装备制造企业以什么样的创新路径来积极应对广大电池制造企业客户的需求?这是摆在所有装备企业面前的一个重要课题。
日前举办的第九届动力电池应用国际峰会(CBIS2024)期间,在由逸飞激光冠名的“先进电池技术及应用”主题论坛上,逸飞激光工程技术研究院总监雷波,作题为《装备研创路径升级 助力电池极致制造与创新拓展》的主题演讲,向与会代表分享了逸飞激光的创新发展经验。

图为逸飞激光工程技术研究院总监雷波作主题演讲
01
电池需求多元化
装备企业挑战与机遇并存
市场方面,随着全场景电动化的开启,动力、储能、小动力、消费电子等不同细分场景的应用特征,带来了不同类别电池产品的差异化需求。如高安全性、低成本、长续航、快充、轻量化、长循环寿命等,这对电池装备制造企业提出了新的挑战。
据雷波介绍,逸飞激光将电池的技术创新,与极限制造方案的创新进行深度耦合,协同打通从技术创新到产业化的路径,推动不同类别电池在生产环节的极限制造,持续助力电池产业进化。
“这需要从不同场景电池的实际需求出发,围绕电池的能量密度、快充、长循环、安全等关键指标,在满足不同电池形态、不同工艺路径、不同封装形式等生产需求的同时,提升生产效率、生产良率、加工质量,并实现极致管控、极限制造。”
迎接新挑战,首先要解决行业痛点。在雷波看来,从电池技术创新到实现极限制造过程中,面临诸多痛点,这主要包括专业领域复杂,技术创新到真正在产品中的应用的周期长、投入高,存在新技术应用滞后性等特征。
为了解决上述痛点,雷波指出,逸飞激光根据差异化的电池需求,打造共性装备及工艺技术的同时,还提供定制化生产设备、柔性化产线配置,实现装备及专用加工系统的模块化、标准化、产品化,并加强系统创新组合。
同时,积极建设工程技术研究平台,加强共性单元技术创新、分析测试及工程验证转化一体化的产业化落地,打通工艺技术与装备技术在电池应用场景的数据链,更好地服务于电池制造场景,助力电池极致制造与创新拓展。
02
构建支撑产业链进化的装备创新路径
资料显示,逸飞激光成立20多年来,一直以创新战略为公司的发展核心,坚持“激光技术、智能装备技术、工艺应用”三维一体的滚动创新模式,持续推动技术创新和产品迭代升级,助力下游客户可持续发展。
对于“装备制造企业以什么样的创新路径来积极应对广大电池制造企业客户的需求?”的问题,雷波表示,逸飞激光通过激光工艺及智能装备创新,结合不同客户、不同电池及装备模式的需求,构建了产业链协同创新平台,推进新技术、新产品的工程转化和规模制造。
雷波分享了逸飞激光产业链协同创新平台的五大“利器”,即系统性研发、制造方案数字化、制造工艺及工程验证、制造品质保障分析测试服务和通用检测服务平台。
值得注意的是,据介绍,逸飞激光的系统性创新研发,是紧跟产业发展趋势的制造装备和技术攻关。主要包括激光系统、智能装备智能激光控制系统、激光加工工艺、系统化智能装备的创新研发及应用,以及面向客户难点的精准定制化研发。
其中,在激光加工工艺创新研发上,逸飞激光取得全新突破。据介绍,其极片涂层激光表面处理技术,可应用于固态电池负极极片激光微加工工艺;电池壳体毛化工艺,能够提高漆层与壳体结合力,优化电芯外壳喷涂工艺;集流盘抑制飞溅焊接工艺,可以提升集流盘焊接质量及合格率。
同时,精准定制化研发也是逸飞激光的一大创新优势,以解决客户的生产难点。
“对于极耳成型的多种路径,如无损整形、切叠、拍平工艺,以及不同的密封钉装配工艺,逸飞激光对加工工艺难点都进行了精准的研发突破,并提供相应的定制化装备解决方案。”
此外,逸飞激光的制造工艺及工程验证平台,可以对电芯、电池模组等进行验证,通过系统分析,对新材料、新结构、新形态、新制造工艺的规模化制造提供数据支撑或优化建议。
资料显示,截至2024年6月末,逸飞激光申请知识产权超1000项,已获授权知识产权577项,其中发明专利86项,实用新型专利324项。
03
逸飞激光产品矩阵
锂电领域,逸飞激光的产品阵容庞大,覆盖各类电芯、模组PACK的组装整线系统方案,以及从前段到后段的智慧物流系统及仓储、智能制造软件系统方案等。
据介绍,逸飞激光在行业内率先突破圆柱全极耳电芯的关键工艺,推出量产系列装备,处于国际领先水平;针对方形电芯的封装,逸飞具备超过15年的工艺创新和装备交付经验,并引领了多项激光工艺在方形电池封装中的应用;针对模组PACK领域,逸飞激光也推出了高柔性的系列化解决方案,具备行业领先水平。
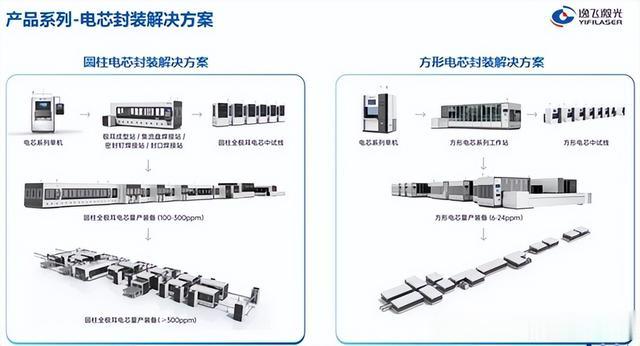
逸飞激光电芯封装解决方案
据介绍,逸飞激光目前在国内已形成6大产业基地布局,以武汉光谷总部为核心,建设了华中基地、华东基地、华南基地以及无锡新聚力、珠海逸科兴。行业应用持续拓展,从新能源电芯到电池系统,再到半导体、医药健康等领域。基于工程技术平台,未来将持续孵化和推出更多先进加工工艺,以及可靠的模块化装备。
雷波表示,“逸飞激光通过对行业应用实践的积累,以及建设电池领域激光应用产业链协同创新平台,能够更好地与客户创新融合,从而让先进加工工艺更可靠,让制造装备更可靠,以加速电池制造领域的智能化升级。”