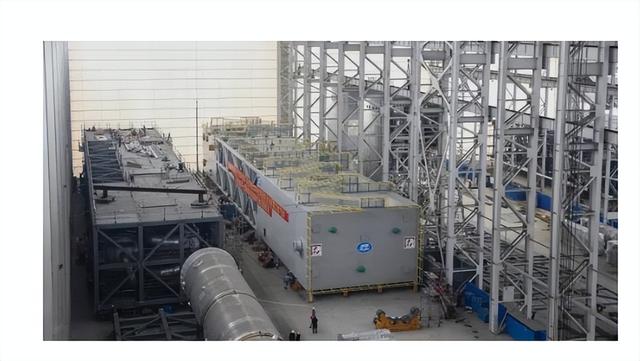
2018年1月31日,由杭氧集团运用“品字标浙江制造”标准制造的浙江石化四套83000m³/h空分设备首台重达950吨、国内单体规模最大的整体冷箱完成制造,开始发运。
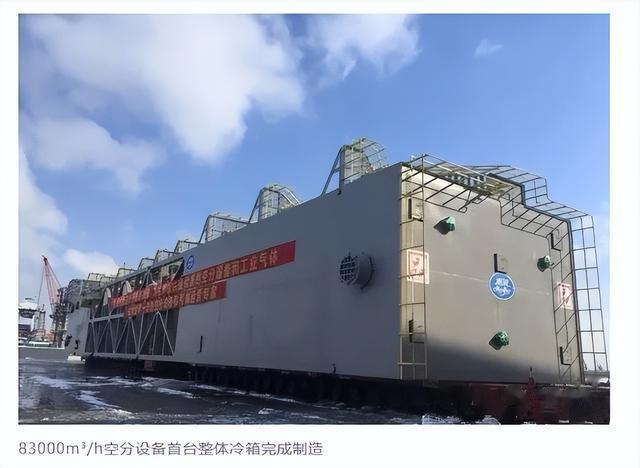
2018年6月5日,杭氧股份为浙江石化炼化一体化项目设计、制造的国内最大四套83000m³/h空分设备的最后一套空分冷箱完成吊装,标志着四套空分冷箱已全部吊装就位。
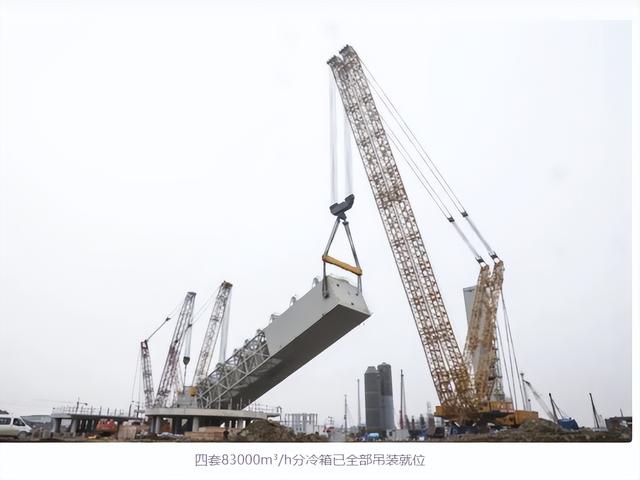
每台整装冷箱重达950吨、长近70米,相当于体积相当于三个标准游泳池。要研制完成这样的特大型整装冷箱的空分设备,自然对设计、生产、运输等环节也提出了更高要求。
整装冷箱卧式安装完成后,需要翻转90度,把设备立起来。近70米的整装冷箱每个部位重量都不一样,如何在吊装过程中,确保设备不受挤压,不会破损,精确的计算是关键。
相比传统现场立式安装,整装冷箱是卧式吊装变位安装,工序增加,工况复杂,制造难度加大。这要求支撑设备的每一个支架都要做到与设备“严丝合缝”,一毫米的误差都不能有。杭氧以浙江制造标准为要求,严格实施精品工程,一台空分整装设备有3445道焊口,通过综合焊接方式,确保焊接的不变形,一次焊接合格率达到99.5%以上。
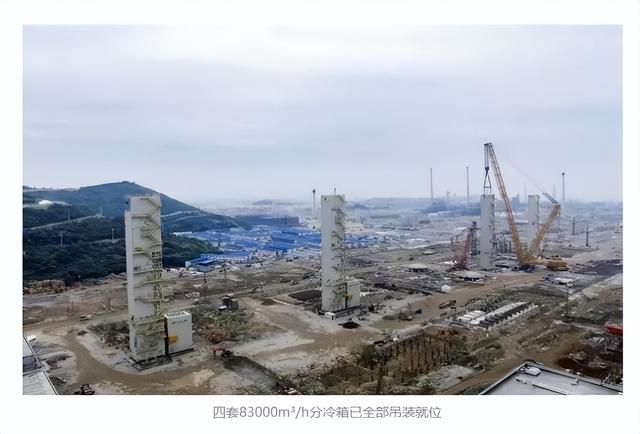
相对于传统的现场组装模式,工厂内整装制造能够有效避免现场组装场地和施工技术的局限,更好地保证设备生产质量,大幅缩短现场安装时间,预计能够缩短项目时间三个月。
2020年4000万吨/年炼化一体化项目二期4套105000Nm^3/h空分装置2019年新年伊始,杭氧凭借在浙石化一期4套83000Nm^3/h空分项目中表现出来的强大研发、制造和服务能力,与浙江石油化工有限公司再度携手,一举中标4000万吨/年炼化一体化项目二期4套105000Nm^3/h空分装置供货合同。
2020年4月,由杭氧研制的4套8万等级整装空分设备稳定运行,顺利完成考核验收,各项技术指标满足合同要求,能耗指标达到世界领先水平。而浙石化十万等级整装空分设备的等级、先进性、稳定性要求比之前研制成功的八万等级更高。

105000Nm^3/h空分装置整装冷箱
整装冷箱卧式安装完成后,需要翻转90度矗立,工艺要求十分复杂而精确。杭氧进一步优化设计方案,全面考虑起吊、运输、安全、能耗等因素,采用了更加高效的核心部机,实行高标准、高要求的“浙江制造”标准精益生产,对容易变形的起吊点进行计算、监控、检测,支撑设备的每一个支架与设备“严丝合缝”,近4000道焊口通过综合焊接方式,确保焊接的不变形,一次焊接合格率达到99.5%以上,把这一项目打造成高质量、高水准的精品工程。
杭氧为浙石化二期配套特大型整装空分设备

2022年4月26日,位于舟山鱼山岛的浙石化二期四套105000Nm^3/h空分设备先后开车成功,开始源源不断为浙江石油化工有限公司4000万吨/年炼化一体化项目提供所需的气体。这既是该世界级大型综合石化产业项目的一个重要节点,也是“杭州制造”在十万等级整装空分设备上获得又一次新突破。
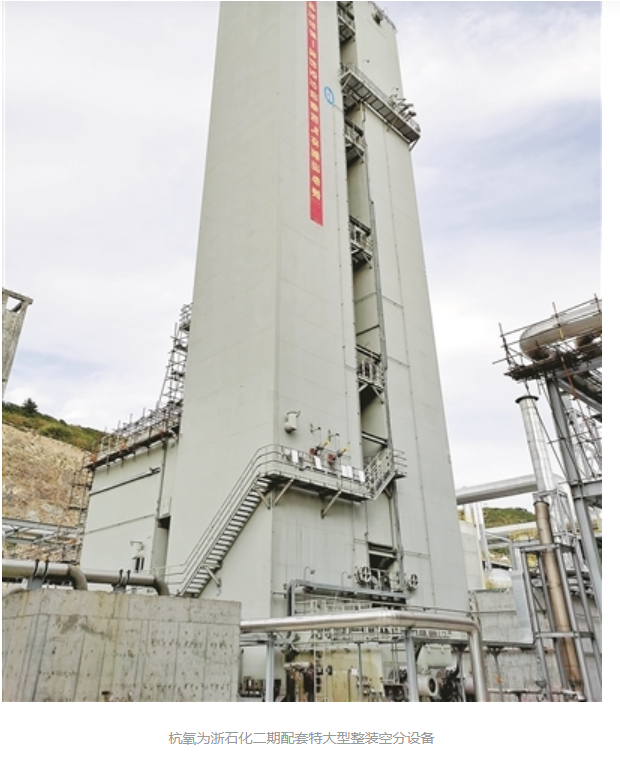
随着空分设备向大型化和节能化方向发展,高压铝制的板翅式换热器的应用越来越广泛。而大型空分设备配套的高压铝制板式目前全世界只有美国、法国的两家公司可以生产,国内空分成套一直依赖进口。
历史性突破-13.5MPa的超高压板翅式换热器为加速空分配套关键设备国产化进程,打破国外企业的技术垄断和市场垄断,填补国内空白,提高我国板翅式换热器的研制水平,杭氧在2013年初把全面掌握8~10MPa高压铝制板翅式换热器设计制造技术提升为公司发展战略,并成立空分高压板式换热器攻关小组,由公司总工程师任组长,加大人力、科研和技改力度,统筹安排,合理利用有效资源,做好工艺保障和质量保证,并利用研究所和气体公司两大平台,进行基础和机理研究,深入开展技术攻关。同时,利用高精高速冲床,自主开发了翅片的冲压模具,在模具开发的基础上成功研制了高密度高压翅片和低阻高效波纹型翅片,还进行了高压翅片的爆破试验,为实现高压铝制板翅式换热器国产化奠定了坚实的基础。
2014年,国产首台最高设计压力为8.1MPa的高压铝制板翅式换热器通过压力试验,之后又成功应用于神华宁煤空分设备中。为了进一步推进大型空分关键部机国产化进程,杭氧又展开了10MPa及以上等级高压板翅式换热器产品潜心研制。
在长达近两年多时间的研制过程中,杭氧股份技术创新团队进行了大量的科研试验,有效开展了国际合作和产学研结合,充分运用了国际合作单位——德国多特蒙德大学的失效分析结论和成果,在材料控制技术、模具成型技术、高压翅片及高效低阻波纹型翅片研制技术、清洗工艺、部装工艺和真空钎焊等工艺和技术上实现了创新和突破,并取得了多项发明专利。
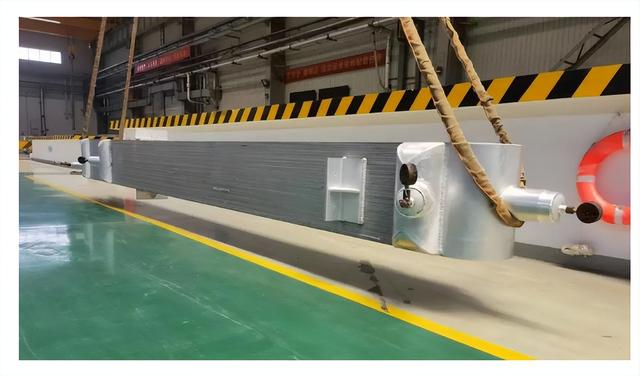
2017年杭氧板式厂完成了武石化高低压一体换热器研制任务,该换热器的结构7500mm×1300mm×2840mm,单重达32吨,最高设计压力5.9MPa。是当时杭氧板翅式换热器单体最大的高压换热器
武石化高低压一体换热器2022年4月,在世界权威检验机构英国劳氏质量认证(LRQA)的现场见证下,杭氧板式换热器有限公司设计压力为13.5MPa的超高压板翅式换热器产品完成了最终压力试验,水压试验压力达17.55MPa,达到了目前世界上该类产品最高设计压力等级(13.5MPa),取得了历史性的突破。
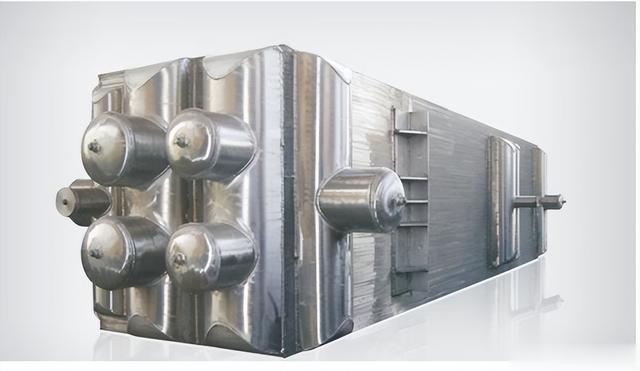
该产品芯体由设计压力0.55MPa的空气层通道和设计压力高达13.5MPa、最大静水压17.55MPa的液氮层通道组成。在近两年的研制过程中,该公司技术创新团队进行了大量的科研试验,强化产学研结合,在材料控制技术等方面实现了创新和突破,并取得了多项发明专利。

杭氧突破了设计、制造工艺、质量等8个技术难题,在打破高压板翅式换热器依赖进口的局面后,继续将该类产品性能推向新的高度。杭氧在短时间内完成了该类产品10MPa、12.8MPa、13.5MPa的“三级跳”, 从追赶者变为领先者。其中,12.8MPa等级产品在2021年荣获中国机械工业科技进步奖一等奖。
**********************
赞盛世中华繁荣富强
向装备制造工作者致敬,
为化工行业建设者加油
**********************
本系列和大家分享最近十年来化工装备行业取得的成就
图文来源网络资讯收集整理,对资讯发布者表示感谢,如有侵权秒删
感兴趣的朋友可以看系列合集,欢迎讨论