前言
极耳对齐精度问题是卷绕电芯质量控制体系下一个重要的问题。为了优化卷绕工艺控制闭环及提升电池性能,我们做了许多尝试与努力,针对电芯多极耳对齐精度问题,提出了建立极耳位置模型和采用边缘闭环控制算法,实现对齐精度的有效控制。模型通过检测、矫正参数,提供理论数据,并通过仿真验证其对改善极耳位置的适应性,此方法对优化卷绕质量、提升电池性能有重要意义。
动力电池智能卷绕技术

摘 要:在卷绕电芯质量的把控中,极耳对齐精度是一个极为复杂的影响因素,涉及多个工序的质量。为了解决电芯多极耳对齐精度差的问题,本文通过建立极耳位置模型,采用边缘闭环控制算法,对影响对齐精度的各项参数进行检测、矫正和控制闭环,为现有控制技术提供理论参考数据,实现极耳对齐精度的有效控制。同时极耳位置模型可反映各项参数对极耳位置的影响方式以及极耳错位的表现方式,以便于研发人员理解各项参数对极耳错位的影响程度以及修正极耳错位的方式,并将其表现在控制方法中。仿真分析与实际控制工况的结合结果表明,所采取的控制方法对改善极耳位置有着较高的适应性,且模型也能准确反映出极耳位置的变化趋势。此外,本文进一步探讨了实现智能券绕整体闭环的逻辑方法,进而优化整个卷绕工艺中的控制闭环,对最终实现卷绕工艺的质量闭环,提高电池性能质量以及生产效率的目标,有着重大的参考意义。


动力电池的生产对技术要求较高,对装备依赖性较强,因此目前动力电池产业的发展仍受到生产装备的制约。在关键的工艺环节中,尤其是卷绕成型阶段,张力的控制精度、纠偏对齐以及极耳错位等都将直接影响电芯质量;同时,当前卷绕设备的正常运行仍需要人工的干预,导致动力电池生产的整体效率下降,一致性较低,是导致生产浪费和质量下降的重要因素[1]。
极耳对齐精度作为电芯制作的难点之一,其主要的影响因素来源于材料的厚度问题。在卷绕工艺的要求中,电芯的尺寸和极耳位置等都是确定的:并且需要使用特定周长的卷针进行卷绕。而随着卷绕圈数的增加,极耳的数量在增加,累计的位置误差也在增大。在各项参数影响不变且卷绕50圈的情况下,卷绕材料整体的平均厚度偏差达到1μm时,电芯第一圈与最后一圈的极耳错位将超过7mm,且随圈数的增加,极耳错位量也会进一步增大。
在卷绕工艺前,模切工艺会根据设定的极耳间距值对极耳进行模切处理,业内对于解决极耳错位问题已有一些方向,即通过优化极耳间距的计算来优化模切工艺参数,可想而知,解决极耳错位问题的关键在于模切工艺段极耳间距的模切参数定义。目前已有的方案中,韦磊等[2]提出了在卷绕工艺中使用未模切的原极片,然后在成型电芯上通过人工裁切获得理想的极耳位置分布,最后通过拆解、测量的方式获得极耳间距数据;张国帅等[3]通过在电芯刨面预设极耳位置,再对刨面图上的极耳位置进行测量获得极耳间距数据;花宇等[4]通过对电芯的形态和工艺参数进行分类,在确定影响因子的基础上假定一种基准形态,再进行算法探究,进而给出了电芯形态和极耳序列号判别式,并结合基准形态的算法形成最终的通用算法。前2种方案依赖于实验样品,在工艺变更后需要重新制作理想模型,存在局限性。这些是在模切工序段通过优化极耳间距的方式来解决极耳错位的方法。
在卷绕工序段,业内也有通过实时改变卷针角度或者在卷绕过程中向材料层中加入介质的方式来达到纠正极耳错位的目的。但均会一定程度地影响工艺、电芯质量和生产效率。本文的研究将通过建立模型仿真并结合实际控制的方式,在卷绕工艺段,根据现有的调节方式,定量分析各影响参数,优化控制体系,实现对极耳位置的有效控制。此外,本文还倡导全流程产品质量信息的流通,利用智能卷绕技术,从生产全流程的角度解决电芯生产的质量问题。
1 动力电池制造技术
动力电池生产工序大体上可以分为3个阶段:前段工序(电极制作)、中段工序(电芯合成)和后段工序(化成封装),如图1所示。在中段工序中,卷绕成型是目前电芯成型的主要工艺,适用于圆柱形电池和方形电池的制造。
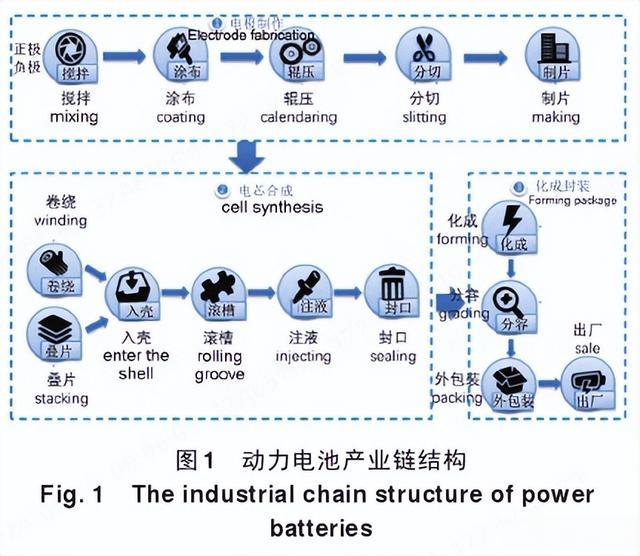
1.1 卷绕制造技术
1.1.1 卷绕工艺
卷绕工艺是利用固定卷针通过转动的方式,将正负极极片和隔膜按一定的顺序绕制成圆柱型,或者绕成环形冷压成带圆弧的方型电芯,并以收尾贴胶的方式固定电芯结构。
在该过程中涉及对极耳对齐、张力控制以及纠偏对齐等决定产品质量的关键问题的处理。虽然目前卷绕技术是电芯成型工序中最成熟的,但在电芯极片隔膜对齐度、极耳对齐度、极片贴合的一致性等质量因数以及生产效率上仍然有较大的提升空间。另外,卷绕工艺中的参数设定,如极片尺寸、卷绕圈数以及卷针长度等都是根据电池的容量设计来确定的,因此卷绕设备会根据不同的电芯工艺以及设计要求做出不同的改变。
1.1.2 卷绕质量的要求
在卷绕的不同阶段对于质量的要求不同:在卷绕前,通常对设备、组件的安装精度和料线质量有要求,具体包括辊组件的加工精度、辊组件间的平行度和极片厚度、波浪边、蛇形弯以及极耳不良品等;卷绕过程中,对张力控制、切断毛刺长度以及机器运动精度等有具体要求,其中,恒张力控制是保证电芯界面平整、层间贴合均匀的关键;卷绕完成后,极片、隔膜对齐度、极耳对齐度以及卷芯尺寸等是卷绕质量的关键要求[5]。
极耳影响着动力电池的安全性,其对齐度是判断电芯合格的重要标准之一。极耳错位会导致电芯极耳焊接不牢固、不均匀,影响电池的电性能和安全性能;另外,极耳错位过大会导致正负极极耳间距缩小,造成电池短路,并且焊接时的火花与金属飞溅,也会增大短路的风险。
因此,在卷绕工艺和卷绕设备上的共同突破,将促进卷绕技术的发展以更好地解决极耳错位带来的安全隐患,再通过基于模型的数字化以及大数据的智能化,进一步实现动力电池的智能卷绕技术。
1.2 智能制造技术
智能制造的本质是利用数据化解制造过程的不确定性,从而实现最佳的制造价值,其方法是准确获取数据,通过运用人工智能、大数据和物联网等先进技术,实现对制造过程自动化和智能化的管控,以提高制造效率和产品质量。
随着市场和消费者对产品质量、个性化和交付周期等需求的提升,传统的工业生产方式已经开始发生根本性的变革;在新兴技术的快速发展以及日益激烈的全球经济竞争中,智能制造将成为制造业不断提高生产效率,降低生产成本,在市场竞争中取得优势的关键路径。
2 卷绕技术中的控制难点
在电芯成型工艺中,卷绕技术经历了长时间的迭代,其中最突出的改变就是“卷圆成方”,即用圆形卷针卷绕出方型电池,再进行冷压成型,最终得到带圆角的方型电芯,实现了对方型卷针的替代。
虽然卷绕技术的发展极大地提升了卷绕电芯的质量,但是在追求动力电池高质量发展的道路上仍然有着众多需要解决的控制难点,主要体现在极耳对齐、张力控制以及纠偏对齐等方面,产生这些问题的主要原因涉及材料的质量、频繁的加减速、卷绕前工序的影响以及设备本身的质量等。在此,以我司 250 自动卷绕机(图 2)的具体控制要求为例,展示目前在各控制难点的数值要求。
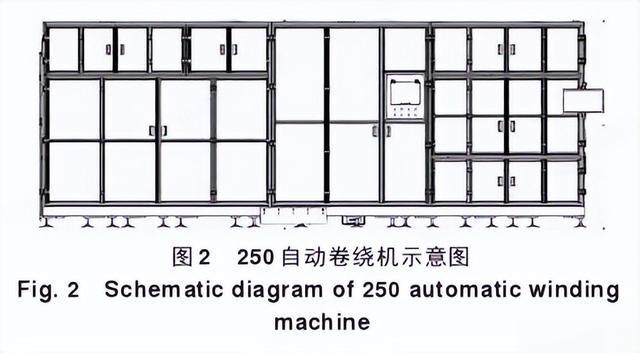
2.1 极耳对齐度
极耳对齐指的是电芯上每层正负极极耳的位置在叠层方向上都分别在要求的范围内,是一种范围对齐。由于锂电生产过程中既离散又连续的特性——离散是因为其每段工序的设备、标准和质量都来自不同的企业,而连续则是每个工序之间的生产质量都相互影响,因此,卷绕前每段工序出现的极耳错位因素相互叠加,造成了极耳错位发生的随机性,其中导致极耳错位的原因主要归咎于极片厚度的差异,还包括极耳间距、卷针直径以及卷绕参数等来自不同工序段的影响因素。
在 250 自动卷绕机中,极耳对齐的要求为±7 mm,电芯卷绕圈数为 50 圈。然而在标准条件下,电芯平均每层的厚度偏差达到 1 μm 时,第50 圈的极耳偏差将超过 8 mm。总的来说,针对极耳错位的问题需要从卷绕前的每段工序中做到严格的质量把控,否则,当所有的质量问题都累积到电芯卷绕成型段时,只在卷绕段进行调控的效果是有限的。
2.2 张力控制
在250自动卷绕机的整个卷绕过程中,隔膜张力控制要求在 100~750 gf(1 gf=9.8×10-3 N),极片张力设定范围在 100~2000 gf,匀速运行时极片和隔膜的张力波动范围均在规定标准值的±5%,同时实时显示张力值与传感器值偏差在 5% 以内。理论上料线张力越小,波动越小,则电芯质量越高,目前在实际工序要求中的张力范围也是按照这个要求控制的。
2.3 料线对齐
电芯生产工艺中明确有料线边缘对齐度的要求范围,这使得卷绕设备上每条料线都至少安装有1组纠偏组件,极片段甚至有 3~4 组,目的就是纠正跑偏的料线。料线跑偏的主要原因是其在辊上运动时横向受力存在差异,具体表现为辊组件间的平行度以及极片横向的厚度差异等问题。对齐度在250 自动卷绕机的要求中明确了负极-正极、负极-隔膜以及隔膜-隔膜之间的偏差范围,具体数值均要求在±0.5 mm。
3 极耳错位的理论分析
从涂布、辊压工序段的极片厚度,到激光膜切段的极耳间距,再到卷绕成型段的精度误差和层间距问题,都是影响极耳对齐的重要因素。这种来自多工序质量问题的叠加影响,若只在卷绕段进行极耳质量调控是很难做到高质量生产的。由于卷绕阶段是电芯产品的产出阶段,也就是直观地显现出极耳错位问题的阶段,因此很容易造成是由卷绕设备问题导致极耳错位的误解。事实上,在卷绕前料线厚度以及极耳间距就已经成型,也就是质量问题以及错位风险在卷绕前就已经存在,并与卷绕段的误差共同影响极耳位置。因此,在卷绕段进行调控只能解决卷绕段产生的误差以及在一定程度上缓解前段工艺质量的影响,而真正解决极耳错位问题应该在制片段就开始进行全流程的质量把控。
3.1 影响因素
3.1.1 工艺流程分析
从工艺流程上来看:制片阶段产生的厚度问题主要表现在厚度不均匀、厚度超差以及料线边缘问题等,使得在卷绕过程中每层卷绕半径不规则变化,进而影响到极耳位置以及收放卷速度匹配,造成极耳错位和张力问题。
模切阶段是参考料线标准厚度以及卷绕参数等完成的工艺设计,即极耳间距需要裁切的距离是按照标准厚度计算得出的,每个极耳间距都与一个标准厚度相对应。然而,模切阶段本身存在一定的裁切精度问题,再加上来自制片阶段的厚度问题影响,使得极耳间距与实际厚度之间产生随机性的变化,导致卷绕过程中极耳位置的随机分布。
卷绕阶段是电芯的成型阶段,在此之前,所有正负极与隔膜都是由不同设备分开加工、处理,并随机搭配正负极卷料和隔膜卷料进行电芯卷绕,这使得该阶段存在一个材料整合的过程,也就是极组厚度的均匀性将取决于选取的这4捆卷料的厚度情况。另一方面,卷绕设备自身的精度问题以及卷绕参数中速度、加速度和张力的设定值也会影响极耳位置,尤其是卷针直径。
来自多个阶段的影响因素(图 3)导致极耳位置的把控需要在各个阶段做到严格的或者有预见性的质量监管,即在离散的生产工序中,通过信息流的方式建立生产信息、质量信息等的交互平台。产品信息跟随产品物料一起流动,使得独立的生产工序在加工前就能大体了解待加工产品的状态信息,并提前做出合适的工艺调整,加强各段工艺间的关联性。
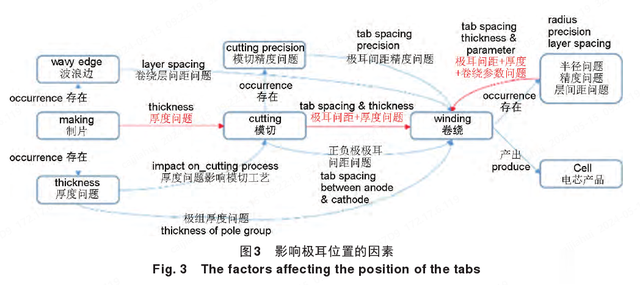
3.1.2 基础影响因素分析
从各个工序阶段大体上可以总结出3类影响因素,极组厚度、极耳间距以及卷绕精度,其中厚度是主要的影响因素,不仅包括极组厚度,还涉及卷针直径误差以及卷绕层间距问题。
(1)极组厚度
极组厚度是正负极极片厚度以及相邻两层隔膜厚度的总和,具体影响方式表现在负极-负极间的极组厚度影响下一层负极极耳的位置,如图4中的A 所示;正极亦然,如图 4 中的 B 所示。极组厚度的异常会引起下一圈的周长变化,而按照标准厚度裁切好的极耳间距与该变化的周长之间存在差异,最终导致该层的极耳错位并继续影响下一层的极耳位置。

值得注意的是A与B虽然同为极组厚度,但是其中的料线组合略有差异,即构成极组厚度的料线来自不同的卷绕层;同时,根据包覆顺序可以观察到,第一层正极的厚度异常会影响第一层的负极,而负极的厚度异常却不会影响到正极。
根据这2个特性可以得出3个结论:
①正负极极组厚度存在微小差异,当料线局部厚度差异较小时,两者基本一致。
②料线或极组厚度异常会产生叠加影响,持续影响后续每层的极耳位置。
③卷绕过程中,压花辊调试极耳位置的原理是通过改变正极料线的厚度,调整极组厚度以改变极耳位置,然而改变正极厚度对同层的负极造成的影响相同,因此压花辊调试对于正负极极耳的位置影响程度一致,这也是卷绕工序中存在调试限制的原因之一。
(2)极耳间距
极耳间距指的是两相邻极耳间的距离,可分为两相邻极耳内侧的距离或两相邻极耳间的距离,如图5所示。其影响主要体现在2个方面。
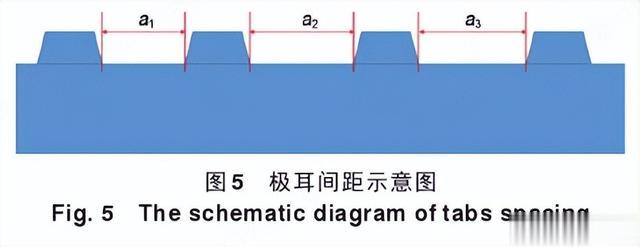
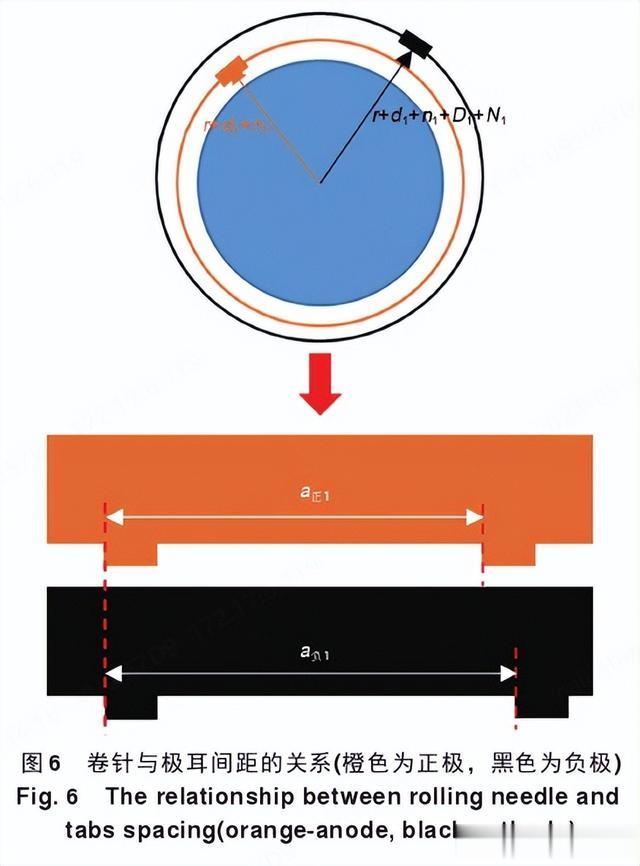
①第一层极耳间距与卷针周长的对应关系卷绕电芯前两个极耳对齐取决于第一个极耳间距与卷针直径之间的对应关系,如图6所示,关系式为:

式中,a正/负1表示第一层正负极极耳同侧的间距;r、d1、n1、D1、N1分别表示卷针半径、第一层负极极片、(下)隔膜、正极极片和(上)隔膜的厚度。
根据电芯工艺要求,在卷绕段和激光模切段都会分别设定好卷针周长以及极耳间距的工艺参数,然而机台本身的精度问题、工序的离散性以及产品信息传递限制等都会使得卷针周长与极耳间距的对应关系无法达到电芯工艺标准,从而引起极耳错位。也再一次说明机台间的信息传递以及工序间参数对应的重要性,在前一段工序出现问题时,下一段工序可以通过及时调整,达到提高产品生产质量的目的。
②相邻极耳间距的差值与极组厚度的对应关系根据卷针半径与极耳间距的对应关系式可以得出,每一个极耳间距都有对应的卷绕半径(卷针半径加上当前所有的极组厚度),如图 7 所示,关系式有:
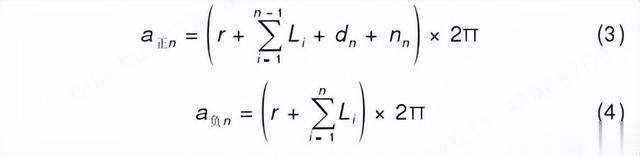
其 中 , L 表 示 极 组 厚 度 , 即 L1= d1+ n1+D1+ N1。
从两相邻极耳间距的差值中可以得出,其与极组厚度的关系如下:

因此,在极组厚度理想的状态下,卷绕电芯中每个极耳间距呈现等差的递增趋势,即该层极耳间距与上层极耳间距的差值与该层新增的极组厚度呈对应关系。
(3)卷绕精度
卷绕精度的影响体现在多个方面,包括机械精度、控制精度、参数设定以及卷针半径,其中主要的影响来自参数设定和卷针半径。图8所示为卷针直径。
参数设定指的是卷绕时的速度、加速度和张力的设定数值以及精准把控,这直接影响到卷绕的层间距,相当于从另一个方面造成了极组厚度的异常;卷针是整个卷绕过程的基础支撑,它的尺寸不仅直接影响电芯的尺寸,还影响电芯内部的极耳位置分布。
卷绕参数与卷针半径对极耳间距的影响从公式中分别表达为:

根据公式表示,卷针半径对每一层极耳的影响都是一个定值。因此,它与厚度影响的不同之处在于,其对于每一圈的极耳位置影响程度相同,而厚度的影响会产生叠加效应。在实际情况下,极耳位置通常也是由多种因素共同影响的。


3.2 极耳错位的方式
根据极耳位置影响因素的数量和类型,大致可以将极耳错位方式分为3类(图9中为电芯的截面示意图,橙线和蓝线代表每层正负极极耳两侧的对齐状态)。

(1)单一因素影响,即只有卷针半径或者厚度的影响卷绕电芯若只受到卷绕半径影响时,其极耳位置呈现等差的直线偏移,如图10所示,第n层极耳偏移量为:

其中,∆r为卷针半径的偏差量,每层极耳位置都相对于上层偏移2π∆r的距离。
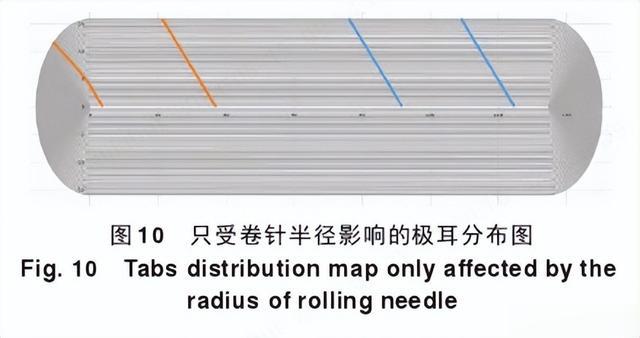
假设卷绕圈数为 50 圈,要求极耳错位量不大于7 mm,则卷针半径偏差不能超过0.022 mm。
卷绕电芯若只受到厚度影响时,其极耳位置呈现等比的弧线偏移,如图11所示,第n层极耳偏移量为:

其中,∆d为每层厚度的平均偏差量,第n层相对于n-1层偏移2πΔd × n的距离。假设卷绕圈数为 50 圈,要求极耳错位量不大于 7 mm,则平均厚度偏差不能超过 0.87 μm(此处的厚度包括极组厚度以及卷绕层间距)。
(2)共同影响,即卷针半径与厚度同时影响
卷绕电芯若同时受到卷绕半径和厚度影响,其极耳位置呈现 U 形偏移,如图 12 所示,此时卷绕半径与厚度对极耳位置的影响程度相反(影响程度相同时偏移量更大,在此不考虑),第n层极耳偏移量为:

这也是在卷绕过程中,通过调试卷针半径来缓解极耳错位的原理,即由于厚度异常导致大幅度极耳错位时,可通过调试卷针半径的方式来降低极耳错位的程度。
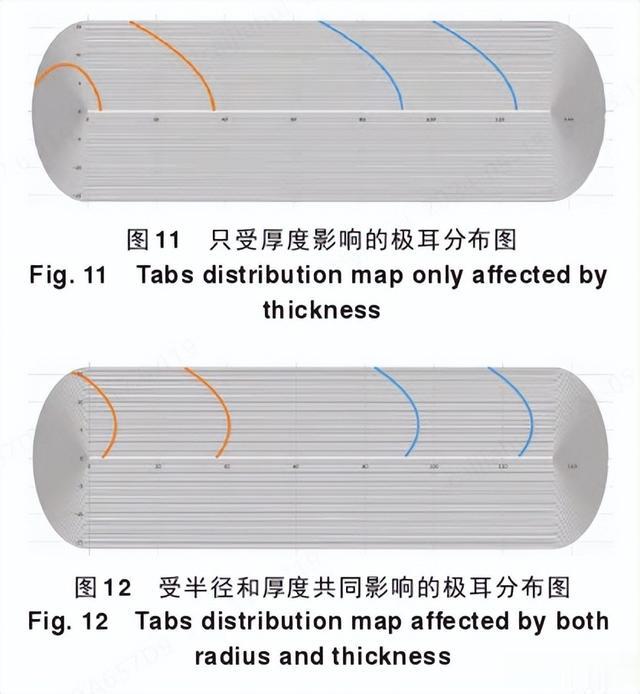
假设条件相同,卷绕圈数为 50 圈,要求极耳错位量不大于 7 mm,此时的平均厚度偏差不能超过3.5 μm,相比之前的0.87 μm,对料线厚度质量有着更强的适应性。
(3)异向影响,即正负极极耳错位的方式不同由前文的分析大体可以得出,正常工艺情况下正负极极耳的偏移方向和程度基本相同,这是由于厚度和卷针半径对正负极的极耳影响程度一致,然而,在实际生产中仍有正负极偏移不同的情况,其中常见的是“八字”偏移,如图13所示。
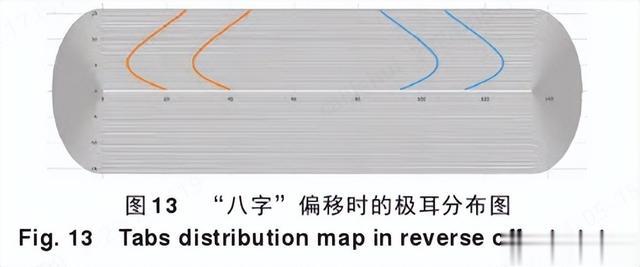
该种偏移的特点在于正负极极耳的偏移方向或程度不同,由于在卷绕过程中的调试对正负极的影响程度一致,因此在卷绕过程中无法对此种偏移做出有效的极耳位置调控。引起“八字”偏移的原因主要是正负极料线的模切工艺不同(正负极极耳间距差异过大)或者在料线横向上的厚度分布不均(正负极极耳处的局部厚度差异过大)。
3.3 解决方案
影响极耳错位的因素来自电芯生产的多个工序,从工艺的角度出发,在卷绕前料线的厚度以及极耳间距已经加工好,只在卷绕过程中进行检测和调控十分困难并且效果受限;从影响因素的角度分析,极耳间距与众多因素之间存在强相关性;从设计和制造的角度来讲,模切阶段是根据卷绕工艺进行计算后对极耳位置进行设计的阶段,而卷绕只是将模切段设计好的料卷按照正常的卷绕工艺将其卷成卷芯,前者是产品的设计阶段,后者是产品的制造阶段,质量是设计出来的。
因此,在全流程对极耳位置质量把控的基础上,解决极耳错位的重心应该在模切阶段。然而要想在模切阶段能对极耳位置做到高质量的设计,首先就是需要实现对料线厚度的测量,这是解决极耳错位的基础,更是实现高质量极耳位置设计的必要条件。在能实现亚微米级的实时厚度测量之后,模切段就能根据料线厚度的变化对极耳间距做出相应的调整;同时建立工序间、设备间的联系,使设备在加工前就能了解待加工产品的质量信息并调整工艺参数,实现关键生产信息的快速流通,促进智能制造技术的发展。
然而,激光切卷绕一体机与激光膜切、卷绕分体机间极耳错位的解决方式也不同,由于一体机实现了在一台设备上结合激光切与卷绕2道工序,相当于建立起了2道工序间的信息流通,因此,一体机的极耳对齐度将比分体机更加容易控制。
3.3.1 激光切卷绕一体机
拥有有效的测厚技术后,在一体机上实现闭环控制相对就更加容易。只需要通过动态检测极片的厚度,再通过算法计算出需要裁切的极耳间距,最后进行动态的切割调整即可;同时,还可以根据卷绕电芯的质量情况做出相应的裁切调整,再通过数字化积累实现极耳对齐的高质量调控。
3.3.2 激光模切、卷绕分体机
在分体机中通过电芯产品的质量反馈来改善极耳间距的裁切参数是不可靠的,因此,需要在激光模切段就对极耳位置做好最佳的设计规划。具体的实现方式是在卷绕前对正负极以及隔膜卷料做好标识,其目的是保证同一标识的卷料将会一同被送入卷绕工序中并卷绕成同一电芯,即在激光模切段对有同一标识的卷料进行针对性加工(整个正负极与隔膜卷料中的每片电芯一一对应,不合格片不计),根据综合的极组厚度情况进行极耳位置的针对性切割,做到最优的极耳位置设计。
在这个过程中,为了提高卷绕效率并减少停机时间,需要保证正负极卷料的有效片数相同,实时检测不合格的片数并排除在计数之外,这样能保证换料的同步进行,减少不必要的停机时间。
3.4 模型仿真运用案例
在工艺质量学习闭环中,数据的整理收集以及模型的优化选择是实现整体制造过程大数据闭环的方式。
以极耳错位模型为例:
①模型只考虑了极组厚度以及卷针半径的影响;
②电芯卷绕圈数为50圈;
③所有的偏差均以标准厚度为基础。
3.4.1 料线尺寸偏差计算
标准料线尺寸如表1所示,正负极极片的误差要求在±3 μm,隔膜要求为±1 μm,根据不同的尺寸偏差要求,运用不同的计算方式对概率进行估算。
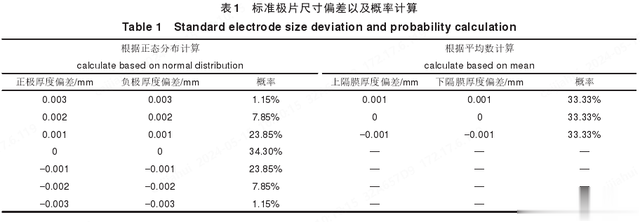
由于正负极极片误差在±3 μm,假设极片厚度符合正态分布情况,隔膜厚度以平均数方式简便计算,即可得出在标准要求下,料线厚度的偏差量以及概率情况。
3.4.2 卷径与极组极值的关系
根据不同的极组总体偏差情况,只通过变化卷径的方式调节,结果如表2所示,若极耳错位量要求在 7 mm 以内,极组总体偏差为±5 μm 时,可通过卷径调节完成合格生产,合格率估算为 99.6%;同理,若极耳错位量要求在6 mm以内,极组总体偏差为±4 μm 时,可通过卷径调节完成合格生产,合格率估算为97.95%。
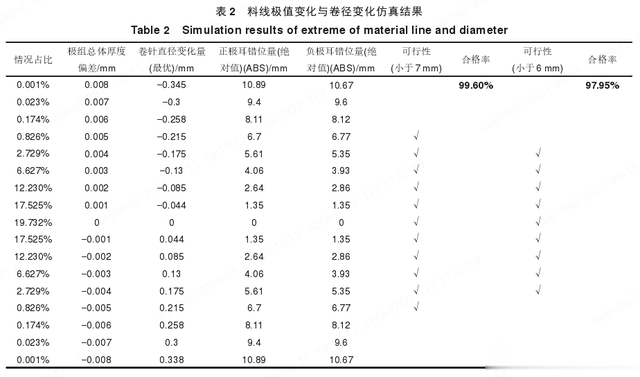
仿真过程中,在每组总体厚度偏差一定的情况下,调整卷针直径使得正负极极耳错位量最小,从而得到最优的卷针直径数值以及正负极极耳的错位量。
在只进行卷径调整的情况下且极耳错位偏差要求在7 mm以内时,若极组的总体偏差超过±5 μm,则无法只通过卷径变化完成极耳错位的调整;而随极组总体厚度偏差的极值化情况的加重,整体的生产合格率预测也将会大幅度下降。
3.4.3 压花与极组极值的关系
目前的压花是通过改变正极的厚度来完成极耳位置调节,因此,根据负极和上下隔膜的偏差,以及电芯极耳位置要求可以推算出正极厚度所需调节的厚度情况,如表3所示。
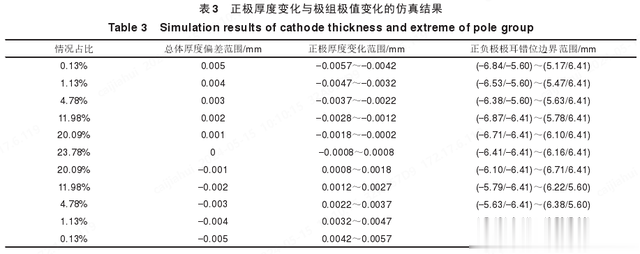
以表 3 第 1 行数据为例:当负极与上下隔膜的总体偏差达到 0.005 mm 时,正极厚度的偏差需要保持在-0.0057~-0.0042 mm之间,即正极厚度要比标准薄 4.2~5.7 μm,才能保证正负极极耳错位量在要求范围内。也就是在总体偏差达 5 μm 时,正极厚度偏差为-5.7 μm 和-4.2 μm 所对应的正负极 极 耳 错 位 量 分 别 为 -6.84mm、 -5.60mm 和5.17 mm、6.41 mm。
若需要满足所有偏差情况下极耳位置调整要求,正极厚度变化范围最少需要在-4.2~4.2 μm之间,这需要通过压花来实现,即通过测厚计算得出此时的厚度偏差情况,再根据正极的厚度进行压花调节。然而,正极厚度自身存在±3 μm 的误差情况,因此压花所带来的正极厚度变化只有超过14.4 μm 时,才可以应对所有的厚度偏差情况。
3.4.4 卷径、压花与极组极值
由于压花只能使极片变厚这一特性,使得卷绕段的调控受到一定的限制,因此在卷绕过程中,控制正极片在受到一定的压花压力后的厚度值与标准值接近,此时再通过控制增减压花的压力即可实现正极片变薄变厚的目的。
根据实际工况情况,料线整体厚度偏厚,且卷绕机压花可调厚度为 0.008 mm,因此正极片厚度越薄越有利于极耳位置对齐,即取正极偏差为-0.0042 mm进行仿真计算,如表4所示。

在整体偏厚的情况下,正极以最大负偏差进行仿真计算,通过调节卷针直径偏差,得到最优的正负极极耳偏差情况(两极耳偏差绝对值的差值最小)。因此,整体偏差为正值时,正极偏差值为-4.2 μm,整体偏差为负值时,根据压花压力调节的能力,正极偏差值为 3.8 μm。当偏差达到±9 μm 时(不包括正极),无法通过卷径变化和压花共同调节实现极耳位置的对齐。即在共同调节的情况下,可以适应更大的偏差范围,极组偏差达到±8 μm(不包括正极偏差)。然而,实现的基础在于有足够的压花厚度调节来调整正极的厚度情况,使得卷绕机能适应更大的料线偏差,因此,在符合质量以及工艺等要求的前提下,尽量增大压花的厚度调节范围,将提升对极耳错位的调节能力。
3.4.5 小 结
在理论仿真中,以客户现场的实际生产要求为例,极组偏差在±5 μm以内时,可以只通过卷径调节实现电芯的合格生产;同时,压花厚度调节能力能达到 14.4 μm 时,极组偏差达到±5 μm,也能实现只通过压花调节达到极耳对齐的要求。此外,2 种调试方式结合使用,可以在极组偏差达到±11 μm 的情况下,完成极耳对齐的生产要求。
在结合实际控制时,首先需要通过测厚计算来确定料线的厚度情况,再根据整体偏差值(不包括正极)以及正极厚度情况来判断卷针直径的调节数值,现阶段建议优先只通过卷径调整实现极耳对齐(由于目前压花存在影响料线质量的争议),在极组厚度偏差过大时,再通过改变压花压力实现辅助调节,从而实现极耳位置的有效调控。
但要实现真正意义上的对齐仍需要对料线质量以及极耳间距进行优化提升。实现真正意义上的高质量智能制造,即在发现料线质量问题时,就已经通过计算得出该层极耳的错位量,并在激光膜切时根据该段错位量调整极耳间距的切割参数。在卷绕前解决错位问题,实现问题的预处理和解决,卷绕时只需要通过检测料线质量变化和极耳的位置情况,做出适当的错位参数调整,进而实现极耳位置的精准把控。
4 智能卷绕技术
4.1 技术思路
智能制造技术的核心思想就是基于模型的数字化以及大数据的智能化。通过智能卷绕技术来解决极耳错位问题,首先需要的是建立卷绕电芯的极耳位置模型,在实际实验和虚拟模型中,通过相同的参数设定对比结果输出,优化极耳位置模型的系统结构,最终实现虚拟调试。
同时,依靠模型可以数字化以及优化积累的特征,实现数字化积累。在每一次优化调节的过程中,计算机对厚度数据与极耳位置数据关系的积累,将帮助获得关键控制点以及控制逻辑,为智能化提供有效的数据支撑。
智能化将在数据的支撑下,实现对异常厚度部分的预测性极耳间距加工以及自动的工艺参数变更,大大提升产线的生产效率以及合格率。此外,生产过程中,从数据采集、设备、生产现场以及运营管理等的信息状态和结果都将以数据的形式存储,并持续实现质量的闭环优化,提高电池制造的合格率、一致性和安全性。
4.2 质量闭环
质量闭环的层级架构可分为设备内部控制的实时闭环、工艺质量的学习闭环以及基于电芯产品性能的数据闭环,如图14所示。

卷绕设备内部的实时控制是实现质量闭环的基础,也是实现智能卷绕的基础。因此,首先需要解决卷绕设备本身的质量问题,包括定位精度、效率、一致性和稳定性等,这主要是通过传感器和逻辑控制等装备的底层控制方式来解决。针对于极耳错位问题,在检测机构实现了厚度的测量后,调试机构根据厚度情况调整工艺参数,实时把控极耳位置情况,并把检测到的极耳位置情况反馈至调试机构,实现极耳位置的质量闭环。
工艺质量学习闭环的应用可以结合材料参数、过程参数、环境参数以及产品质量参数实现生产过程质量闭环。在工艺闭环过程中,控制系统结合工艺参数以及产品质量输出,实现质量过程中的工艺学习闭环。具体表现为控制系统对比厚度、极耳间距以及卷绕参数等工艺信息与产出电芯的极耳位置信息,结合当前控制方式进行深度学习和控制优化。
5 结语
智能卷绕技术的实现需要从内部和外部2个方面进行。在卷绕工艺内部,提升卷绕设备的质量性能,完善实时控制逻辑保证质量闭环。建立理论模型,通过实体模型和虚拟模型的数字连接,达到数字化积累的目的,从积累优化和深度学习中,实现卷绕过程的控制和数据闭环;在卷绕工艺外部,建立工艺间的信息流通,实现设备与设备间的连接以及生产现场数据的实时采集、处理、上传等。同时,在工艺闭环上也通过整体模型优化选择,实现整体制造过程的数据闭环。
具体在极耳错位中表现为,在卷绕设备上,首先需要具备完整的影响因素检测机构,并在卷绕控制系统中搭建信息处理平台,即通过检测出来的厚度以及极耳间距等信息,匹配合适的卷绕参数以及调控方式。再通过最终卷芯中极耳位置质量,修正卷绕过程中的参数以及控制方式,这是可以实现卷绕数据闭环的过程。在工艺上,建立卷绕设备与模切设备的信息流通,加强卷绕与模切单机间的质量关联,即通过二维码等方式,搭建卷绕设备直接获取卷料信息的途径,再将卷绕过程中的质量信息上传并继续传递至下一个工序环节直到形成最终的电池质量信息证件。该质量信息证件需要根据标准规范,确定每个工序需要输出的质量信息,以及在每个工序之间的传递方式。这样既达到了控制质量的目的,也方便了电池质量问题的信息追溯。
总之,智能卷绕技术的发展不仅依赖卷绕技术本身,还基于整个工序间的相互关联。打破工序间的“孤岛效应”。通过标准规范的形式,制定各工序间信息流、物料流和能量流的流通方式,各工序保证输出的信息符合标准即可。建立信息传递标准规范将是实现动力电池智能制造的重要途径,也是实现“黑灯工厂”和产品少人化、自适应、定制化、大规模生产的基础。